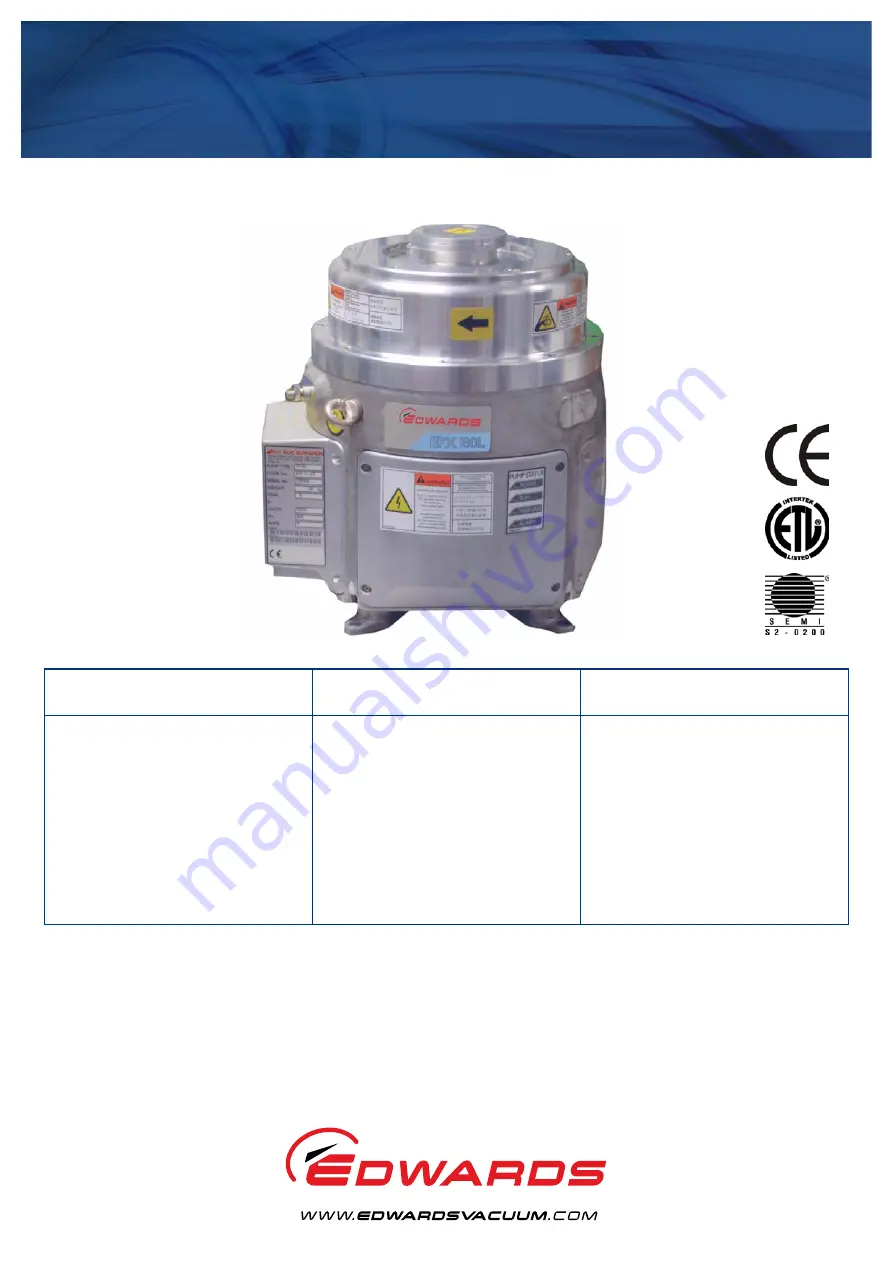
A419-00-880
Issue F Original
Instruction Manual
EPX HiVac Series Dry Vacuum Pumps
Description
EPX
EPX TWIN
Item Number
Item Number
EPX180L
A419-41-xxx
A419-61-xxx
EPX180N
A419-42-xxx
A419-62-xxx
EPX180LE
A419-43-xxx
A419-63-xxx
EPX180NE
A419-44-xxx
A419-64-xxx
EPX500L
A419-51-xxx
A419-71-xxx
EPX500N
A419-52-xxx
A419-72-xxx
EPX500LE
A419-53-xxx
A419-73-xxx
EPX500NE
A419-54-xxx
A419-74-xxx