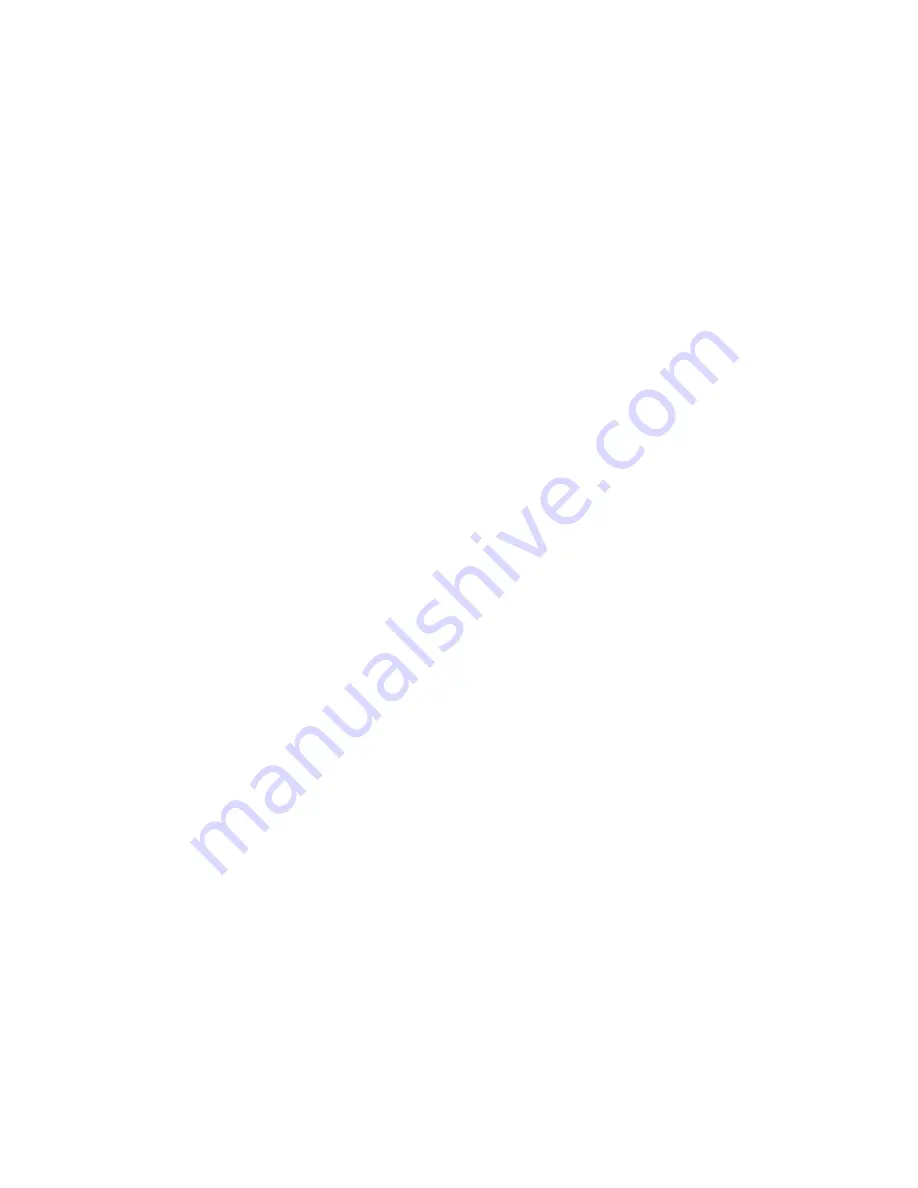
Tap position indication (TPI)
The control has the ability to track the position of the tap-
changer. The TPI function senses the status of the motor
and neutral light circuits and does not require source (input)
voltage. The present tap position is stored at FC 12.
EXAMPLES: “8” at FC 12 indicates 8 raise and “-7”
indicates 7 lower.
The TPI function is synchronized to the position of the tap-
changer by running the regulator to the neutral position.
To manually set the present tap position: Access Admin
security level; access FC 12; use the
EDIT
key to change to
the desired value.
The maximum tap position since last reset (upper drag-hand
value of the present tap position) and its date and time are
stored at FC 27. The minimum tap position since last reset
(lower drag hand value of the present tap position) and its
date and time are stored at FC 28.
