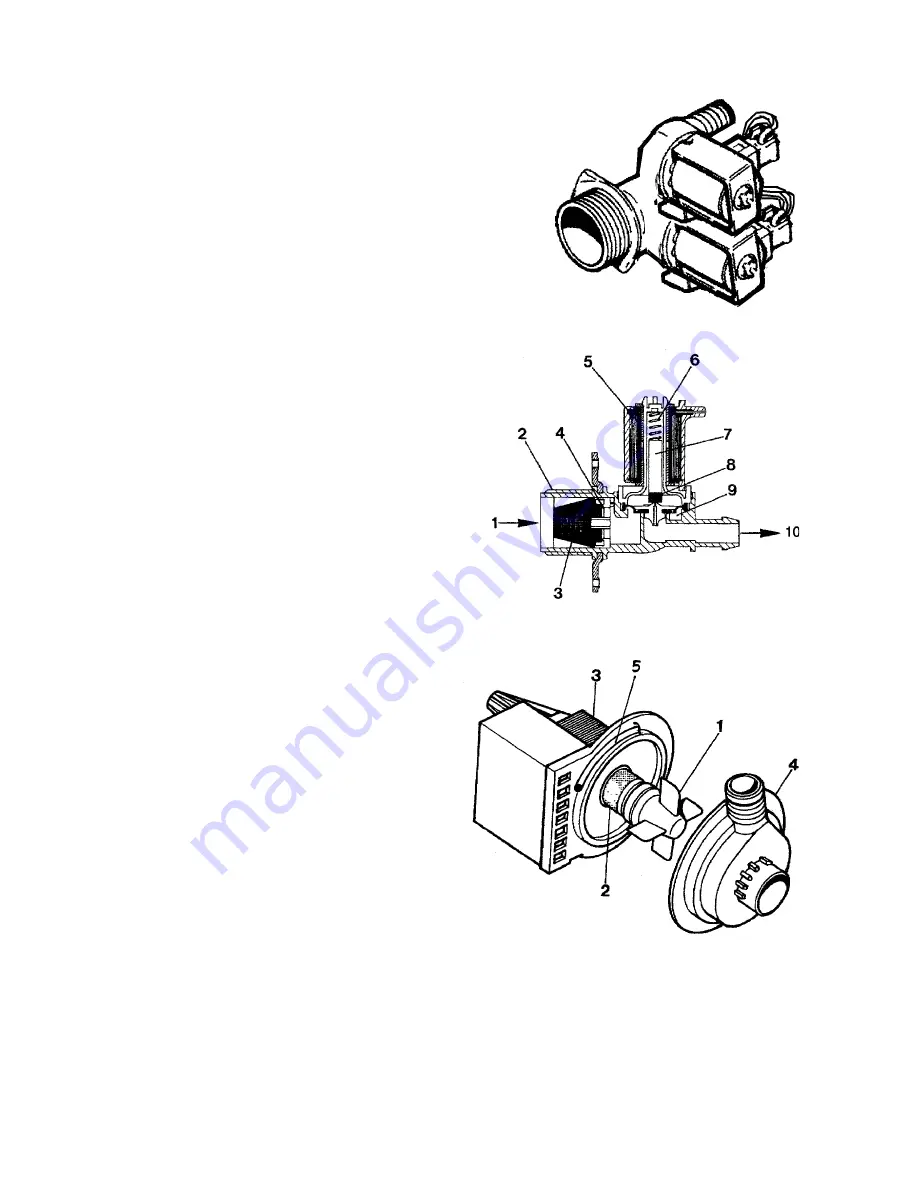
- 16 -
11.2003 R.K.
599 518 544
Double water supply valve
General characteristics
This electro-magnetic controlled valve regulates the supply of water
to the machine. It 1s actuated by a solenold which is controlled by
the electronic module via the level regulator.
When the valve Is inactive, (without voltage) the spring holds the
splndle down and the rubber cone seals a small hole at the centre
of the membrane. A head of water bullds up which holds the
membrane against Its seating and closes the valve.
When voltage 1s applled to the solenold, the splndle with the rubber
cone is drawn up-ward against the spring and the hole in the
membrane 1s exposed, permitting the passage of water. The
pressure differential 1s lost and water can flow freely through the
valve.
1
Water entry
2
Valve housing
3
Filter
4
Flow regulator
5
Coil
6
Spring
7
Spindle
8
Rubber cone
9
Membrane 10 Water delivery
Drainage pump
1
Impeller
2
Rotor
3
Stator
4
Pump housing
5
0-ring
The rotor consists of a permanent magnet which can
rotate clockwise or anti clock-wise. The rotor can
rotate one quarter revolution without movement ofthe
impeller.
Ifthe impeller seizes, the rotor can therefore make
small movements in both directions until the impeller
is freed. An unusual sound may be heard at Start
which is quite normal.
Function check
1 Check that the impeller can move freely.
2 Check the resistance of the Stator winding. This should be 170 Ohm.
Max. capacity= 20 l/mm.
Power consumptlon
= 30 W
Содержание WMD1050
Страница 19: ... 19 10 2003 R K 599 518 355 ...
Страница 35: ...35 ...