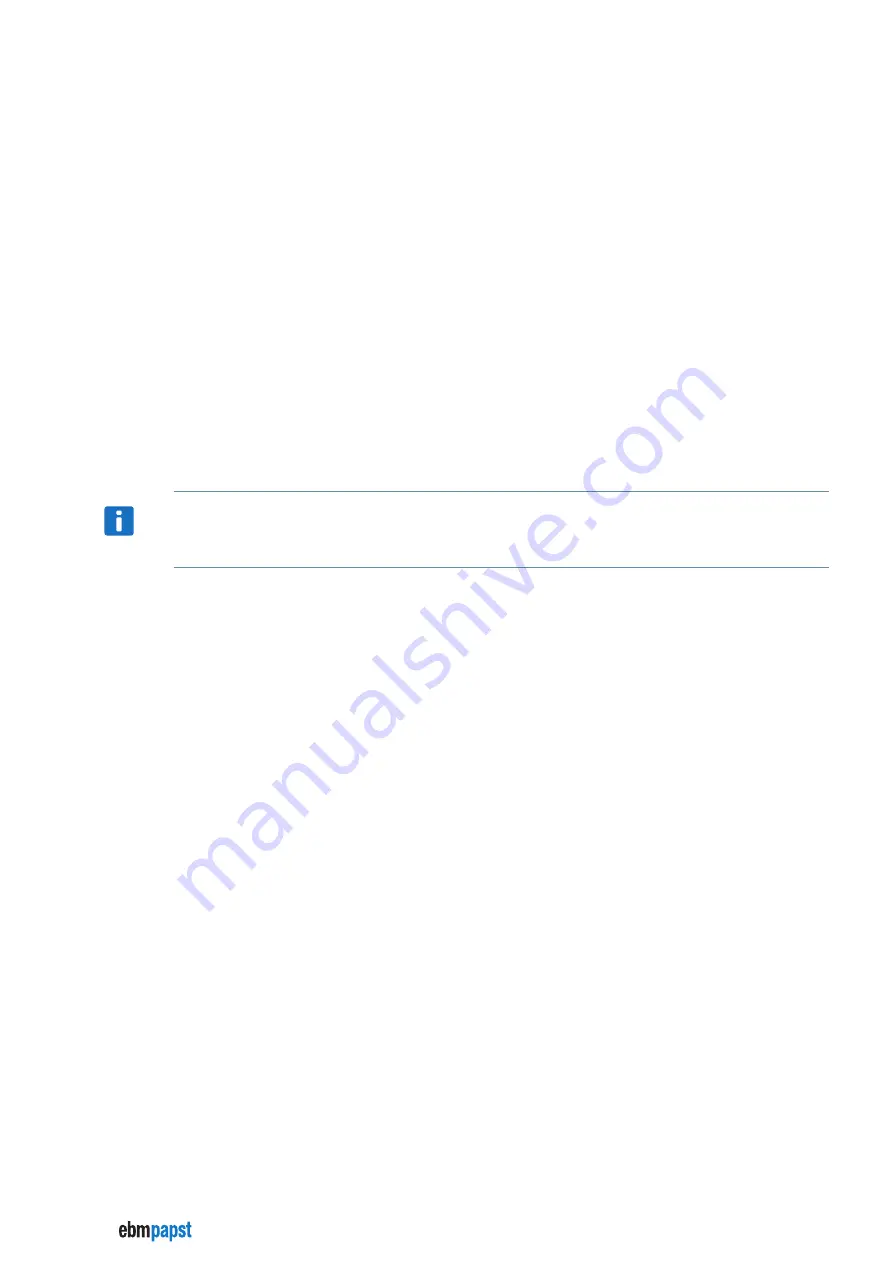
7/28
Item no.: 601.2055 · ENU · Change V1.1 · Release 2022-10-11
Drive concepts
Drive concepts
SIMATIC MICRO-DRIVE
SIMATIC MICRO-DRIVE
Safety information
2.5
Personnel qualifications
The following qualification requirements are specified in these operating instructions:
•
Authorized specialist personnel:
People who have been trained by the operator about potential hazards when carrying out
their assigned tasks and activities, in compliance with the associated documentation, in particular the safety and warning
notices contained therein. Due to their experience and training, authorized specialist personnel are able to avoid potential
risks and hazards when dealing with the drives or the application.
2.6 Safety of persons
• Provide sufficient protection against accidental contact (e.g. cover electrical contacts).
• Do not wear loose clothing or jewelery.
• Keep hair, clothing, and gloves well away from rotating components.
• Use personal protective equipment (e.g. hearing protection, thermal gloves).
2.7 Electric/electromagnetic safety
NOTICE
The drive is a built-in component that is operated in conjunction with the Siemens drive controllers (PDC
(=Profi Drive Control) or F-TM ServoDrive) and the cables defined for this by Siemens. The specifications for
electromagnetic safety can be found in the operating instructions of the Siemens drive controllers.
• Depending on the environmental conditions, regularly check the drive and connected cables for damage.
• Only use cables and plug connections approved by ebm-papst.
• Immediately replace defective cables and loose connections.
• Ensure EMC capability in the end device/installation state, e.g. with shielding.
• Provide suitable measures for avoiding impermissible electromagnetic interference emissions, such as shielding.
• Provide suitable measures against high-frequency EMC radiation
• Use control units and control devices for influencing the electromagnetic radiation.