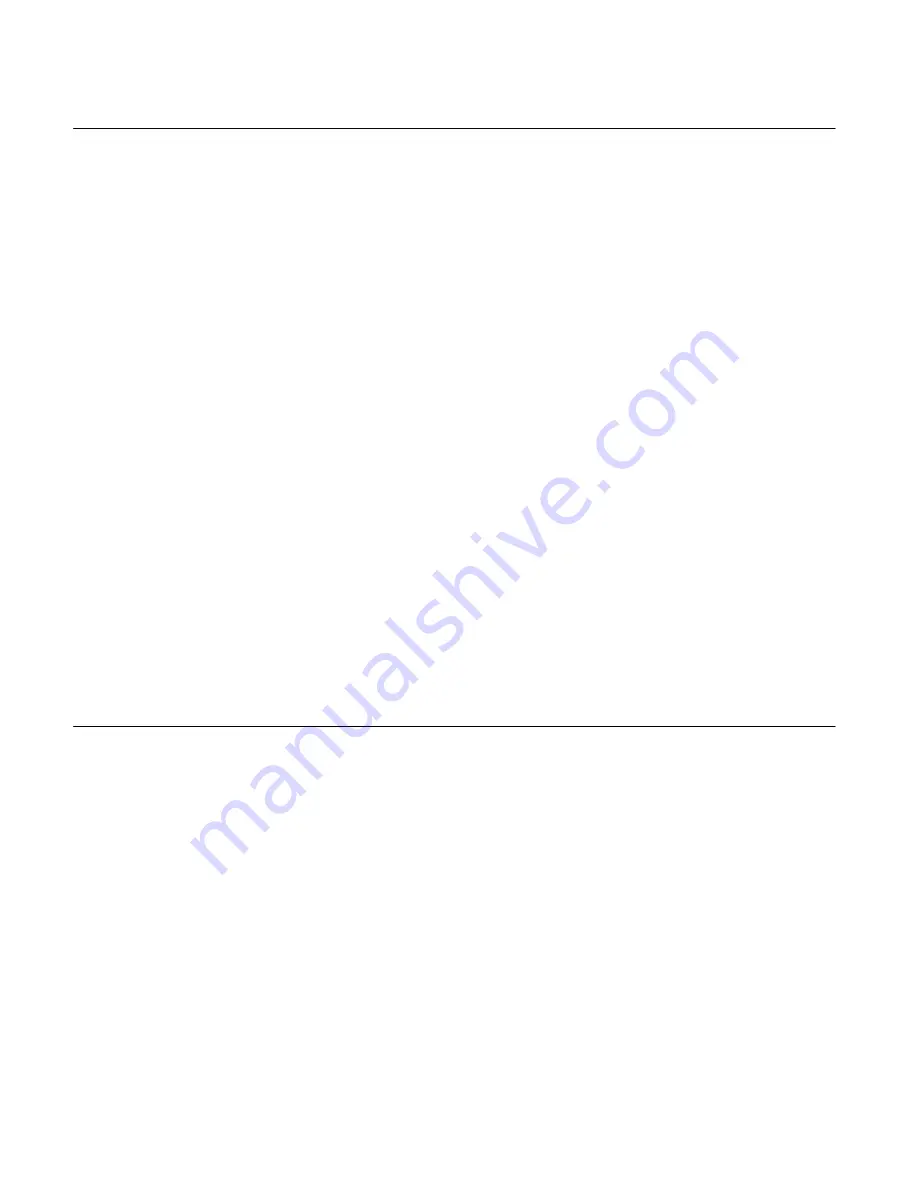
6
Section IV – Installation
A. Installation Drawings
The installation drawings listed in Table 2 will show installa-
tion dimensions, port locations and operating parameters.
Manifold, subplate and bolt kit information is also included.
NOTE
The tank line must be piped directly to tank to
minimize back pressure. The drain line from the
remotely operated valve (vent valve) must also be
directly piped to tank. Any pressure in the drain line
is additive to the pressure setting of the valve.
B. Circuit Connection
Threaded type CT/CS valves are usually connected directly
in the pressure line. Circuit flow passes through the ports
located on opposite sides of the valve body. The bottom port
(opposite the cover) is the return flow port and is connected
to tank. These valves may be teed into the pressure line by
plugging or blocking one of the pressure outlet ports.
CG type gasket mounted valves are teed into pressure lines.
The tee is connected to the pressure port of the valve sub-plate
or manifold. The return port is connected to tank. The valve
must be mounted against a flat, ported mounting surface.
Repair or replacement of CG valves is simplified in that piping
need not be disturbed.
C. Piping And Tubing
1. All pipes and tubing must be thoroughly cleaned
before installation. Recommended methods of cleaning are
sandblasting, wire brushing and pickling.
NOTE
For instructions on pickling, refer to instruction
sheet 1221 – S.
2. To minimize flow resistance and the possibility of
leakage, only as many fittings and connections as are
necessary for proper installation should be used.
3. The number of bends in tubing should be kept to
a minimum to prevent excessive turbulence and friction
of fluid flow. Tubing must not be bent too sharply. The
recommended radius for bends is three times the inside
diameter of the tube.
D. Fluids and Seals
Standard seals (Nitrile) can be used with petroleum, water
glycols, and water-oil emulsion type fluids.
F3 seals (Viton*) can be used with all commonly used indus-
trial hydraulic fluids. Viton is compatible with petroleum, wa-
ter base and synthetic fire-resistant fluids.
*Trademark of Dupont De Nemours Co., Inc.
Section V – Service and Maintenance
A. Inspection
Periodic inspection of the fluid condition and tube or piping
connections can save time-consuming breakdowns and
unnecessary parts replacement. The following should be
checked regularly.
1. All hydraulic connections must be kept tight. A loose
connection in a pressure line will permit the fluid to leak out.
If the fluid level becomes so low as to uncover the inlet pipe
opening in the reservoir, extensive damage to system
components can result. In suction or return lines, loose
connections permit air to be drawn into the system resulting
in noisy and/or erratic operation.
2. Air bubbles in the reservoir can ruin system compo-
nents. If bubbles are seen, locate the source of the air and
seal the leak.
B. Cleanliness
Clean fluid is the best insurance for long service life. There-
fore, check the reservoir periodically for dirt and other con-
taminants. If the fluid becomes contaminated, flush the entire
system and add new fluid.
To insure your hydraulic system is clean, perform the
following steps:
1. Clean (flush) the entire system to remove paint,,
metal chips, welding shot, etc.
2. Filter each oil change to prevent introduction of
contaminants.
3. Provide continuous oil filtration to remove sludge,
products of wear and corrosion generated during the life of
the system.
4. Provide protection to all areas that can introduce
airborne contaminants into the system.
5. Perform regular servicing procedures of filters,
breathers, and reservoirs.