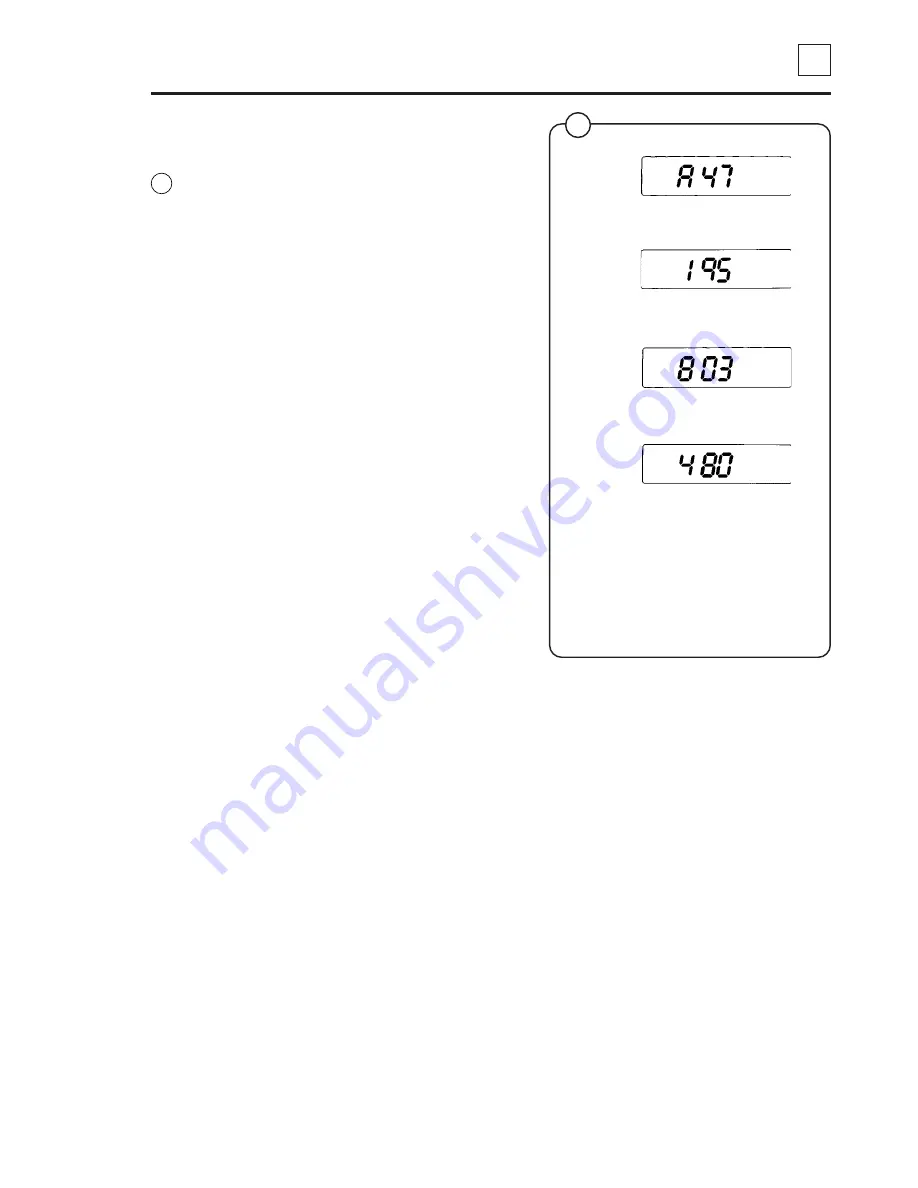
11
23
23. Programme unit
438 9149-81/06
04.03
Service
Manual
Programme memory part number
(service mode only)
•
Depress the service button on the
communication card.
•
Enter code 51 (A47), code 52 (195), code 53
(803) and code 54 (480).
•
The programme memory part number in this
example is A471 958034. The number ’80’ is
an internal revision number.
Fig.
15
15
2238 2237 2236 2235
+
Code 51
Code 52
=
Part number:
A471 958034
Internal rev no.:
80
Code 53
Code 54
+
+
Содержание W3105H
Страница 1: ...Service Manual W365H W375H W3105H W3130H W3180H W3240H W3300H Exacta 438 9201 81 EN 06 42 ...
Страница 2: ......
Страница 4: ......
Страница 5: ...438 9144 41 01 00 23 1 1 1 Safety precautions Service Manual Contents Safety precautions 3 Warnings 3 ...
Страница 6: ......
Страница 8: ......
Страница 9: ...2 Technical data 438 9144 61 02 03 20 Contents Technical data 3 Physical features 3 Connections 4 ...
Страница 10: ......
Страница 14: ......
Страница 22: ......
Страница 23: ...11 Regular maintenance 438 9145 01 01 00 23 Contents Daily 3 Every third month 3 ...
Страница 24: ......
Страница 28: ......
Страница 66: ......
Страница 74: ......
Страница 76: ......
Страница 100: ......
Страница 102: ......
Страница 122: ......
Страница 142: ......
Страница 143: ...38 Drain valve 438 9146 01 01 00 23 Contents Description 3 Function 3 Repairs 4 Disassembly 4 Assembling 5 ...
Страница 144: ......
Страница 148: ......
Страница 149: ...39 Detergent compartment 438 9146 21 01 00 23 Contents Description 3 ...
Страница 150: ......
Страница 152: ......
Страница 154: ......
Страница 158: ......
Страница 160: ......
Страница 164: ......
Страница 165: ...43 Frame 438 9146 61 01 00 23 Contents Description 3 ...
Страница 166: ......
Страница 168: ......
Страница 169: ......
Страница 170: ...www electrolux com professional Share more of our thinking at www electrolux com ...