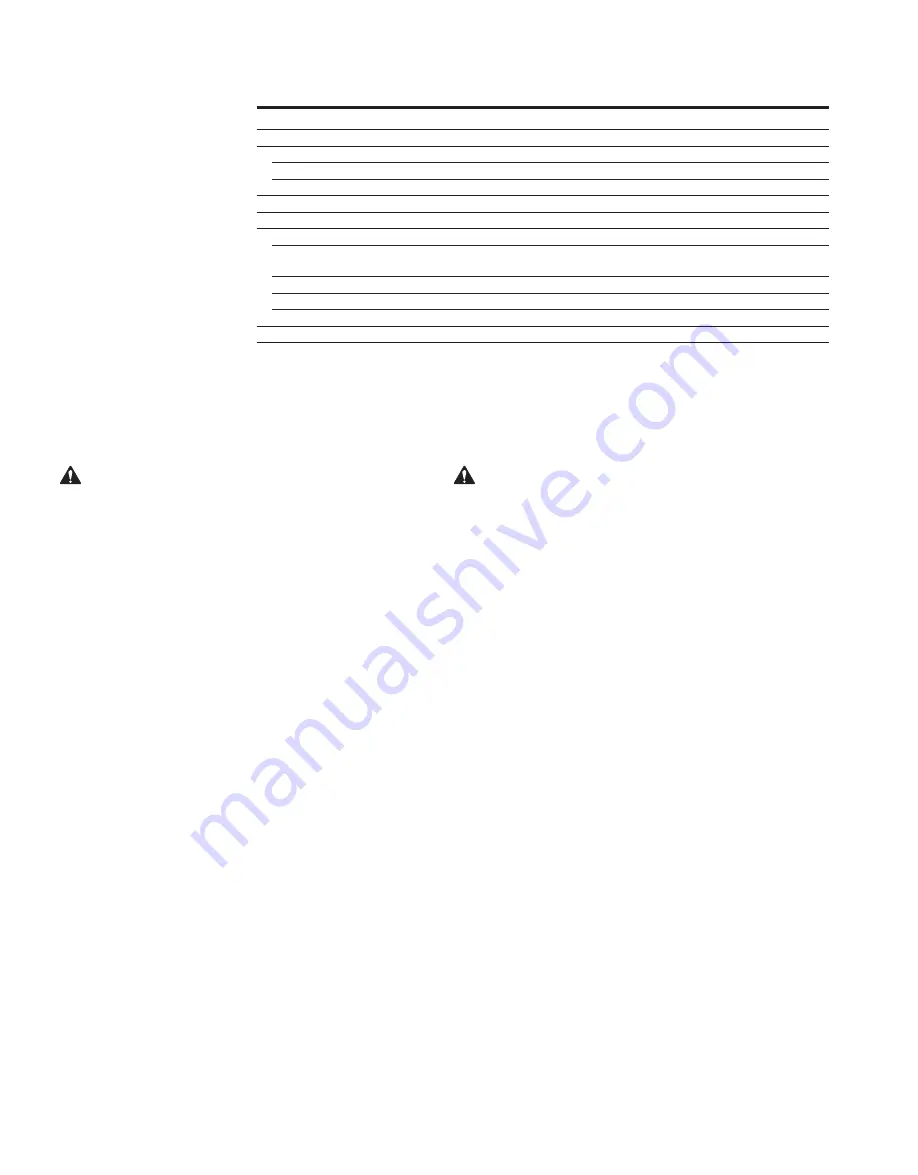
2
EATON
ET4001 Crimp machine operator´s manual W-EQCR-TM022-E3 March 2019
Table of contents
1. PREVENT
UNAUTHORIZED
OPERATION. Do not
permit anyone to operate
this equipment unless
they have read and
thoroughly understood
this manual.
2. WEAR SAFETY GLASSES.
3. AVOID PINCH POINTS.
Do not rest your hand
on the crimp ring. Keep
your hands clear of all
moving parts. Do not
allow anyone, other than
the operator, close to the
equipment while it is in
operation.
4. MAINTAIN DIES WITH
CARE. Dies used in
the ET4001 crimp
machine are hardened
steel, offering the best
combination of strength
and wear resistance for
long life. Hardened dies
are generally brittle and
care should be taken to
avoid any sharp impact.
Never strike a die with a
hardened instrument.
5. USE ONLY SPECIFIED
EATON PRODUCTS.
Make hose assemblies
using only Eaton's
hose and Eaton fittings
specified for this
assembly equipment.
6. VERIFY CORRECT
CRIMP DIAMETERS.
Check and verify correct
crimp diameters of all
fittings after crimping.
Do not put any hose
assemblies into service
if the crimp diameters
do not meet Eaton crimp
specifications.
7. MAKE SURE ALL DIES
ARE COMPLETELY IN
PLACE, the spacer ring
rests against the locator
bracket, and the pusher
halves are closed before
crimping.
8. DO NOT OVER
PRESSURIZE. Do not
exceed the 5,000 psi
hydraulic pressure
supplied to the machine
9. DIE CHANGE. DO NOT
INSERT/REMOVE DIES
WHILE THE POWER IS
ON OR MACHINE IS IN
OPERATION.
10. SECURE THE
EQUIPMENT TO
A STABLE WORK
SURFACE. Prior to
operation, secure the
crimp machine to a
stable work surface to
prevent the equipment
from tipping. See
pages 4-5 for mounting
instructions.
11. UNPLUG THE POWER
SUPPLY WHEN NOT IN
USE.
12. KEEP WORK AREA
CLEAN. Cluttered areas
and benches invite
accidents.
13. DO NOT OPERATE
WITHOUT THE BASE
ADAPTER RING IN
PLACE.
Safety instructions
ET4001 Crimp machine
WARNING
Eaton's hose and Eaton hose fittings should only be assembled
using Eaton approved assembly equipment. Do not use any
combinations of Eaton's hose, Eaton hose fittings, or Eaton
assembly equipment with hose, hose fittings, or assembly
equipment supplied by another manufacturer.
Eaton hereby disclaims any obligation or liability (including
incidental and consequential damages) arising from breach of
contract, warranty, or tort (under negligence or strict liability
theories) should Eaton hose, Eaton hose fittings, or Eaton
assembly equipment be used with any hose, hose fittings, or
assembly equipment supplied by another manufacturer, or in the
event that product instructions for each specified hose assembly
are not followed. (Reference SAE J1273 – Recommended practice
for hydraulic hose assemblies).
WARNING
Failure to follow Eaton processes and product instructions and
limitations could lead to premature hose assembly failures,
resulting in property damage, serious injury, or death.
Eaton fitting tolerances are engineering to match Eaton's hose
tolerances. The combination or use of Eaton's hose and hose
fittings supplier by another manufacturer may result in the
production of unreliable and/or unsafe hose assemblies and is
neither recommended nor authorized by Eaton.
Read and understand the operator’s manual before
attempting to operate any equipment.
Section
Page
Safety instructions
2
Specifications and equipment
3
ET4001 Crimp machine
3
ET4001P-002 Electric pump
3
Shop/Work Table Mounting Instructions
4 - 5
Check-out procedure
5
Operating instructions
6 - 9
ET4000AR-001: Using ET4000AR-001 Base adapter rings
6
ET4000AR-002: Using ET4000AR-002 Base adapter rings for heavy 4-wire
7
and 6-wire fittings (-20 thru -32 collets)
T-410-25 Adapter ring
8
Spacer ring and nominal crimp diameter measurement
9
Troubleshooting procedures
11
Repair and replacement items
11