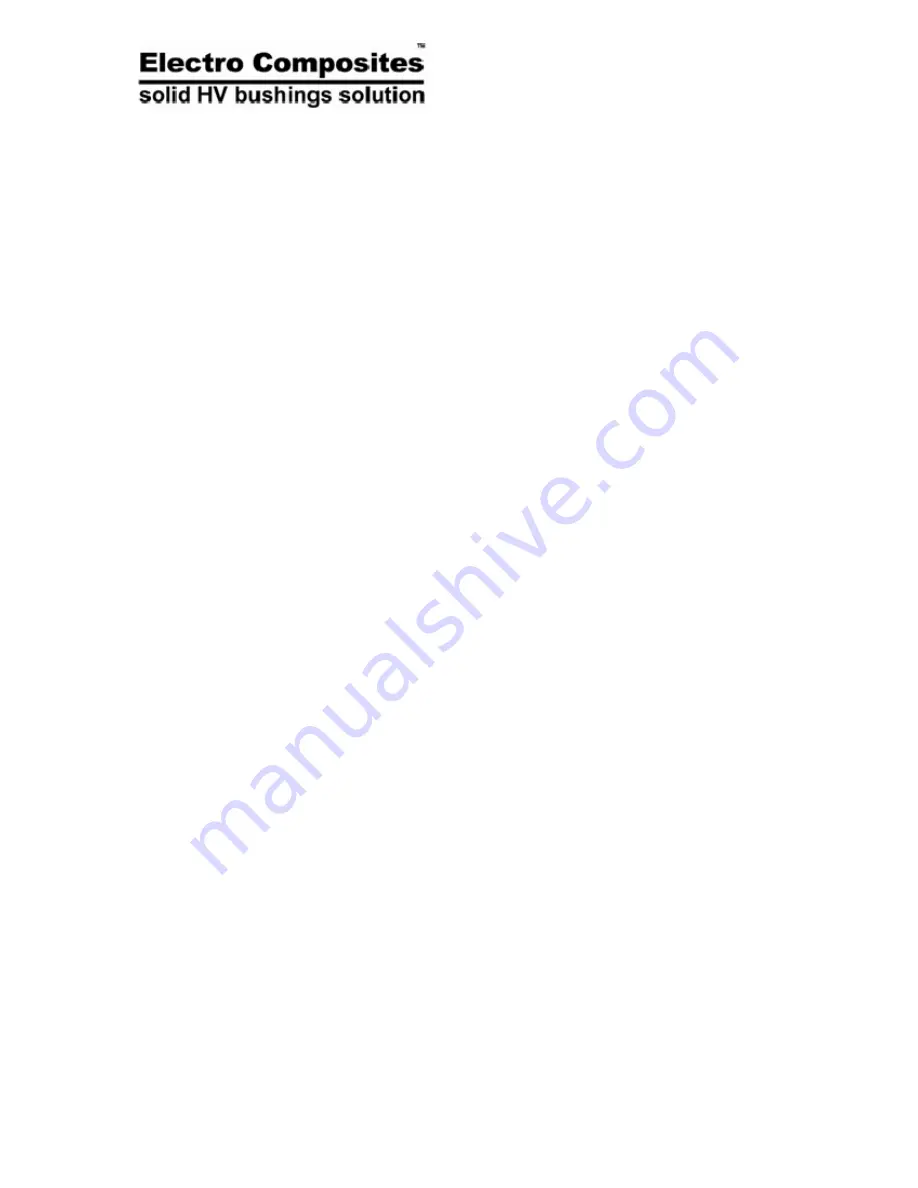
Page
11
of
12
MAINTENANCE
ELECTRO COMPOSITES (2008) ULC bushings are designed for outdoor, severe
condition service with minimal maintenance requirements. The only serviceable
components on SDC
TM
bushing are the test tap and removable threaded terminals on
draw-lead type designs. However, bushings exposed to salt spray, cement dust or other
abnormal deposits must be cleaned regularly to prevent flashover and corrosion of metal
parts. Cleaning should be done before performing routine power factor and capacitance
measurements (bushings with a capacitance tap only).
AFTER 1 MONTH OF SERVICE AND YEARLY
Check the bushing insulation (epoxy part) for signs of cracks or chips and surface
contamination deposits. Should treeing be visible, clean the affected area with isopropyl
alcohol. Insure all connectors are tight and there are no loose components. Inspect the
bushing with an IR camera to determine if there is a hot spot, which would be indicative
of a bad or loose connection.
ONCE EVERY 3 TO 5 YEARS
Perform the yearly maintenance check and cleaning. Perform a Doble test for Power
Factor and Capacitance. Refer to the Doble M-4000 test set instructions, Doble Bushing
Field Test Guide, and ELECTRO COMPOSITES (2008) ULC instructions for proper test
procedures. Refer to values measured at bushing receiving for baseline value. See
INSTALLATION/TESTING section in this document.
FIELD REPAIRS
Any damage to a bushing, which might make repair either desirable or necessary,
should be reported to ELECTRO COMPOSITES (2008) ULC. Typically, a small chip at
the end of a shed will have very little effect on the bushing’s function. Do not try to fill
chips with epoxy, as this will have no beneficial effects. For small chips, simply sands
down the sharp edges with a fine grit sandpaper. Since the bushing insulation is
essentially a solid epoxy casting, chips in the insulation surface will not cause any
moisture problems. Should a crack be found, DO NOT ATTEMPT TO REPAIR THE
BUSHING AND NOTIFY ELECTRO COMPOSITES (2008) ULC IMMEDIATELY.