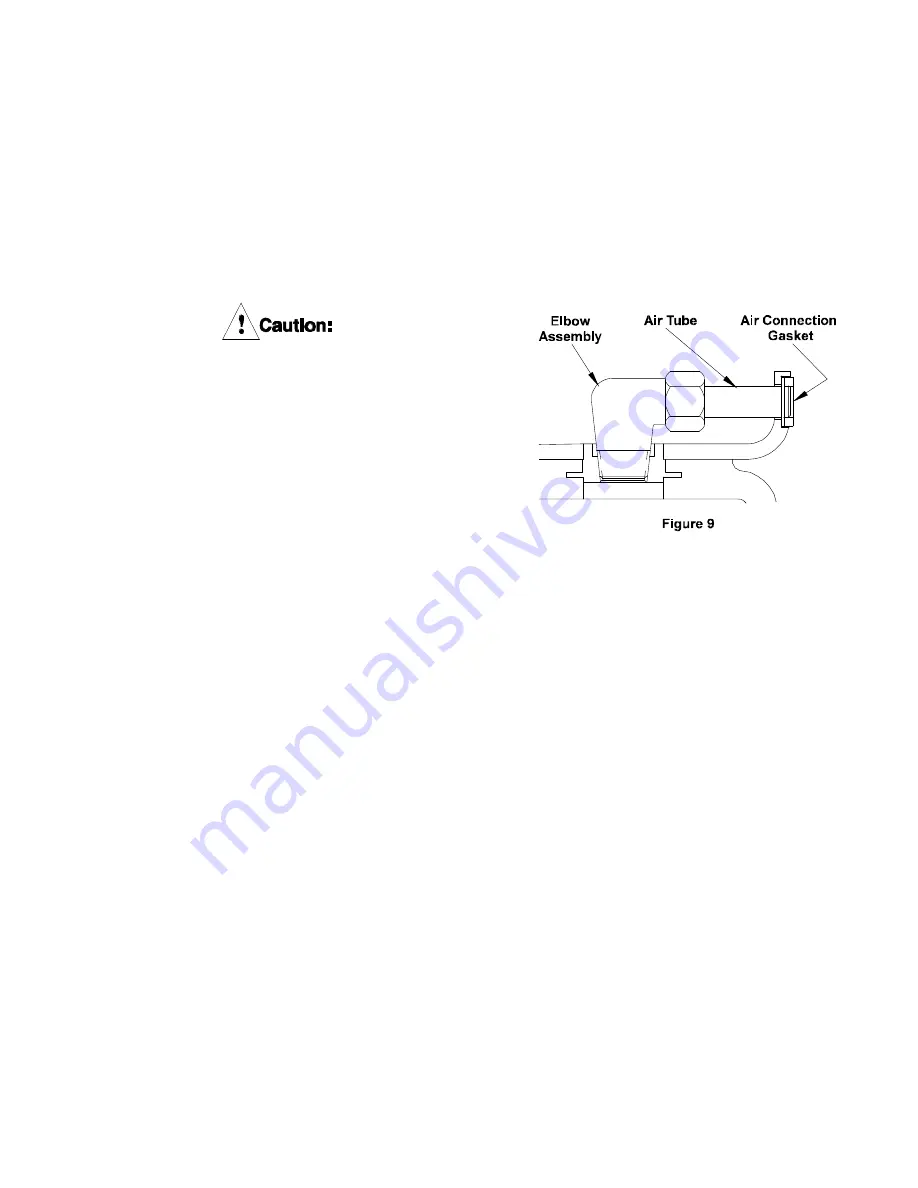
2.4.2.
Fabricate a rigid bracket for supporting a dial
indicator and attach to the spider. See
Figure 8.
2.4.3
Thoroughly clean the flange O.D. and the face
of the drum hub where alignment readings are
to be taken.
2.4.4
Rotate the spider and take parallel alignment
readings off the drum hub flange O.D. If both
shafts can be rotated together, the alignmnet
readings are less influenced by any surface
irregularities.
When recording parallel alignment
readings, “Sag” of the indicator/indi-
cator bracket must be accounted for.
2.4.5
Angular alignment readings can be made by
accurately measuring the gap between the
spider and drum hub faces with an inside mi-
crometer. If a dual indicator is used, make
sure to monitor and correct for any axial
movement of the shaft. To reduce the influ-
ence any surface irregularities may have on
the angular alignment readings, index the spi-
der 90 degrees after taking the initial set of
readings. Take an additional set of readings
and index the spider another 90 degrees.
Continue in this manner until four sets of read-
ings have been taken. For misalignment cor-
rection, use the average of the four readings,
the four bottom readings, and each of the four
side readings.
2.4.6
Shim and shift the base of the movable shaft
to correct the misalignment. After tightening
the base, recheck the alignment and correct.
If necessary. Make sure to check for a “soft
foot” condition. Dowel or chock into position
after satisfactory alignment has been
achieved.
Note: On many applications, thermal growth
of the driving or driven machinery may result
in unacceptable shaft alignment in a running
condition. It is always good practice to make
a “hot alignment” check and re-shim if neces-
sary.
2.5
Installation of Element and Drum
(Single and Dual)
2.5.1
Note the orientation of the drum flange with
respect to the air connection(s) on the ele-
ment and slide the drum into the element.
2.5.2
Separate the shafts as far as the bearing
clearances will allow and hoist the ele-
ment/drum into position.
2.5.3
Attach the drum to the drum hub with the ap-
propriate fasteners. See Table 1. Make sure
the bore in the drum flange fully engages the
pilot on the drum hub.
2.5.4
Apply a small amount of gasket cement to the
air connection gaskets to hold them in position
during installation. Install the air connection
gaskets onto the air tubes. See Figure 9.
2.5.5
Align the element air connections with the pas-
sages in the spider and attach the element to
the spider with the appropriate fasteners. See
Table 1. Make sure the element fully engages
the register in the spider.
2.6
Air Control System
2.6.1
A typical air control system is shown in Figure
10. Since the air control system used will be
dependent on the specific application, a de-
tailed description cannot be made in this man-
ual. Following are some general guidelines for
installing and adjusting air controls.
2.6.1.1 The air receiver tank must be located as close
to the rotorseal as possible (within five feet)
for consistent clutch or brake response.
2.6.1.2 Use full size piping and valves consistent with
the rotorseal size.
2.6.1.3 Keep the number of elbows to a minimum.
2.6.1.4 Use poppet-type solenoid valves. Spool
valves are not recommended.
2.6.1.5 An air line lubricator is not required for the ele-
ment; however, if one is used, it must be a
non-adjustable, mist-type.
PDF Format
7
© Copyright Eaton Corp., 2001. All rights reserved.
StockCheck.com
Downloaded from StockCheck.com