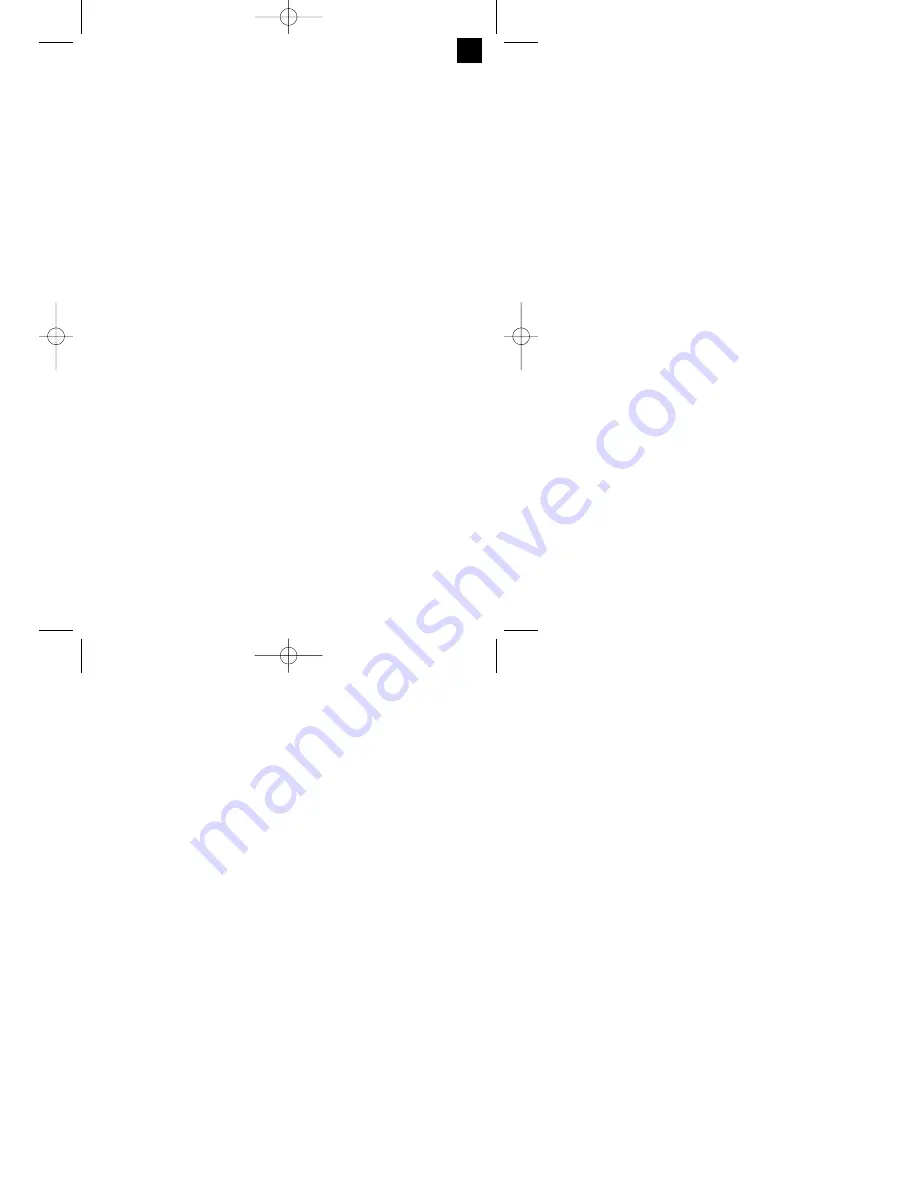
the equipment is used over a prolonged period or
is not properly guided and maintained.
6. Before starting the equipment
6.1 General information
Before commissioning the machine, it must be
firmly mounted on a workbench or similar.
For
this pull the four rubber stoppers (32) from the
bottom side of the saw (Figure 6) and insert 4
screws through the feets to fix it on a stable
surface.
All covers and safety devices have to be properly
fitted before the machine is switched on.
It must be possible for the blade to run freely.
When working with wood that has been
processed before, watch out for foreign bodies
such as nails or screws, etc.
