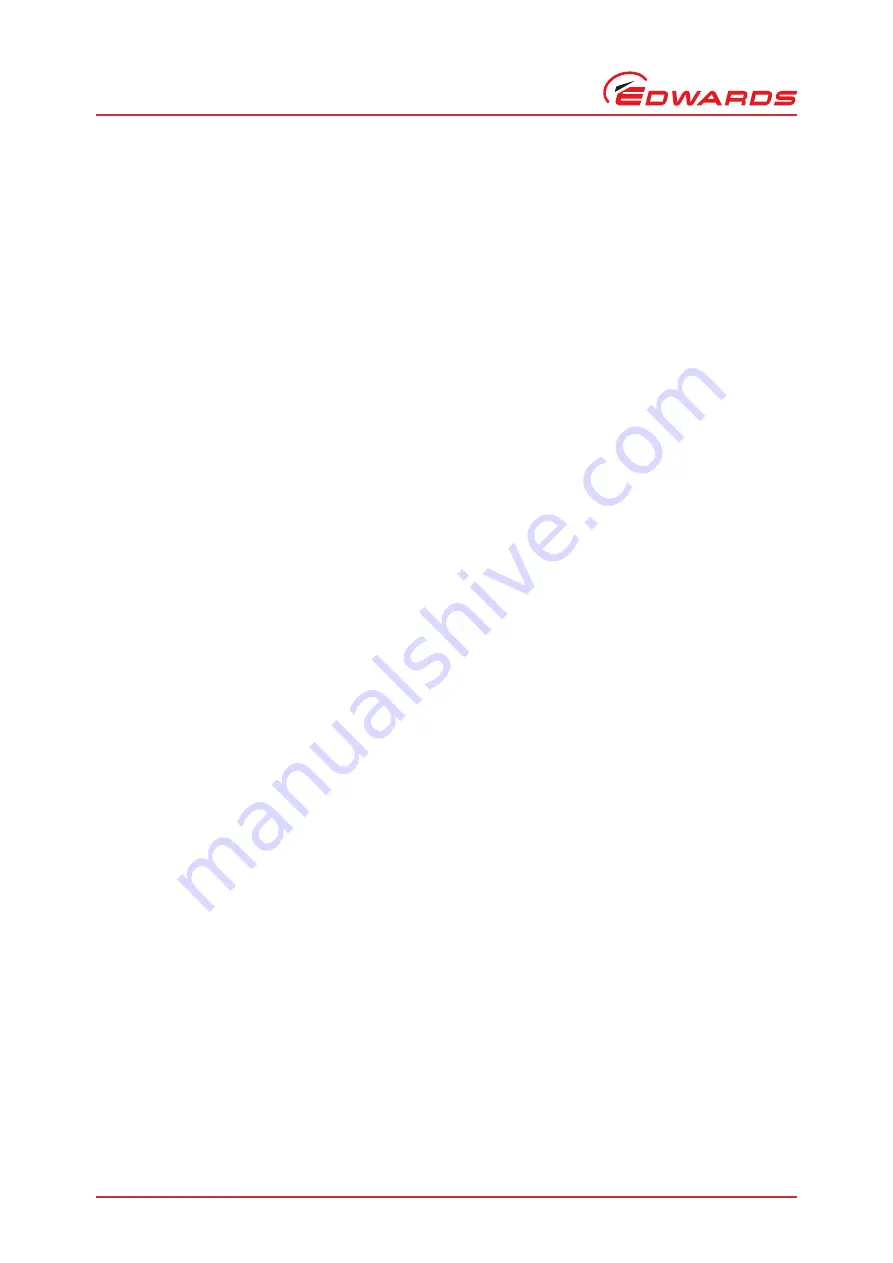
A371–22–880 Issue R
Page 30
© Edwards Limited 2013. All rights reserved.
Edwards and the Edwards logo are trademarks of Edwards Limited.
Service, spares and accessories
7.4.7
Outlet mist filter
The outlet mist filter separates and traps oil droplets to prevent oil mist discharge from the pump outlet.
7.4.8
Oil drain extension
Fit the oil drain extension between the oil drain port on the pump and the oil drain-plug to make the drainage of oil
from the pump easier. The pack includes an oil drain extension tube for use when oil is gravity drained.
7.4.9
Vibration isolators
The vibration isolators reduce transmission vibration and noise when the pump is floor or frame mounted, and helps
to reduce strain when the mounting area is uneven.
7.4.10
Pump inlet or outlet NW25 adaptor
This is a
3
/
8
inch BSP to NW25 adaptor, supplied with connection hardware. Use this adaptor when the NW10 adaptor
fitted to the pump-inlet or the outlet-nozzle fitted to the pump outlet are removed, to adapt the
3
/
8
inch BSP thread
to NW25.
7.4.11
Solenoid operated gas-ballast control valve
The valve provides remote or automatic on/off control of gas-ballast. The valve can be connected to shut-off ballast
to prevent the return of air to the vacuum system when the pump is switched off.
7.4.12
Solenoid operated pipeline valve
Fit the pipeline valve between your vacuum system and the pump inlet to provide additional system protection when
the pump is switched off.