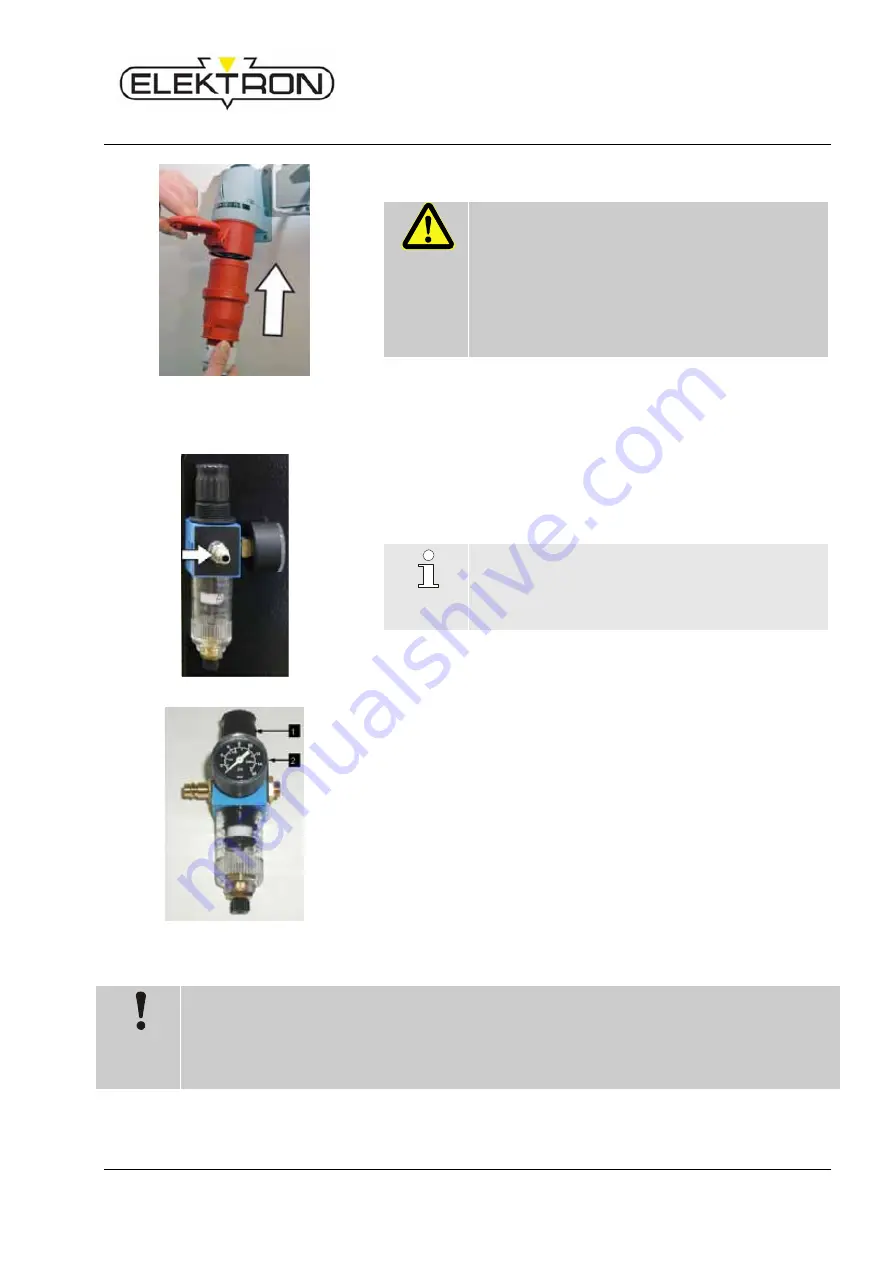
Resistance Welder MULTISPOT MI-90 T
Installation
23
Fig. 15: Connecting welder to power
supply
1.
Take the power cord from its support.
2.
Run the power cord along a safe route.
WARNING
Stumbling hazards
Power cords may constitute a stumbling hazard
when improperly laid or installed and may cause
people to fall and hurt themselves. In this particular
case, the cable could block the wheels of the
welder and make it tip over.
Therefore:
– Run the power cord along a safe route.
3.
Connect the power cord to the mains.
4.
Use strain relief clamps to protect cables.
5.3 Connecting the pneumatics
Fig. 16: Connecting compressed-air
supply
1.
Take the supply line from the pneumatic grid of the plant and
plug it on to the welder (Fig. 16).
2.
The plant's pneumatic mains must provide about 6 bar (87 Psi)
input pressure to the welder.
NOTE
6 bar (87 Psi) input pressure generate a contact
force of the electrodes of 3.5 kN (787 lb f) approx.
To adjust the contact force of the electrodes,
proceed as described below.
Fig. 17: Pressure gauge and pressure
regulator
3.
Check the pressure supplied at the pressure gauge (Fig. 17/2).
If necessary, use the pressure regulator (Fig. 17/1) to set the
pressure as required (depending on welding program and
manufacturer's specs).
– Turn the regulator in the "+" direction to increase the input
pressure.
(
Max. admissible: 10 bar / 145 Psi
)
– Turn the regulator in the "-" direction to decrease the input
pressure.
(
Min. admissible: 6 bar / 57 Psi
)
4.
When decreasing the input pressure, actuate the pliers from
time to time to let the air escape.
CAUTION ! Improper pressure of compressed air may damage property.
Low pressure reduces the contact force of the electrodes which, in turn, increases wear of the
electrodes. High pressure, on the other hand, may damage the spot welding pliers. Therefore:
– Check the pressure gauge before you switch on the welder. Compare to the parameters of
the welding program selected.
– Maintain the pressure between 6 and 10 bar (87 and 145 Psi).