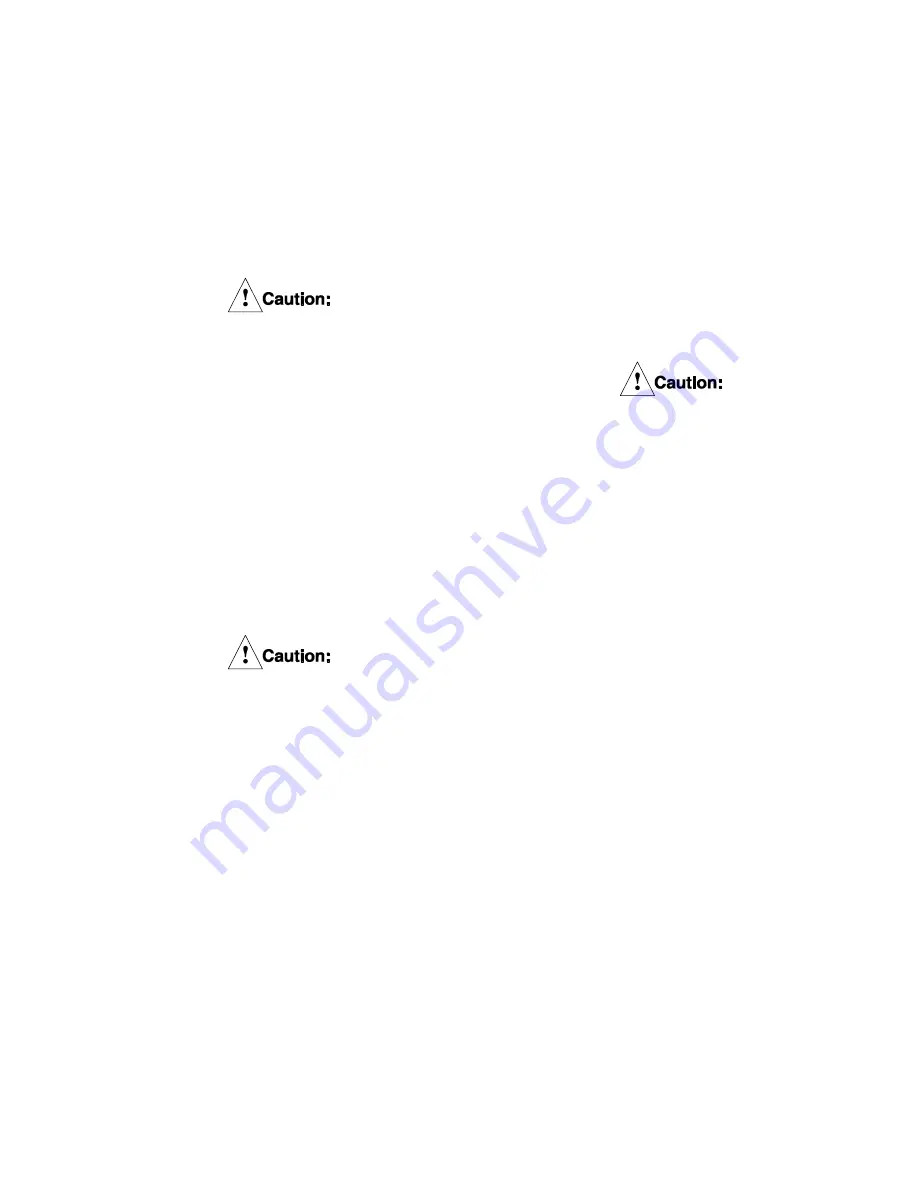
3.2
Air Connection
The rotorseal shaft (7) has a pipe thread for
the inlet air connection. The connection to the
rotorseal must always be through a flexible
hose, and the air supply piping must be self-
supporting. Orientation of the hose in a hori-
zontal position may help in reducing bearing
loading. A good pipe thread sealant must be
used when connecting the flexible hose to the
rotorseal.
Rigid air connection will preload
the rotorseal bearings, resulting in
premature failure.
4.0
MAINTENANCE
A replacement kit is available to allow the
rebuilding of the type RH rotorseal (refer to
the table under Figure 1). Airflex rotorseals
are manufactured with quality materials to
precision tolerances. These instructions
should be followed carefully to assure a prop-
erly repaired rotorseal. Only Airflex rotorseal
parts should be used. The rotorseal must
be removed from its mounting, and repairs
should only be made in a clean, dust-free
environment.
When replacing components, use
only Genuine Airflex replacement
parts. Use of other materials may
severely effect performance.
4.1
Disassembly
4.1.1
The cover (10) is retained in the housing (1)
by both staking and the use of Loctite®. Use a
flat blade tool to carefully un-stake the cover.
It may be necessary to heat the housing
slightly to soften the Loctite®. Use
a spanner wrench to remove the cover.
Note: The cover on some RH rotorseals
is secured with a setscrew and Loctite®.
Remove the setscrew prior to attempting
to remove the cover.
4.1.2
Remove the shaft (7), bearings (8) and bearing
spacer (9) from the housing (1) by holding the
knurled portion of the shaft in a vise while striking
the housing gently with a soft-faced mallet.
Note: Some units do not have a knurled area. In
this case, a pipe union can be temporarily
attached to the threaded portion of the shaft to
aid in holding the shaft while preventing damage
to the shaft. Rotate the housing while striking to
reduce binding of the bearings in the housing.
4.1.3
Remove the carbon seal (5), rubber seal ring
(4), spring retainer washer (3) and spring (2)
from the housing. If these parts do not fall
freely from the housing, they may be removed
with the aid of a wire hook.
4.2
Cleaning and Inspection
4.2.1
After disassembly, clean all parts thoroughly
using a grease-cutting solvent.
Follow proper safety precautions
when using solvents.
4.2.2
Inspect and check the ball bearings (8). They
should be free of rust and contamination,
revolve smoothly without binding and show
no signs of excessive looseness or wear.
Bearings with damaged or leaking seals
should be replaced.
4.2.3
Inspect the lapped sealing end of the shaft (7)
for scoring or pitting. Scoring or pitting will re-
sult in leakage. If the disassembly resulted in
burrs on the shaft where it was held, remove
the burrs.
4.2.4
If inspection indicates the shaft or bearings
are in poor condition, the shaft, bearings and
bearing spacer (9) must be replaced.
4.2.5
Inspect the housing and cover for damage.
Replace if necessary.
4.3
Assembly
4.3.1
Assemble spring (2), spring retainer washer
(3), rubber seal (4) and carbon seal as shown
in Figure 1. The rubber seal should firmly seat
on the chamfered surface of the carbon seal.
4.3.2
If the bearings and shaft are replaced,
assemble the bearings and bearing spacer
to the shaft using proper bearing assembly
procedures.
RS 9030
3
© Copyright Eaton Corp., 2002. All rights reserved.
(Revised: December 2002)