Before you actuate the On/Off switch, make sure
that the saw blade is correctly fitted and that the
machine’s moving parts run smoothly.
Check that the voltage on the rating plate is the
same as your supply voltage before you connect
the machine to the power supply.
6.2 Assembling the saw (Fig. 1-3; 5)
To adjust the turntable (17), loosen the locking
grip (14) by approx. 2 turns, which frees the
turntable (17).
Press the latched position lever (13), turn the
turntable (17) and scale pointer (15) to the
desired angular setting on the dial (16) and lock
into place with the locking grip (14). The saw has
locking positions at angles of - -45°, -30°, -22.5°, -
15°, 0°, 15°, 22.5°, 30°, 45° and 60°, at which you
can engage the latched position lever.
To release the saw from its position at the bottom,
pull the fastening bolt (27) out of the motor
mounting while pressing down lightly on the
machine head (4). Turn the fastening bolt (27)
through 90° before releasing it, so that the saw
remains unlocked.
Swing the machine head (4) up until the release
lever (3) latches into place.
The clamping devices (8, 21) can be fitted on the
left or right of the fixed saw table (18).
Undo the locking screws for the roll base (30).
Guide roll base with limit stop (9) over one of the
holding bars for the roll base (10) and install on
the fixed saw table (18), tightening the
appropriate locking screw (30) (Figure 5).
Mount the second holding bar for the roll base
(10) on the opposite side of the saw and secure
with the appropriate locking screw (30).
When the locking screw (22) is loosened, you can
tilt the machine head (4) to the left by up to 45°.
The foot (32) will prevent the saw from tipping
forwards during operation. Turn out the foot (32)
until it touches the surface on which the saw is
standing.
6.3 Precision adjustment of the stop for crosscut
90° (Fig. 1, 7-9)
Fasten the turntable (17) in 0° position.
Undo the locking screw (22) and move the
machine head (4) all the way to the right using the
handle (1).
Place the 90° angular stop (a) between the blade
(7) and the turntable (17).
Adjust the adjustment screw (38) until the angle
between the blade (7) and the turntable (17)
equals 90°.
Finally, check the position of the pointer (20) on
the scale (19). If necessary, release the pointer
(20) with a crosstip screwdriver, move to the 0°
position of the scale (19) and retighten the
holding screw.
No stop angle included.
6.4 Precision adjustment of the stop for miter cut
45° (Fig. 1, 25, 10, 11)
Fasten the turntable (17) in 0° position.
Undo the locking screw (22) and move the
machine head (4) all the way to the left using the
handle (1), until it coincides at 45°.
Place the 45° stop angle (b) between the blade
(7) and the turntable (17).
Adjust the adjustment screw (37) so that the
angle between the blade (7) and the turntable
(17) equals exactly 45°.
No stop angle included.
7. Operation as wood/plastics saw
7.1 Cross cut 90° and turntable 0° (Fig. 1-3, 12)
For cutting widths up to approx. 100 mm it is possible
to fix the saw’s drag function with the locking screw
for drag guide (25) in rear position. If the cutting width
exceeds 100 mm you must ensure that the locking
screw for drag guide (25) is slackened and that the
machine head (4) can be moved.
Move the machine head (4) to its upper position.
Use the handle (1) to push back the machine
head (4) and fix it in this position if required
(dependent on the cutting width).
Place the piece of wood to be cut at the stop rail
(11) and on the turntable (17).
Lock the material with the clamping device (8) on
the fixed saw table (18) to prevent the material
from moving during the cutting operation.
11
GB
Anleitung_RT_XM_305_SPK7:_ 22.06.2010 15:46 Uhr Seite 11
Содержание RT-XM 305
Страница 5: ...5 10 11 17 7 b 37 O 19 20 12 13 15 14 Anleitung_RT_XM_305_SPK7 _ 22 06 2010 15 46 Uhr Seite 5 ...
Страница 7: ...7 22 24 23 21 29 25 24 7 8 Anleitung_RT_XM_305_SPK7 _ 22 06 2010 15 46 Uhr Seite 7 ...
Страница 16: ...EH 04 2012 02 Anleitung_RT_XM_305_SPK7 _ 22 06 2010 15 46 Uhr Seite 20 ...