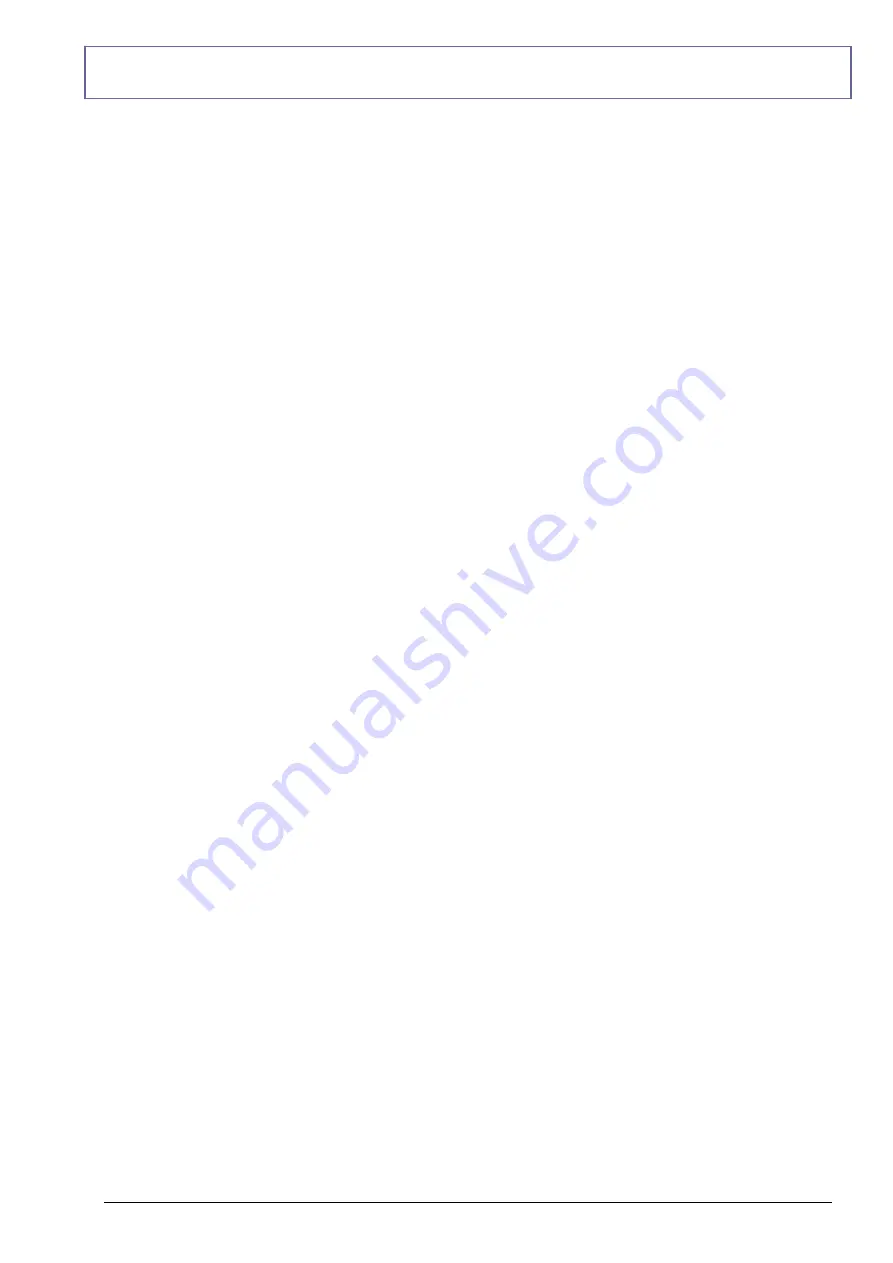
The data, information and descriptions, and the technology described herein are the exclusive intellectual property of Ecotechnics S.p.A. and constitute industrial
secrets. Said information is communicated in strict confidentiality; said information may be used only for the purpose for which it is communicated; said information
may not be divulged, communicated, or revealed to third parties and/or reproduced by any means for any reason whatsoever; said information is protected under
applicable Italian competition and industrial property law.
Service manual VA500-VA750 ed.1 ver.5.05 [MANU360.SA0].doc
pag.7 - 18/10/2005
OPERATING CYCLE
The operating cycle is divided into three distinct phases: the recovery-recycling phase with the
automatic draining of used oil, the vacuum phase, the oil and refrigerant recharging phase.
RECOVERY-RECYCLING PHASE
After carrying out the necessary connections to the vehicle’s air conditioning system and
selecting the phase, if gas is present the machine will begin recovery. There follows a detailed
description of the system. We will follow the path taken by the gas on the enclosed hydraulic
diagram: during this phase the EV1 solenoid valve is open, and the compressor (14) and
electric fan (26) are also in operation. For this to occur, it is necessary that the gas pressure,
visible on the manometer, is sufficient (+0.5 bar) to close the electrical contact at the pressure
switch (7) connected to the distributor. Under these conditions, the flow arriving from the air
conditioning system through the mechanical filters (8), which retains any solid residue, reaches
the evaporator (9) after passing through the EV1 solenoid valve.
From the evaporator, the gas moves past the check valve n°1 (11) and the low pressure filter
(12) until it reaches the compressor (14). The filter mentioned is a high capacity dehydrating
filter (between 10 and 12 ppm per kg of refrigerant in relation to the type of refrigerant and the
temperature of the fluid).
When it leaves the compressor the refrigerant, in a superheated vapour state, arrives at the
separator. In its new configuration this cylindrically-shaped component has three connectors on
the upper part, with a safety pressure switch (16) connected to one of them. This is normally
closed and will open the electrical contact, disconnecting the power supply to the compressor,
if the delivery pressure of the compressor should exceed around 17.5 bar. The compressor is
a 12 cc displacement reciprocating compressor and has three connections: on one side are the
suction and delivery connections, on the opposite side is a connection used for returning the oil
from the separator (15).
There follows a detailed description of the separator: during compressor operation obviously
part of the oil enters into circulation with the refrigerant, therefore it is necessary to make sure
that this oil returns to the compressor so that its functionality is not compromised. In
correspondence with the central connector, the separator has a pure borosilicate coalescent
filter with over 99% efficiency, which causes the oil molecules to coacervate as an effect of the
excitation produced by passing over the filter. In this way, gravity causes the drops of oil to
deposit on the bottom of the bottle and then return to the compressor, at the end of the
recovery phase, when the EV3 solenoid valve is opened.
After coming out of the separator, the superheated gas goes through the check valve n°2 (17)
and returns to the evaporator. When it comes out of the evaporator, the refrigerant goes to the
condenser (27) where it completely passes to a liquid state, transferring heat to the air flow
produced by the electric fan (26). In its now liquid state, the refrigerant then goes through filter
(30), which has the same characteristics as filter (12), and passes through the humidity
indicator (31), the check valve n°3 (32) which stop the gas from the bottle (33) returning, even if
the pressure rises to a relatively high level as an effect of the automatic heating element
resistance (ONLY MODEL XK360), not illustrated.
There is also a bottle manometer (22) and a pressure switch (21) (ONLY MODEL XK360) for
the bottle heater. When the pressure descends below 6 bar, the electrical heating element is
triggered until a pressure of 8 bar is reached.
Finally we arrive to the bottle (33) through the vapour side valve.