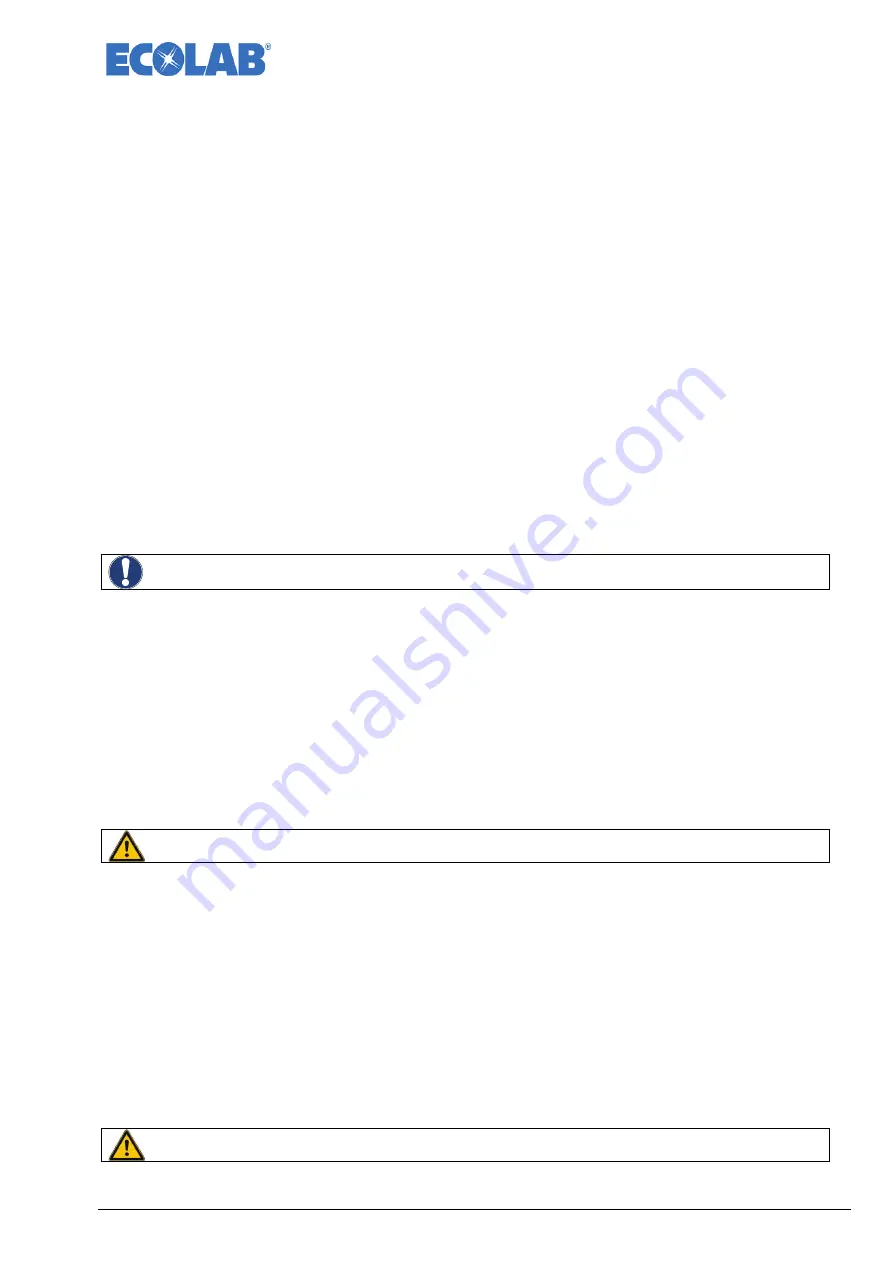
417101634_Lubo-DryExx_Advanced
- 51 -
Rev. 07-01.15
8.
First Use
Following installation and supply of the connections,
DryExx
®
the following steps are to
be followed to bring it into use:
8.1
Electrical Connection
If the metering station and control unit are not supplied from the factory on a standard
console ready for connection, then all electrical connections shown in the connection
diagram, cable lists and circuit diagram of the
DryExx
®
control unit must be supplied.
Before the master switch is switched on, ensure that voltage and frequency supplied
match the information on the appliance rating plate.
8.2
Chemical connection
By using the hose (12/21 PVC fabric), connect the suction lance to the suction
connection of the metering station.
Connect the return hose (12/21 PVC fabric) to the return connection of the diaphragm
valve by means of the hose clamp.
Lead the return hose alongside the suction hose to the suction lance and connect it
with cable ties. The hose end should be placed halfway up the level of suction lance.
Place the suction lance with the return hose into the product container.
Connect the empty detector unit plug from the suction lance to the control unit.
CAUTION
Ensure that here are no blockages in the return hose and ensure that the hose is not
kinked and that it is routed back to the hopper reservoir with a free downwards gradient!
8.3
Filling the supply system
Set the compressed air filter regulator for the controlling air pressure for the pump to
approx. 3 - 3.5 bar.
Starting of the application by activation of the individual lubrication circuits via the
manual booster function of the control unit (see Functional Description Control Unit).
Restarting of "booster phase" until the conveyor belt lubricant comes out of nozzles.
This process is to be repeated for each lubrication circuit until the whole system has
been purged of air.
Optimising the setting of the working air pressure of the pump, so that the nozzles
produce the correct spray pattern.
WARNING
When carrying out refilling, initial-use and installation optimisation operations ensure
that no conveyor belt lubricant is allowed to drip onto the floor.
8.4
Automatic Operation
Items 7.1 - 7.3 have been completed!
The control unit can now be set to automatic operation. If a production signal is
generated by the system, the lubrication circuits are activated at the set times and
then shut down sequentially.
8.5
Changing the Hopper Reservoir
If the hopper reservoir is empty, an empty report is produced by the suction lance, which
is either shown on the display, or a light is illuminated on the control unit. The system is
shut down until the hopper reservoir is changed.
WARNING
When changing the hopper reservoir the suction lance must be held in a vertical position!