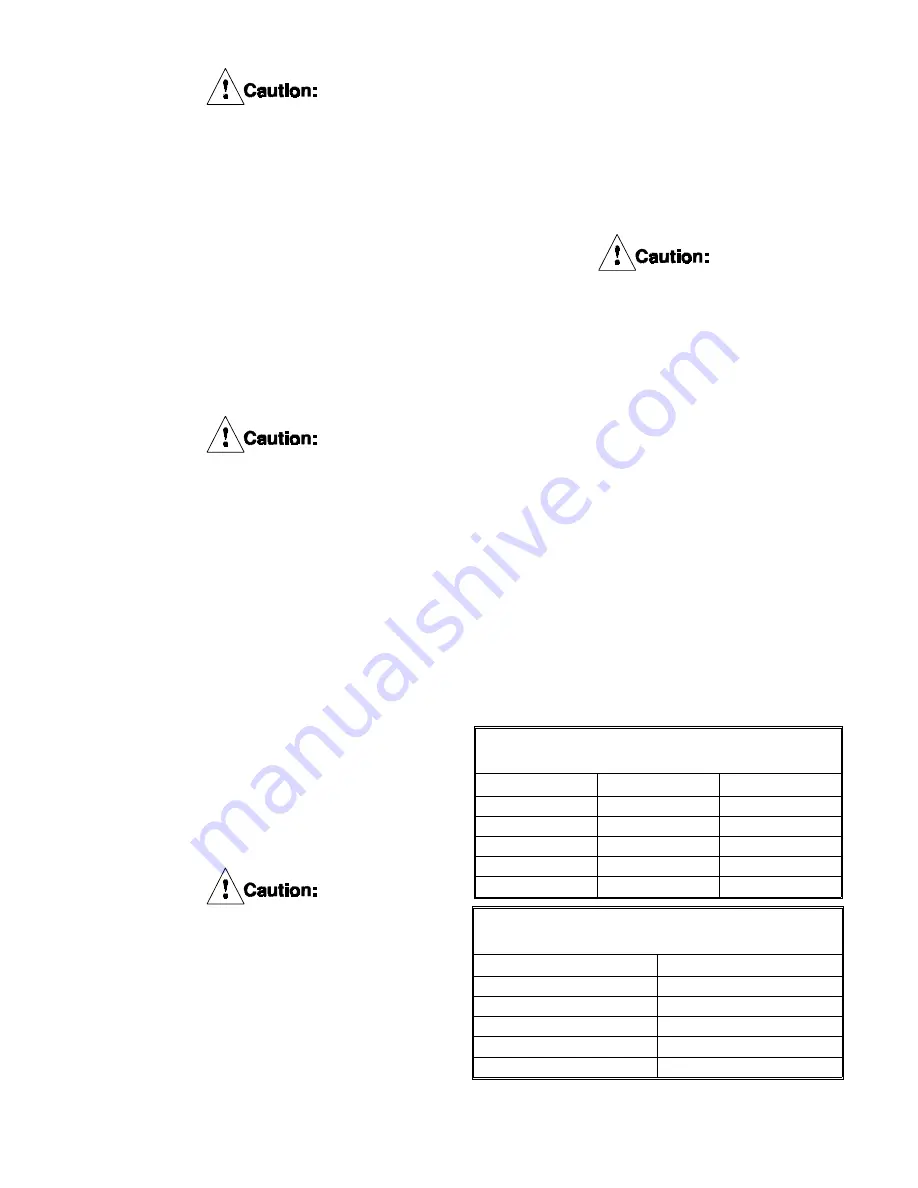
Manual setting of the rivets using a
punch very frequently results in splitting
of the clinched end of the rivet. When
this occurs, the rivet will ultimately fail in
service due to fatigue. It is therefore
recommended that rivets be set using an
automatic rivet setting machine if
possible.
6.3.5
Insert a rivet through any hole and set using a
w asher on the clinched end of the rivet. Figure
21 illustrates machine setting and Figure 22 il-
lustrates setting the rivet manually. When
setting manually, use an arbor press and keep
the setting tool square to avoid splitting the
rivet.
The clinched end of the rivet must have a
washer in place prior to clinching. Failure
to use the washer or use of excessive
force when clinching the rivet will
fracture the friction lining.
6.3.6
The remaining rivets may be installed
in any reasonable sequence follow ing
a crossw ise pattern.
6.4
Wear Plate Replacement
Note: Item numbers (# ) are show n on
Figures 1, 3, 4, 5 ,6 and 7.
6.4.1
Refer to Section 11.0 for the appropriate w ear
plate replacement kit part number.
6.4.2
Remove the screw s and locknuts holding the
w ear plates and remove the w ear plates. If the
w ear plates cannot be easily lifted off, gently
tap the O.D. to break the gasket seal.
Do not attempt to break the gasket seal
by prying between the wear plate and
housing. Damage to the sealing surfaces
may occur.
6.4.3
Inspect the w ater passages and, if necessary,
use a w ire brush to clean them. If repainting is
necessary, sand blast the w ater passages and
paint the surfaces w ith Glid Gard
®
Epoxy
5256/5257 or equivalent. Dry film thickness
should be 0.007" (0.18 mm). Be careful not to
allow the paint to get into the seal grooves or
onto the nubs.
If nubs are severely corroded, wear
plates may not be properly supported.
Replace pressure plate, reaction plate or
mounting flange, if necessary.
6.4.4
Clean and completely dry the gasket surfaces
on the pressure plate (14), reaction plate(s)
(31) and mounting flange (2). These surfaces
should be free of nicks and scratches to
prevent leaks. Nicks and scratches may be
filled w ith Loctite Superflex
®
#596 Silicon
Sealant.
6.4.5
Apply a uniform bead of Loctite Superflex
®
#596 Silicon Sealant in the grooves of the
pressure plate, reaction plate(s) and mounting
flange. Recommended bead diameter is
0.060" - 0.090" (1.5 mm - 2.3 mm).
6.4.6
Inspect the new w ear plates and remove any
scratches or raised edges w ith very fine sand-
paper or steel w ool. Position the smoothest
side of the w ear plate on the mating surface
being careful to align the holes.
TABLE 12
Wear Plate Fastener Torque-ft-lb (Nm) Lubed
Model
Size
Torque
8WCB
#10-24NC
5 (7)
14WCB
1/4-20NC2
12 (16)
18WCB
5/16-18NC
21 (28)
24WCB
5/16-18NC
21 (28)
36WCB
3/8-16NC2
40 (54)
TABLE 13
Inlet and outlet port sizes
Model
Size
8WCB
1/2-14NPT
14WCB
1/2-14NPT
18WCB
1/2-14NPT
24WCB
3/4-14NPT
36WCB
1 1/4-11NPT
PDF FORMAT
27
© Copyright Eaton Corp., 1995. All rights reserved.
Содержание 146246A
Страница 5: ...18 24 36 WCB Single Disc Figure 4 PDF FORMAT 4 Copyright Eaton Corp 1995 All rights reserved ...
Страница 6: ...18 24 36 WCB Dual Disc Figure 5 PDF FORMAT 5 Copyright Eaton Corp 1995 All rights reserved ...
Страница 7: ...18 24 36 WCB Triple Disc Figure 6 PDF FORMAT 6 Copyright Eaton Corp 1995 All rights reserved ...
Страница 8: ...Figure 7 18 24 36 WCB Quad Disc PDF FORMAT 7 Copyright Eaton Corp 1995 All rights reserved ...
Страница 20: ...Figure 14 Figure 15 Figure 13 Figure 16 PDFFORMAT 19 Copyright Eaton Corp 1995 All rights reserved ...