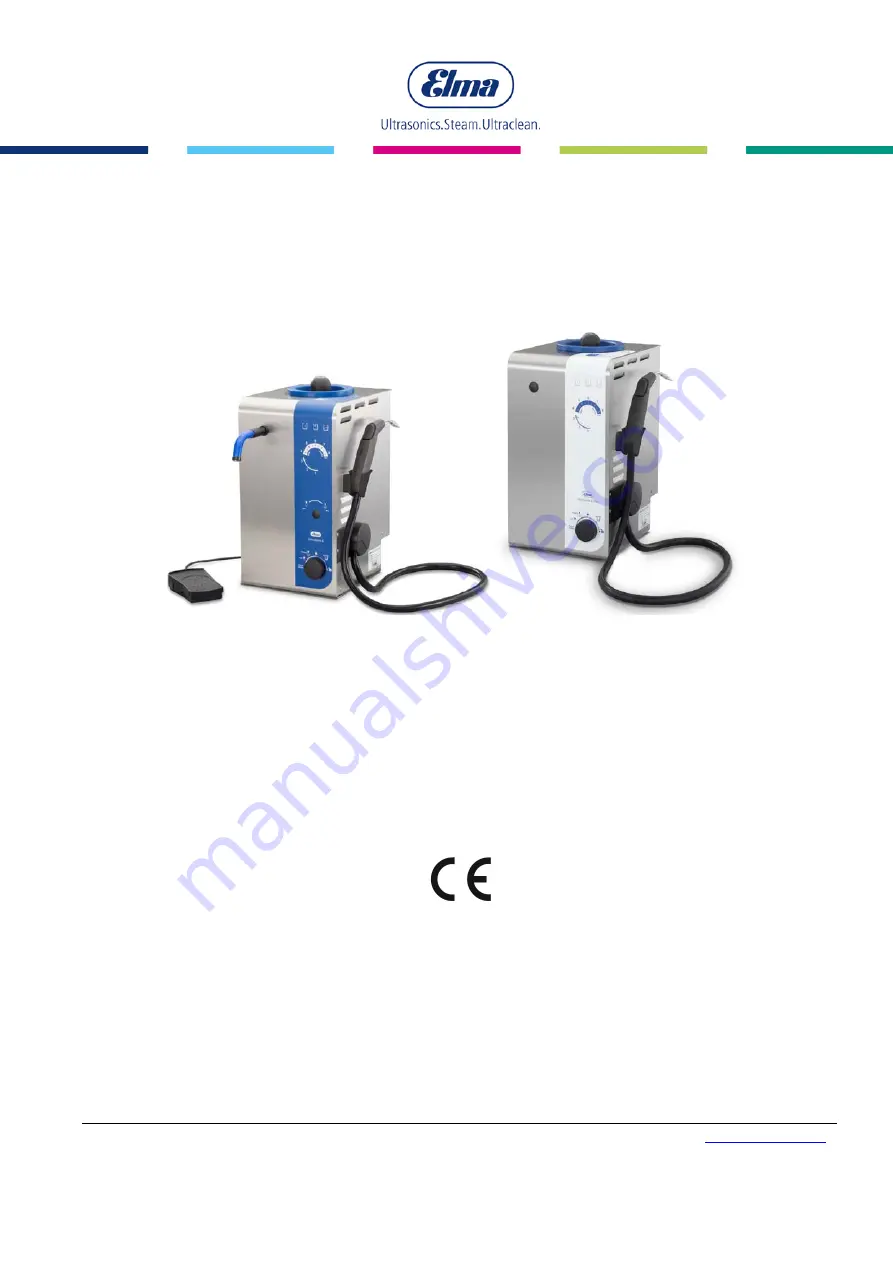
Elma Schmidbauer GmbH Gottlieb-Daimler-Str. 17 D-78224 Singen Tel49 (0) 7731 / 882-0 Fax +49 (0) 7731 / 882-266
document ref. 1076604
Operating Instructions
Elmasteam 8
basic
med
High-performance steam cleaner
English