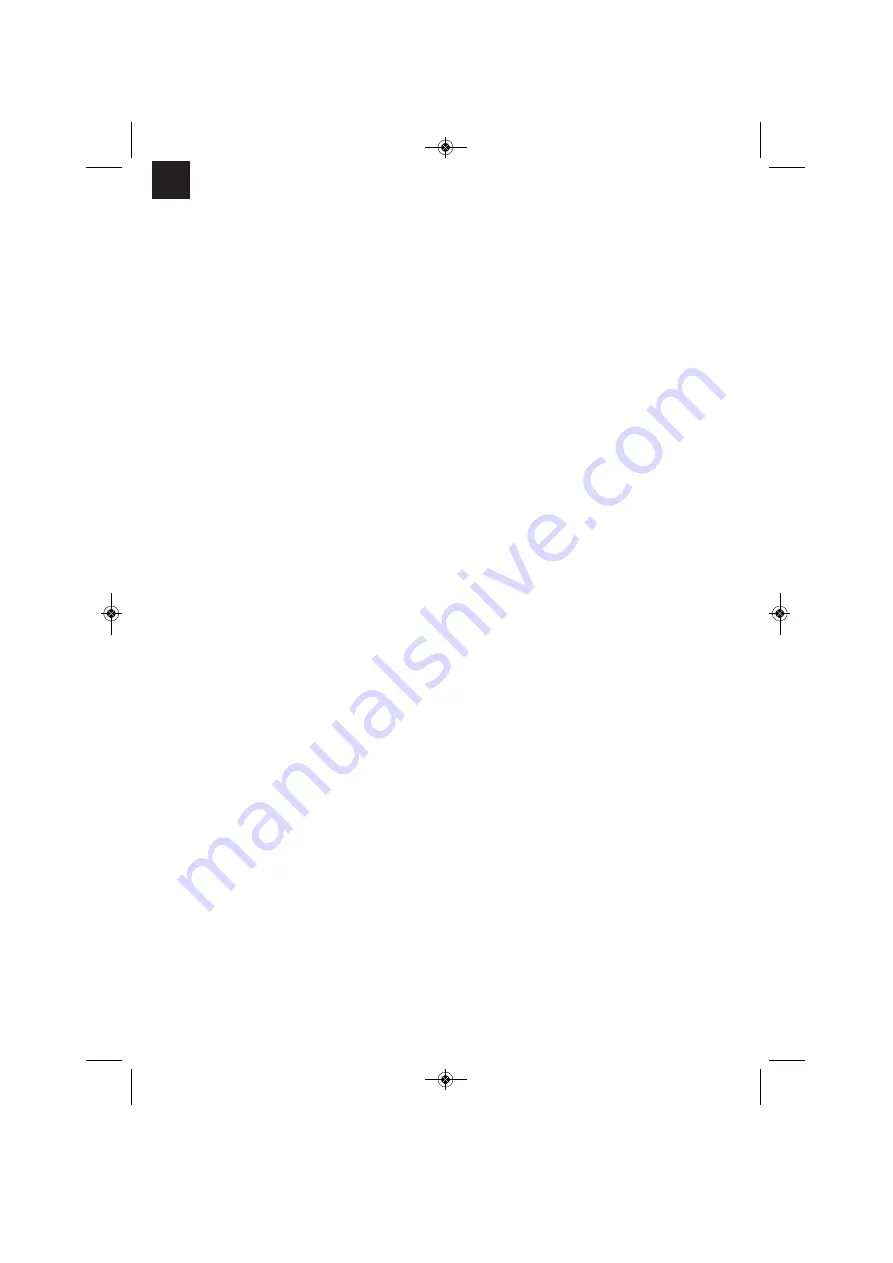
12
GB
two guide grooves. Turn the feed roller (G) over
if necessary or replace it. (Fig. 19).
n
Position the feed roller holder (F) again and
secure it.
n
Remove the gas nozzle (Fig. 2/10) from the
burner (Fig. 2/11) by turning it clockwise,
unscrew the contact tube (Fig. 3/15). (Fig. 2 – 3).
Place the hose package (Fig. 1/9) on the floor as
straight as possible pointing away from the
welding set.
n
Cut off the first 10 cm of the welding wire to
produce a straight cut with no shoulders, warping
or dirt. Deburr the end of the welding wire.
n
Push the welding wire through the guide tube (C)
between the pressure and feed rollers (G/I) into
the hose package mounting (H). (Fig. 20)
Carefully push the welding wire by hand into the
hose package until it projects out of the hose
package by approx. 1 cm at the burner (Fig.
2/11).
n
Undo the adjusting screw for counter-pressure
(L) a few turns. (Fig. 22).
n
Push the pressure roller holder (J) with pressure
roller (I) and pressure roller spring (K) upwards
again and attach the pressure roller spring (K) to
the adjusting screw for counter-pressure (L)
again (Fig. 21).
n
Now set the adjusting screw for counter-pressure
(L) so that the welding wire is positioned firmly
between the pressure roller (I) and feed roller (G)
without being crushed. (Fig. 22).
n
Screw the appropriate contact tube (Fig. 3/15) for
the welding wire diameter on to the burner (Fig.
2/11) and fit the gas nozzle(Fig. 2/10), turning it
clockwise.
n
Set the adjusting screw for the roller brake (D) so
that the wire can still be moved and the roller
stops automatically after the wire guide has been
braked.
6. Operation
6.1 Setting
Since the welding set must be set to suit the specific
application, we recommend that the settings be
made on the basis of a test weld.
6.1.1 Setting the welding current
The welding current can be set to 2 different levels
using the welding current adjustment switch (Fig.
1/6). The required welding current depends on the
material thickness, the required penetration depth
and the welding wire diameter.
6.1.2 Setting the wire feed speed
The wire feed speed is automatically adjusted to the
current setting. The final wire feed speed setting can
be made on the welding wire speed controller (Fig.
1/5). It is advisable to start with the medium setting
and to re-adjust the speed as necessary. The
required quantity of wire depends on the material
thickness, the penetration depth, the welding wire
diameter and also the size of the gap to be bridged
between the workpieces you wish to weld.
6.2 Electrical connection
6.2.1 Mains connection
See point 5.2
6.2.2 Connecting the earth terminal (Fig. 1/8)
Connect the welding set’s earth terminal (8) in the
immediate vicinity of the welding position if possible.
Ensure that the contact point is bare metal.
6.3 Welding
When all the electrical connections for the power
supply and welding current circuit have been made,
you can proceed as follows:
The workpieces for welding must be clear of paint,
metallic coatings, dirt, rust, grease and moisture in
the area where they are to be welded.
Set the welding current and wire feed (see 6.1.1 –
6.1.3) as required.
Hold the welding screen (Fig. 4/13) in front of your
face and move the welding nozzle to the point on the
workpiece where you wish to complete the weld.
Now press the burner switch (Fig. 2/14).
Anleitung_BT_FW_100_GB_SPK7__ 13.03.13 13:12 Seite 12
Содержание BT-FW 100
Страница 5: ...5 17 I K J 18 E E F 16 K 19 G 20 C H 21 K J I L Anleitung_BT_FW_100_GB_SPK7__ 13 03 13 13 12 Seite 5...
Страница 6: ...6 22 L Anleitung_BT_FW_100_GB_SPK7__ 13 03 13 13 12 Seite 6...
Страница 18: ...18 Anleitung_BT_FW_100_GB_SPK7__ 13 03 13 13 12 Seite 18...
Страница 20: ...EH 03 2013 01 Anleitung_BT_FW_100_GB_SPK7__ 13 03 13 13 12 Seite 20...