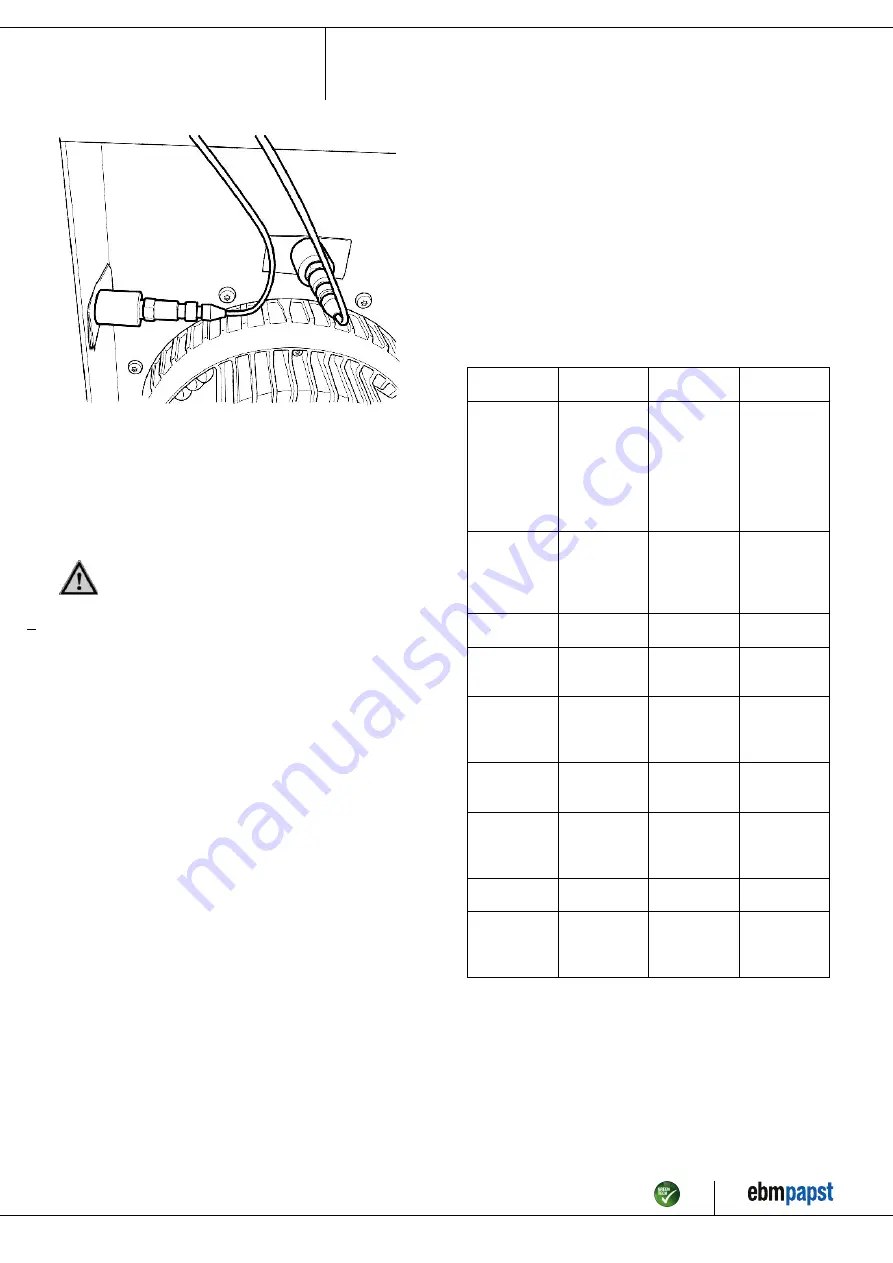
Operating instructions
K3G500-AP25-68
Translation of the original operating instructions
Fig. 4: Example showing vibration measurement. Positioning of the
sensors will vary depending on the device and the circumstances of
installation.
6.2 Cleaning
To ensure a long service life, the fans have to be regularly checked for
proper operation and degree of soiling. The frequency of the checks is to
be adapted to the occurrence of soiling.
DANGER
Risk of injury from rotating fan.
→ Only clean when not in motion. Do not disconnect the fan
from the power supply, just switch it off via the control input.
This will prevent start-up of the fan.
;
Dirt deposits on the motor housing could lead to overheating of the
motor.
;
Dirt on the impeller can cause vibration which would shorten the
service life of the fan.
;
Severe vibration could destroy the fan.
;
In such cases immediately switch off and clean the fan.
;
The preferred method of cleaning is dry cleaning, e.g. using
compressed air.
;
Use is never to be made of corrosive cleaning agents!
NOTE
Damage to the device during cleaning
Malfunction possible
→ Do not use a high-pressure cleaner to clean the device.# Do
not use any acid, alkali or solvent-based cleaning agents.
→ Do not use any pointed or sharp-edged objects for cleaning
;
Completely remove any cleaning agents used.
;
Immediately switch off and replace the device if severe corrosion is
apparent at load-bearing or rotating parts.
;
Repairs to load-bearing or rotating parts are not permissible!
;
Operate the fan for 2 hours at maximum speed to permit the
evaporation of any water which may have ingressed.
;
If cleaning does not eliminate vibration, the fan may have to be re-
balanced. In such cases please contact ebm-papst.
;
The fan is provided with maintenance-free ball bearings. The lifetime
lubrication of the ball bearings is designed for a service life of 40,000
hours.
;
Please contact ebm-papst if bearing replacement is required after this
period.
;
Adapt the maintenance intervals to the dust pollution occurring.
6.3 Safety test
NOTE
High-voltage test
The integrated EMC filter contains Y capacitors. Therefore, the
trigger current is exceeded when AC testing voltage is applied.
→ Test the device with DC voltage when you carry out the
high-voltage test required by law. The voltage to be used
corresponds to the peak value of the AC voltage required by
the standard.
What has to
be tested?
How to test?
Frequency
Which
measure?
Check the
protective
casing against
accidental
contact for
damage and to
ensure that it is
intact
Visual inspection At least every
6 months
Repair or
replacement of
the device
Check the
device for
damage to
blades and
housing
Visual inspection At least every
6 months
Replacement of
the device
Mounting the
connection lines
Visual inspection At least every
6 months
Fasten
Check the
insulation of the
wires for damage
Visual inspection At least every
6 months
Replace wires
Impeller for
wear/deposits/
corrosion and
damage
Visual inspection At least every
6 months
Clean impeller
or replace device
Tightness of
screwed cable
gland
Visual inspection At least every
6 months
Retighten,
replace if
damaged
Condensate
discharge holes
for clogging, as
necessary
Visual inspection At least every
6 months
Open bore holes
Abnormal
bearing noise
acoustic
At least every
6 months
Replace device
Vibration test
Vibration tester,
acceleration or
deceleration
measurement
Recommended
every 6 months
Clean impeller
or replace device
Item no. 54142-5-9970 · ENG · Revision 209539 · Release 2021-02-11 · Page 14 / 15
ebm-papst Mulfingen GmbH & Co. KG · Bachmühle 2 · D-74673 Mulfingen · Phone +49 (0) 7938 81-0 · Fax +49 (0) 7938 81-110 · [email protected] · www.ebmpapst.com