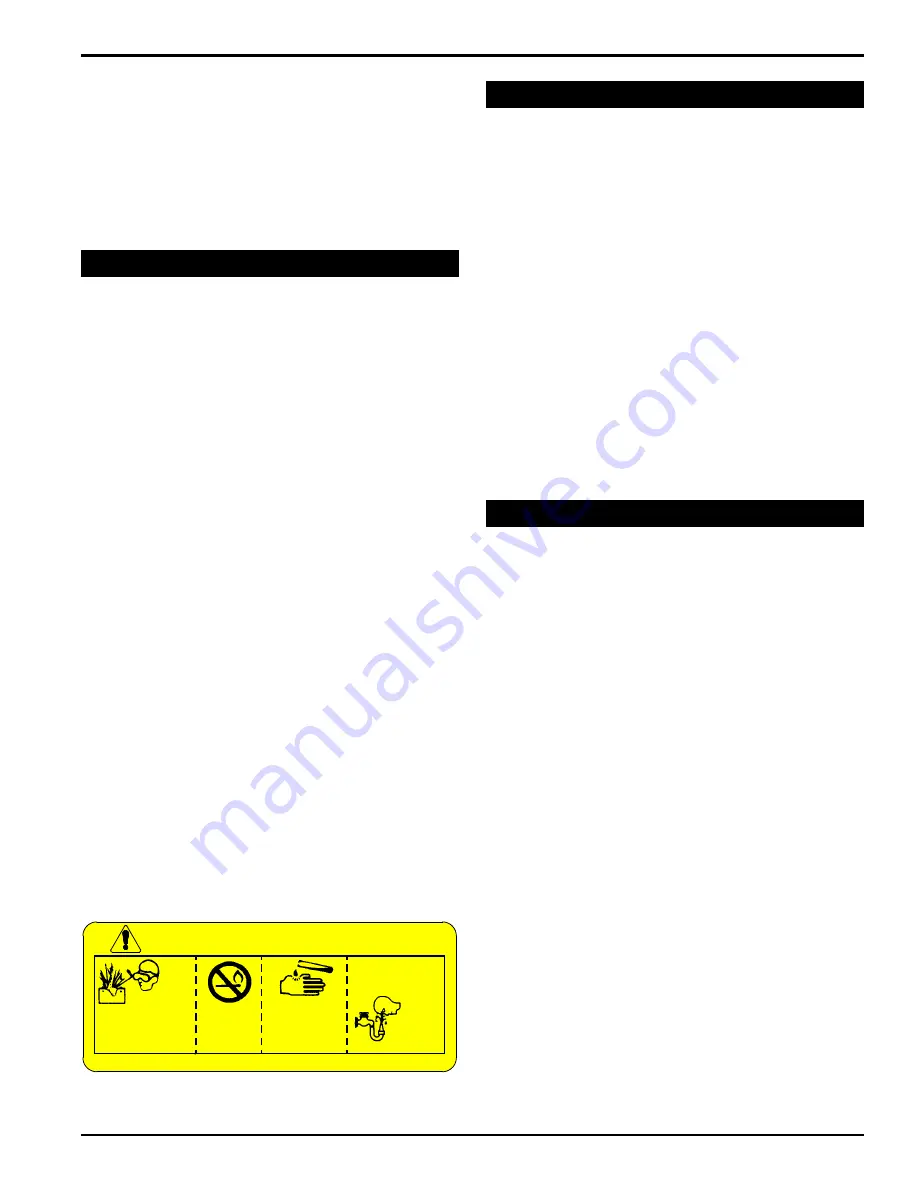
3
6 INCH CHIPPER
ENGLISH
SAFETY
Improper use and care of the battery on electric start
models can result in serious personal injury or property
damage. Always observe the following safety precautions.
●
Poison/Danger – Causes Severe Burns.
The
battery contains sulfuric acid. Avoid contact with skin,
eyes or clothing. Keep out of reach of children.
●
ANTIDOTE – External Contact:
Flush immediately
with water.
●
ANTIDOTE – Internal:
Drink a large amount of water
or milk. Follow with milk of magnesia, beaten egg or
vegetable oil. Call a physician immediately.
●
ANTIDOTE – Eye Contact:
Flush with water for 15
minutes. Get prompt medical attention.
1. The battery produces explosive gases. Keep sparks,
flame or cigarettes away. Ventilate area when
charging battery. Always wear safety goggles when
working near battery.
2. The battery contains toxic materials. Do not damage
battery case. If case is broken or damaged, avoid
contact with battery contents.
3. Neutralize acid spills with a baking soda and water
solution. Properly dispose of a damaged or worn-
out battery. Check with local authorities for proper
disposal methods.
4.
Do not short circuit battery. Severe fumes and fire can
result.
5. Before working with electrical wires or components,
disconnect battery ground (negative) cable first.
Disconnect positive cable second. Reverse this order
when reconnecting battery cables.
1. Before inspecting, servicing, storing, or changing
an accessory, shut off the machine and make sure
all moving parts have come to a complete stop.
Disconnect the battery and remove the ignition key
where applicable.
2. Replace any missing or unreadable safety decals.
Refer to the safety decal section for part numbers.
3. Allow machine to cool before storing in an enclosure.
4. Store the machine out of reach of children and where
fuel vapors will not reach an open flame or spark.
5. Never store this machine with fuel in the fuel tank
inside a building where fumes may be ignited by
an open flame or spark. Ignition sources can be hot
water and space heaters, furnaces, clothes dryers,
stoves, electric motors, etc.
6. Drain the fuel and dispose of it in a safe manner for
storage periods of three months or more.
DANGER / POISON
FLUSH EYES
IMMEDIATELY
WITH WATER
GET
MEDICAL
HELP
FAST
KEEP OUT OF THE REACH OF CHILDREN. DO NOT TIP. KEEP VENT CAPS TIGHT AND LEVEL.
SULFURIC
ACID CAN
CAUSE
BLINDNESS OR
SEVERE BURNS
NO
• SPARKS
• FLAMES
• SMOKING
SHIELD EYES
EXPLOSIVE
GASES CAN
CAUSE BLINDNESS
OR INJURY
1. Position and lock the discharge tube to face the
opposite direction of the towing vehicle prior to towing.
2. Connect hitch safety chains. Tighten trailer hitch
bolts. Do not attempt to tow the trailer if the vehicle is
not equipped with a 2" (50mm) ball.
3. Do not exceed the maximum towing speed indicated
on tire sidewall. Inflate tires to manufacturer's
specifications as stated on the tire sidewall.
4. Optimum towing performance can be achieved by
maintaining a horizontal trailer hitch.
5. Check wheel lug bolts periodically to ensure they are
tight and secure.
6.
Make sure the jack stand and the rear stabilizer
(where applicable) on the trailer are in the UP position
during towing. Place the jack stand on a level surface
and secure it in the DOWN position before using.
7. Never allow passengers to ride on the machine.
8.
If applicable, shut off fuel supply when towing.
9.
Towing laws may vary in different countries/regions/
states. It is recommended that you contact your local
motor vehicle department for any special regulations
that pertain to towing and know the laws of any
country/region/state you travel through.
5. When feeding material into the feed roller wear eye,
face and hearing protection.
6. Stand to side of feed chute when feeding material
and release material quickly.
7. When inspecting or servicing the feed roller, secure
the feed roller in the raised position using the lock pin,
if applicable.
1.6 BATTERY SAFETY
1.7 MAINTENANCE/STORAGE SAFETY
1.8 TOWING SAFETY