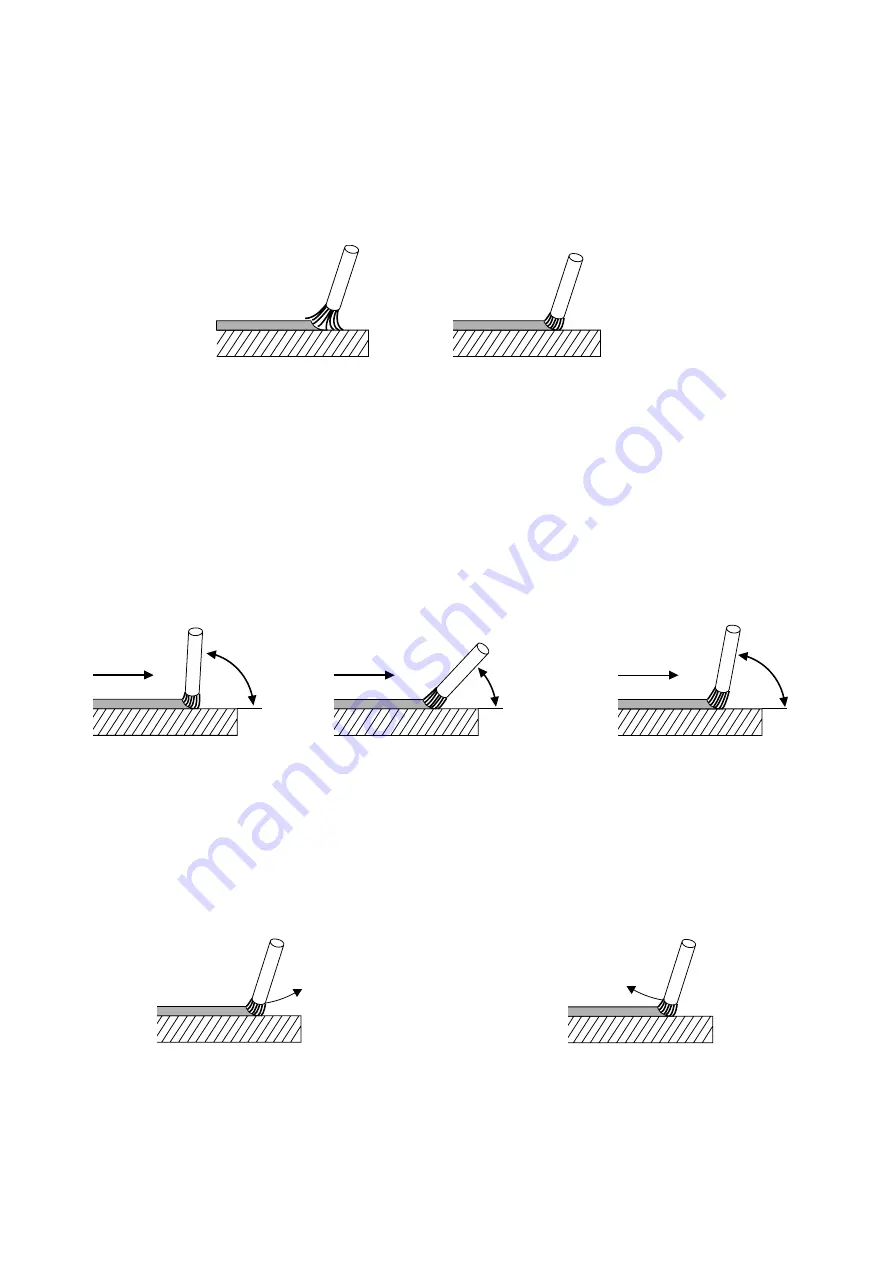
The correct arc length is important for a good weld, because with too short or too long an arc both welding current and
working voltage change. A low working voltage causes insufficient penetration. Too high or too low welding current gives
a poor welding seam. Too long an arc does not sufficiently melt the parent material, resulting in high spatter losses. Also
the air, with its detrimental substances like hydrogen and nitrogen, may get access to the weld pool.
For a good weld the work angle of the electrode (or electrode inclination angle) is of substantial importance. The
inclination should be 70
°
- 80
°
to the welding direction. With the work angle too steep slag will run under the weld pool,
too flat an work angle causes the arc to spatter, in both cases the result is a porous, weak welding seam (see figure
5 - 7).
Welding Hints
Because of the multitude of and great differences in the important points for welding only the very basic operations for
the most common electrodes for low-carbon steels, the rutile or rutile cellulose electrode, are introduced here. In the
case that other electrodes have to be used, the electrode manufacturers supply upon request all relevant information
for the type of special electrode to be used.
Always make some trial welds on scrap material. Select electrode diameter and welding current as per Table 1. Attach
earth clamp to work piece and place electrode into electrode holder as described earlier. Now hold the electrode tip
approx. 2 cm above the starting point of your weld seam. Hold the welding visor in front of your face and draw the
electrode with a short stroke along the groove. Through the welding shield you watch the arc, keeping it to a length of
1 to 1.5 times the electrode diameter.
< 70
°
welding direction
(Figure 6)
(Figure 5)
> 80
°
welding direction
(Figure 7)
70-80
°
welding direction
wrong
wrong
correct
wrong
arc too long
(Figure 3)
correct
approx. 1 - 1.5 the electrode-Ø
(Figure 4)
The welder has to keep the arc at the same length, that is the electrode burn-off is compensated by feeding the electrode
into the weld. At the same time the welder has to watch the weld pool for even penetration and width.
Welding is always done from left to right (backhand welding).
At the end of the welding seam the electrode can not simply be lifted or pulled from the weld, this creates porous end
craters, which weaken the weld. To correctly terminate a weld the electrode is held for a short moment at the end of the
weld seam, then lifted in an arc over the just laid weld.
wrong
(Figure 8)
correct
(Figure 9)
Remove slag only after it has cooled down and is no longer glowing.
If an interrupted weld is to be continued, the slag at the end of the already finished weld must be removed. Then the
arc can be started either in the groove or on the weld, as described earlier, and then moved to the end of the weld, which
has to be thoroughly melted for good fusion. Welding is then continued normally.