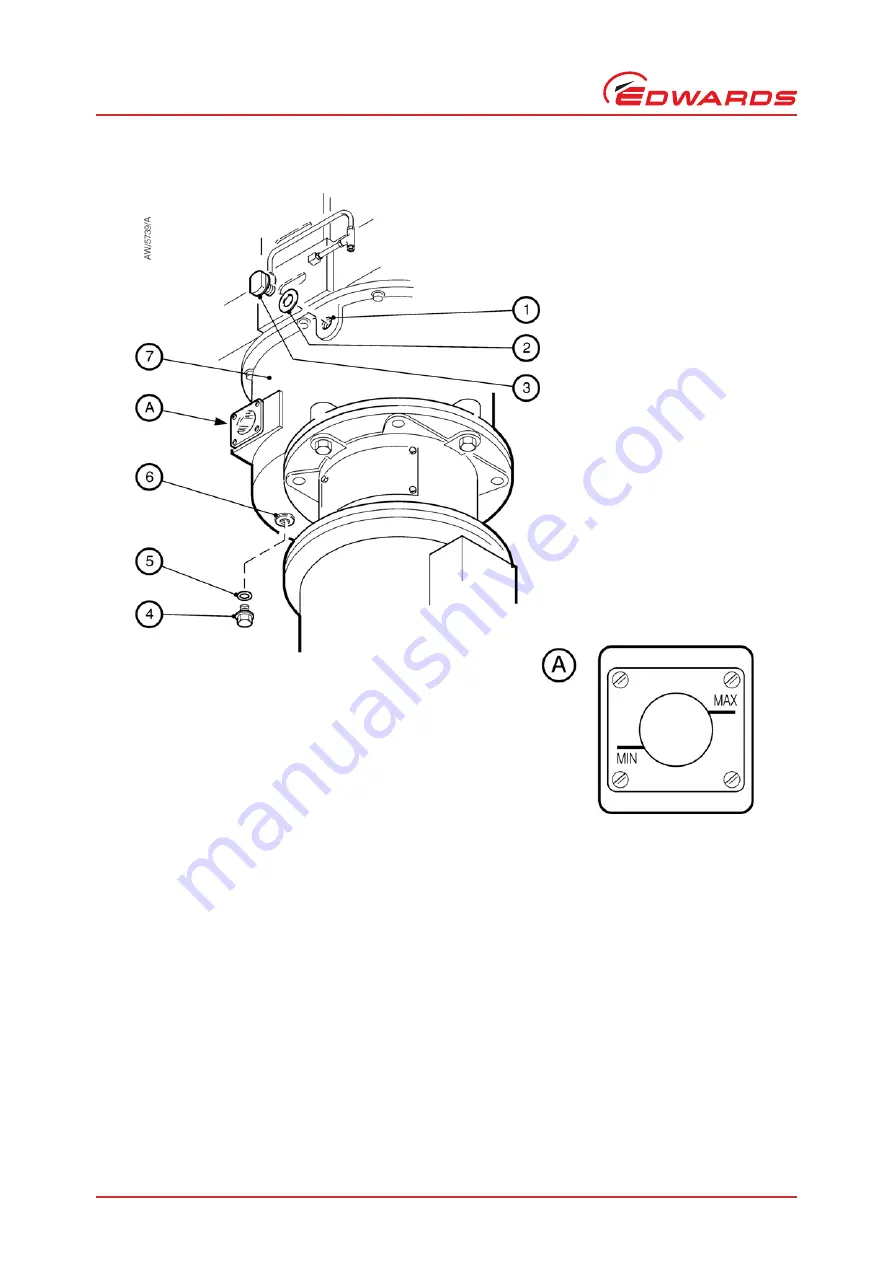
A705-40-880 Issue B
Page 38
© Edwards Limited 2011. All rights reserved.
Edwards and the Edwards logo are trademarks of Edwards Limited.
Maintenance
Figure 6 - Oil-level sight-glass and oil filling and draining connections
1. Oil filler-port
2. Bonded seal
3. Oil filler-plug
4. Oil drain-plug (1/2 BSP)
5. Bonded seal
6. Oil drain-port
7. Gearbox
A. Oil-level sight-glass