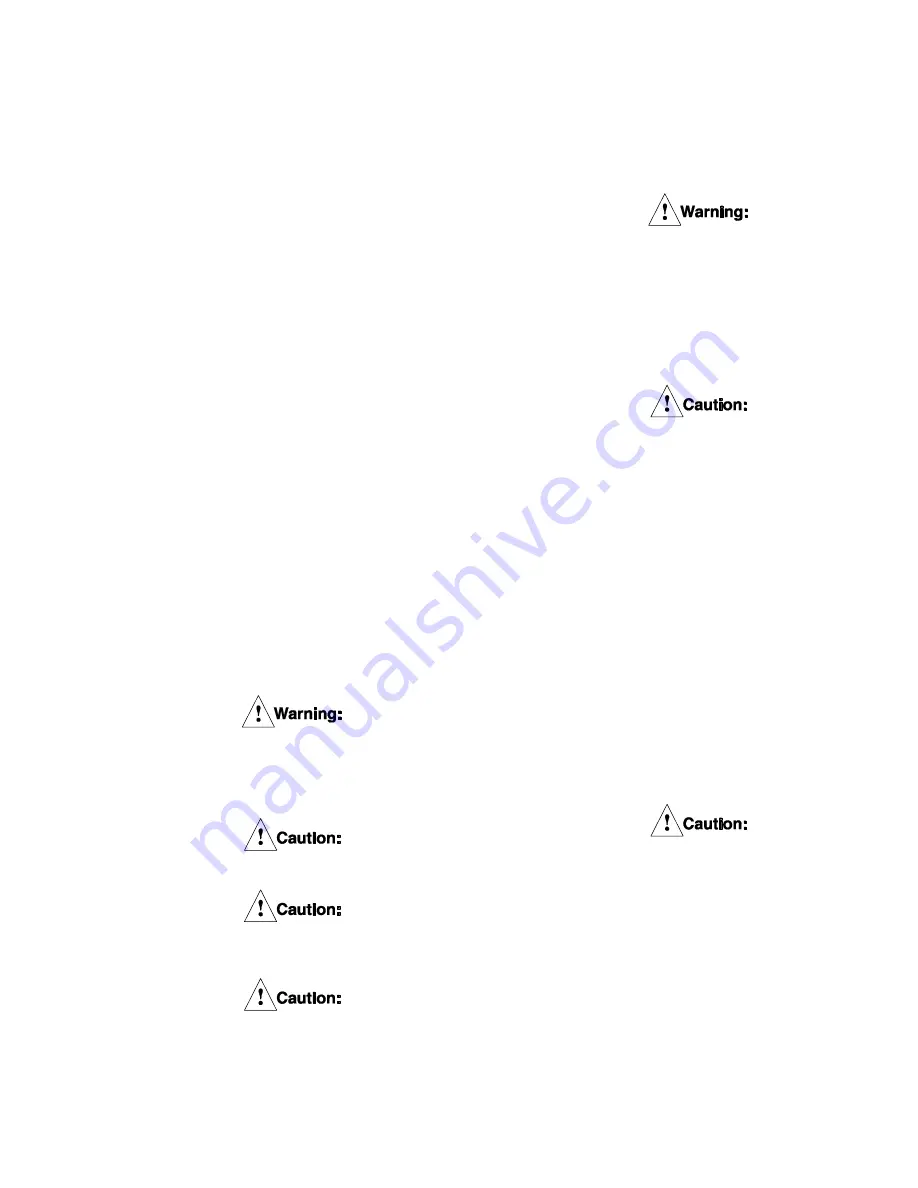
4.5.3
Remove the old screws and and discard the
old friction material.
Note: Use of a pinpoint torch to heat the
screws and soften the Loctite
®
will ease
removal of the screws.
4.5.4
Clean all burrs, corrosion etc. from the friction
disc core or mounting surface.
4.5.5
Position the friction material to align the
screw holes. Install several screws loosely at
several of the outermost screw hole locations to
properly align the friction discs or blocks.
For friction discs (sizes 18 and 24), install the
remaining screws in an even, crosswise pattern
per the procedure in the next paragraph. When
installing screws in friction blocks (sizes 36 and
48), install and tighten the screws from the
centermost position in the block, then progress
towards the outer edges of the block.
Following the above pattern, install one screw at
a time by applying Loctite
®
#262 to the screw
threads (use Loctite
®
#242 for size 18) and
tightening the screw to the proper torque value.
Tighten screws to 15 ft.-lb. (75 in-lb. for size 18).
Install and torque each remaining screw immedi-
ately after application of Loctite
®
, then proceed to
the next screw. Be sure to remove, apply
Loctite
®
and properly tighten the initial screws
used for alignment of the friction disc or block.
Note the relevant safety precautions in the
following column when assembling screws.
Loctite
®
may cure prior to properly
tightening the screw if not tightened
to the proper torque value immediately
after installation.
Use only Airflex-supplied screws.
Loctite
®
#262 must be shaken prior to
application.
Loctite
®
#262 may irritate sensitive
skin. Refer to the product label for
proper safety precautions.
4.5.6
Tensioner friction disc assemblies (7) of size 36"
and larger require that the friction material be
machined flat after assembly, to allow for even
contact and minimize wear-in. Machine the
friction surface perpendicular to the bore splines
within .003", and parallel to the opposite face
within .010".
Use appropriate safety equipment
and dust collection systems when
machining friction material.
4.5.7
After replacement of friction material,
re-assemble the tensioner per Section 4.9.
During start-up, observe wear-in and operation
precautions per Section 3.0, Operation.
After replacement of friction material, a
minimum wear-in period of four hours
at 50% of the rated horsepower is
recommended for the friction couple
to achieve rated torque.
4.6
Wear Plate Replacement
Note: When replacing wear surfaces, it is
recommended that the mating friction material
be replaced or machined flat to ensure good
contact between the mating surfaces. See
Table 14 for wear limits.
4.6.1
Disassemble the tensioner per Section 4.3.
4.6.2
Remove the screws and locknuts holding the
wear plates and remove the wear plates. If the
wear plates cannot be easily lifted off, gently tap
the O.D. to break the gasket seal.
Do not attempt to break the gasket
seal by prying between the wear plate
and housing. Damage to the sealing
surfaces may occur.
4.6.3
Inspect the water passages and, if necessary,
use a wire brush to clean them. If re-painting is
necessary, sand blast the water passages and
paint the surfaces with PLASITE
®
Epoxy #9052
Polymine coating. Dry film thickness should be
8 to 12 mils (0,2 to 0,3 mm). Be careful not to
allow the paint to get into the seal grooves or
onto the face of the support nubs.
WCB 11070 VP 4.2 Format
20
© Copyright Eaton Corp., 2003. All rights reserved
April 2002 (Revised June 2003)