The TPI drag hand values and dates/times are reset to the
present values by the master reset, FC 38, or by resetting
each of the values individually. The drag hand reset switch
resets the drag hands of the position indicator only, not TPI.
All TPI values are stored in non-volatile memory.
The following conditions could occur if the present tap
position was manually set incorrectly:
●
●
The present tap position value will go to invalid “---” if
the present tap position is 0 (zero, neutral) but no neutral
signal is detected. For example, this condition will occur
if a replacement control with present tap position set to
“0” is installed on a regulator which is not in the neutral
position.
●
●
If the TPI function detects a successful upward tap
and the prior value of FC 12 was “16”, or a successful
downward tap is detected and the prior value of FC 12
was “–16,” the prior value will be maintained.
The display will show a diagnostic error message upon
power-up when: (1) the present tap position value prior to
power-up is “---” (invalid) and the regulator is not in neutral
position; (2) The present tap position prior to power-up is
“0” and the regulator is not in the neutral position. [This
condition will cause the present tap position value to go to
invalid (“----”)]; and (3) During automatic or manual operation
the present tap position changes to “0”, but a neutral signal
is not received. The
No Neutral Sync
signal is an attention
signal, not a failure signal.
The TPI will satisfy the diagnostics routine upon power-
up when: (1) The regulator is in neutral and the present
tap position is “0”; (2) The present tap position is not “0”
and the regulator is not in neutral, including when the tap
position is not set correctly; and (3) When the regulator is in
neutral and the present tap position is not “0” (TPI will self-
correct and reset the tap position).
Source-side voltage
Without a source voltage input, some functions will indicate
dashes when displayed. There are three methods for
supplying a source-side voltage to the CL-7 control: Internal
Differential Potential Transformer (IDPT), source-side PT, or
source-side voltage calculation.
Differential voltage
The voltage regulator may be designed and ordered with
an Internal Differential PT (IDPT). The IDPT will be included
in the schematic on the voltage regulator nameplate and
labeled Series Winding Potential Transformer. An IDPT
supplies the voltage difference between the source and
load bushings of the voltage regulator. This differential
voltage is then combined with the load voltage to provide
the source-side voltage. When using an IDPT on an Eaton's
Cooper Power series voltage regulator, the source voltage
accuracy is within ± 1%.
As a standard, a second ratio correction transformer (RCT2)
is not supplied on regulators equipped with an IDPT. The
control will use the internal PT ratio entered at FC 44
and
the input voltage from the IDPT to determine the differential
voltage between the source and the load bushings. The
setting at FC 146 must be set to Vdiff without RCT2 for this
configuration.
If an RCT2 is supplied, the Overall PT Ratio entered at
FC 44 and the input voltage from the IDPT are used to
determine the differential voltage. The setting at FC 146
must be set to Vdiff with RCT2 for this configuration.
Source voltage
A source-side PT may be used to supply a directly
measured source voltage. When using a source-side PT, the
user must change Vin PT Configuration, FC 146, from the
default Vdiff without RCT2 to Vin Mode. Some manufactures
use a source PT as a standard. Using an external source-
side PT may be desirable if the voltage regulators are in
a closed-delta configuration. In a closed delta, the source
voltage and percent regulation will only reflect the true
system source values if an external source voltage or
DeltaCalc feature is used. Voltage regulator performance
is not affected by the difference between metering
parameters when using an external source PT: the accuracy
of the source voltage is dependent upon the accuracy of
the PT. When FC 146 is set to Vin, the control will use the
Internal P.T. Ratio (FC 44
) to determine the measured
source bushing voltage.
Source-side voltage calculation
The CL-7 control has the ability to calculate the source-side
voltage without an IDPT or source PT. When this feature
is turned on at FC 39, the control will use the load voltage
from the main PT, the regulator type (Type A, Type B, Type
C or Type D), the tap position, and the internal impedance
of the regulator to calculate the source-side voltage. This
calculated source voltage is accurate to within ±1.5%. Only
the regulator type needs to be programmed into the control;
124
INSTALLATION, OPERATION, AND MAINTENANCE INSTRUCTIONS
MN225003EN April 2018
CL-7 Voltage Regulator Control