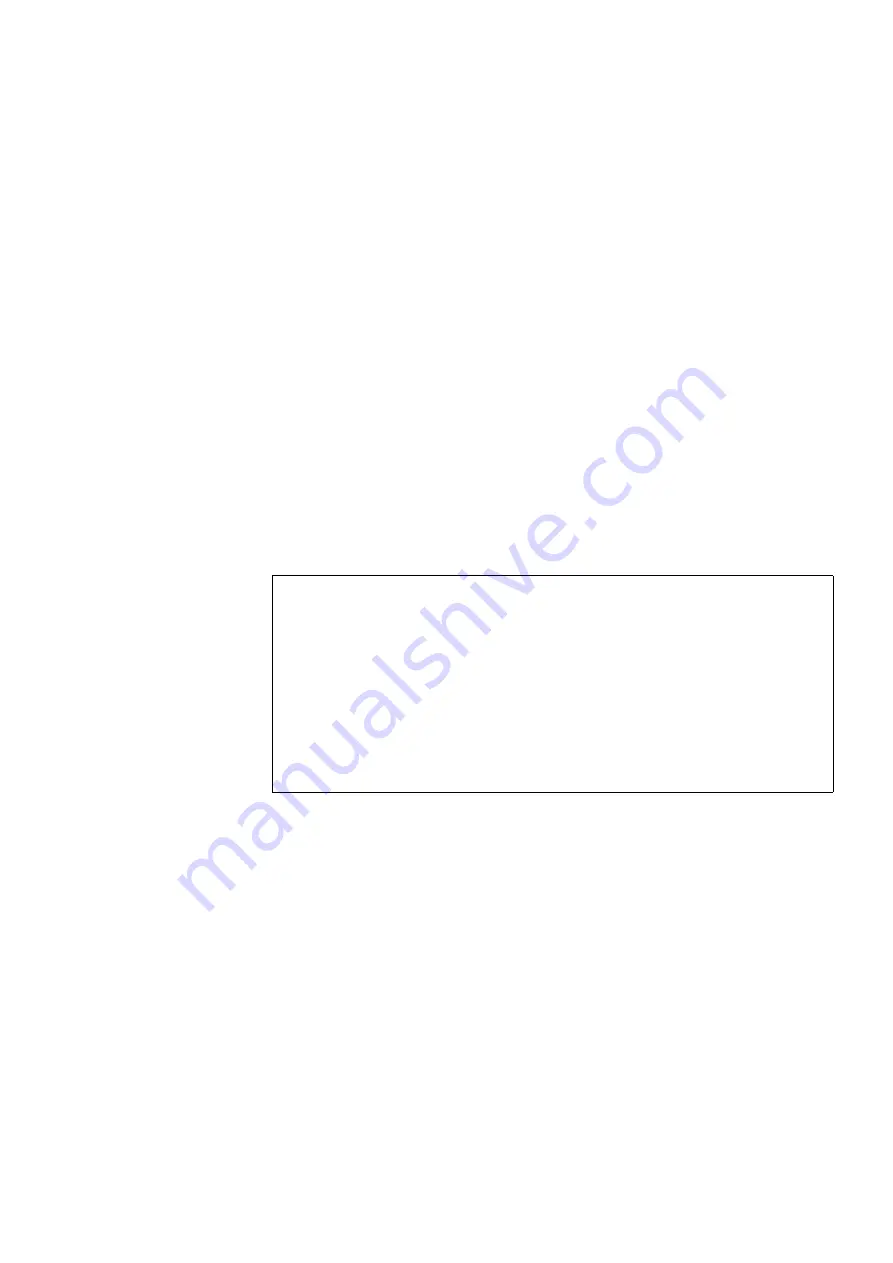
2 Engineering
2.1 Overload monitoring of motors in the Ex e area
ZB12-…, ZB32-…
11/16 MN03407004Z-DE/EN
www.eaton.com
35
2 Engineering
2.1 Overload monitoring of motors in the Ex e area
The Ex e protection of motors is achieved by means of special design
measures. The motors are assigned to temperature classes on the basis of
the highest permissible surface temperatures. The temperature rise time t
E
and the ratio between starting current and rated operational current I
A
/I
N
are
calculated also and specified on the rating plate of the motor.
The temperature rise time t
E
represents the time that expires for the
temperature of the motor winding to rise from its final rated operational
temperature up to the limit temperature, at a starting current of I
A
.
However, Ex e motors are not safe on their own. Explosion safety can only
be achieved by taking additional measures during installation and by
selecting appropriate operational conditions (PTB testing regulations), e.g.
by adding a correctly rated and set overload protection to the circuit.
2.2 Adjusting the overload current protection
DANGER
The selected current overload protection system must not only
ensure proper motor current monitoring, but also that the seized
motor is switched off within the temperature rise time t
E
.
This means that the protective device must be rated so that the
tripping time t
A
for the I
A
/I
N
ratio of the Ex e motor, that is
specified by the characteristic curve, is not greater than the
temperature rise time t
E
in order to switch off the motor safely
within this time (
→
following example).