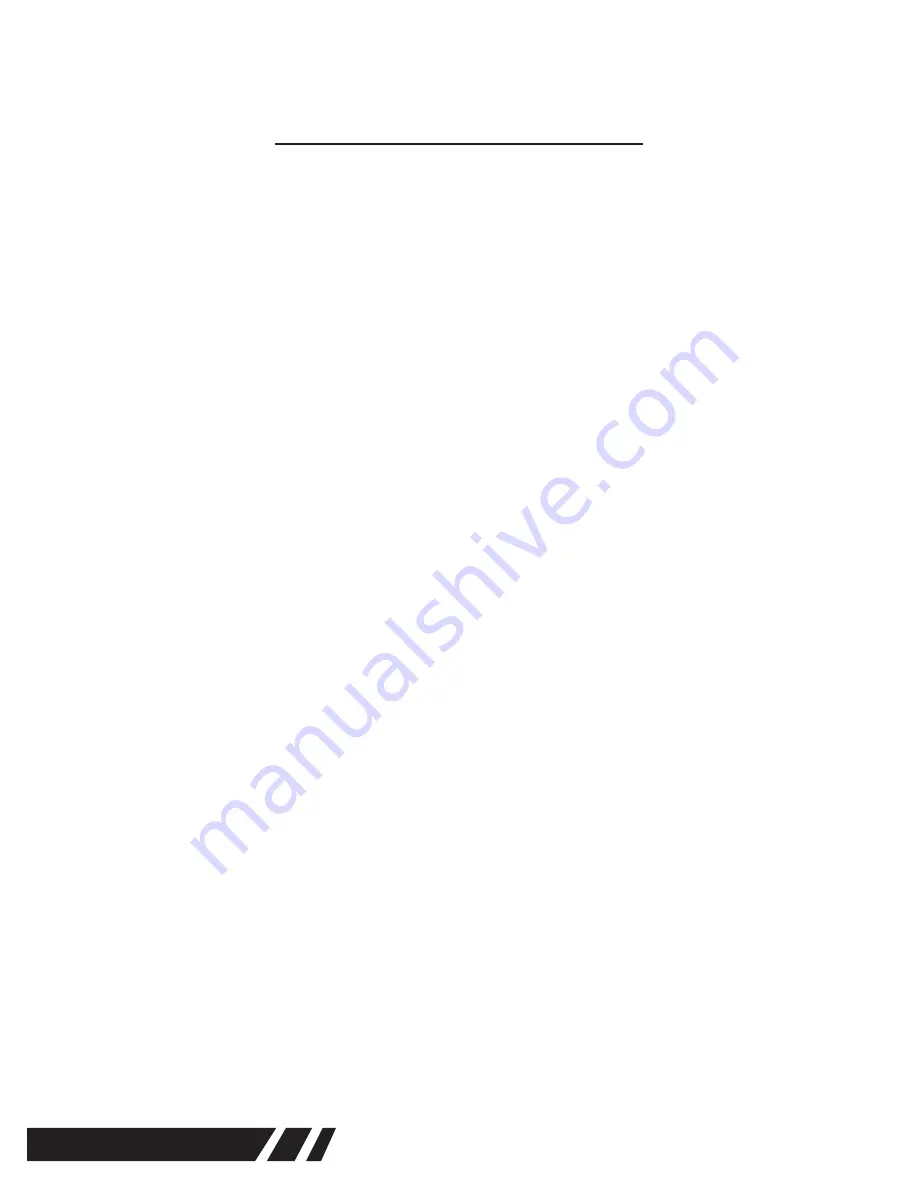
10
ET720 Motor
sERvICE InsTRUCTIOns
Motor Disassembly
Slip the front bearing plate (34) and bearing (33) off the front of the rotor (37) and remove the cylinder
(42) and four (4) rotor blades (36). Set the rear bearing plate assembly (43) on the vise jaws with the
rotor (37) hanging down. Use a 7/32” punch to drive the rotor (37) out of the rear rotor bearing.
Reassembly In General
All parts should be washed in a solvent and inspected for damage or wear. Particular attention should
be given to all bearings, gears, gear pins and rotor blades as failure of these parts could cause
damage to more expensive parts. Rotor blades should be replaced if they measure less than 3/16”
on either end. Inspect and replace any O-rings or seals that show signs of wear or deterioration. All
gears, gear pins and open bearings should receive a generous amount of No.2 Moly grease during
reassembly. When assembling the gear case to the back head, the case should be tightened to a
torque of 300/325 in. lbs. (33.9/36.7 Nm). Do Not Over-tighten, as it can distort the valve assembly
and cause the valve to stick. Reassembly of all of the various sub-assemblies is in the reverse order
of disassembly; however, the following paragraphs list some of the more important reassembly
procedures.
Clutch Assembly
During the reassembly of the spindle/clutch assembly, all parts should receive a thin coating of a
mixture of 10W machine oil and No.2 Moly grease. The clutch (13), retaining ring (12), spring (18),
spring bushing (19), trip (16), balls (17), cam (11) and washer (10) must be in position on the clutch
shaft (14) before installing the spring pin (15). Install the spring pin (15) so it is below the surface at
both ends. The installation of the balls (17) can be simplified by filling the ball slots in the clutch shaft
(14) with grease if desired.
Motor Assembly
Install the rotor bearing (33) into the rear bearing plate (42). Press the rear bearing plate assembly
(press the bearing’s inner race) onto the rear shaft of rotor (37) until there is approximately .001”
clearance between the rear bearing plate (42) and the rotor. Install the cylinder (40) with the slotted end
toward the front and install 4 paddles (36). Install bearing (33) into front bearing plate (34). Press the
front bearing plate assembly (press the bearing’s inner race) onto the front shaft of rotor (37) until there
is approximately .001” clearance between the front bearing plate (34) and the rotor. If a new rotor or
complete motor assembly is to be installed, first use RC609 Loctite when installing a push rod guide
(38) – with the countersunk end in first, and the other end flush with the rear of the rotor shaft.
Содержание ET720-1800
Страница 2: ......
Страница 15: ...This page intentionally left blank...