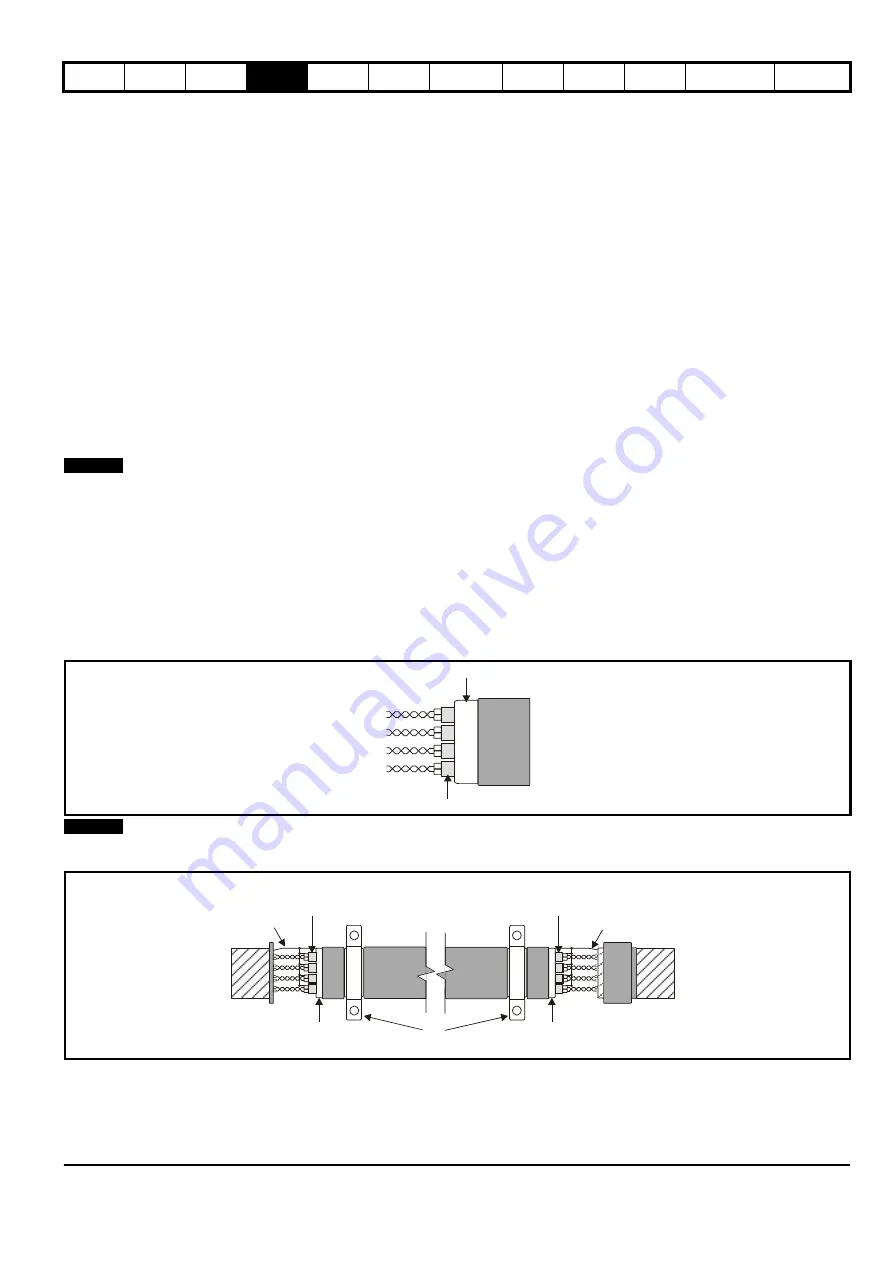
Diagnostics Optimization CT MODBUS RTU Technical Data
E300 Design Guide
79
Issue Number: 1
4.7
Shield, Ground connections
Shielding considerations are important for PWM drive installations due to the high voltages and currents present in the output (motor) circuit with a
very wide frequency spectrum, typically from 0 to 20 MHz.
Resolver connections:
•
Use a cable with an overall shield and twisted pairs for the resolver signals
•
Connect the cable shield to the drive 0 V connection by the shortest possible link (“pigtail”)
•
It is generally preferable not to connect the cable shield to the resolver. However in cases where there is an exceptional level of common-mode
noise voltage present on the resolver body, it may be helpful to connect the shield there. In this case ensure absolute minimum lengths of
“pigtails” are used at both shield connections. Also clamp the cable shield directly to the resolver body and the drive grounding bracket
•
Preferably the cable should not be interrupted. Where interruption is unavoidable, ensure minimal length of “pigtail” shield connections at each
interruption.
Encoder connections:
•
Use a cable with the correct impedance
•
Use a cable with individually shielded twisted pairs
•
Connect the cable shields to 0V at both the drive and the encoder, using the shortest possible links (“pigtails”)
•
Preferably the cable should not be interrupted. If interrupted, ensure the absolute minimum length of “pigtail” in the shield connections at each
interruption. Preferably, use a connection method which provides substantial metallic clamps for the cable shield terminations
The above applies where the encoder body is isolated from the motor and where the encoder circuit is isolated from the encoder body. Where there is
no isolation between the encoder circuits and the motor body, and if in any doubt, the following additional requirement must be observed in the
interests of best possible noise immunity.
•
The shields must be directly clamped to the encoder body (no pigtail) and to the drive grounding bracket. This may be achieved by clamping of
the individual shields or by providing an additional overall shield which is clamped
N
The recommendations of the encoder manufacturer must also be adhered to for the encoder connections.
Motor cable:
Use a motor cable with an overall shield. Connect the shield of the motor cable to the ground terminal of the motor frame using a link
that is as short as possible and not exceeding 50 mm (2 in) long. A full 360 ° termination of the shield to the terminal housing of the motor is beneficial.
Brake resistor cable:
The optional braking resistor should also be wired with shielded cable. If un-shielded wire is required refer to
4.17.5 Shielding requirements for the braking circuit
for guidance.
Control cables (including encoder):
If the control wiring is to leave the enclosure, it must be shielded and the shield(s) clamped to the drive using
the grounding bracket. Remove the outer insulating cover of the cable to ensure the shield(s) make contact with the bracket but keep the shield(s)
intact until as close as possible to the terminals. Refer to
Figure 4-36 Grounding of signal cable shields using the grounding bracket
.
illustrate the preferred construction of cable and the method
of clamping.
Figure 4-14 Feedback cable, twisted pair
N
In order to guarantee maximum noise immunity for any application double shielded cable as shown should be used.
Figure 4-15 Feedback cable connections
Use the grounding bracket and grounding clamp supplied with the drive to terminate all shielded cables at the drive.
NOTE
Twisted
pair
cable
Twisted pair shield
Cable
Cable overall shield
NOTE
Cable
Cable
shield
Twisted
pair
shield
Cable
shield
Twisted
pair
shield
Connection
at motor
Connection
at drive
Ground clamp
on shield
Shield
connection
to 0V
Shield
connection
to 0V
Содержание 03200106
Страница 490: ...0479 0024 01 ...