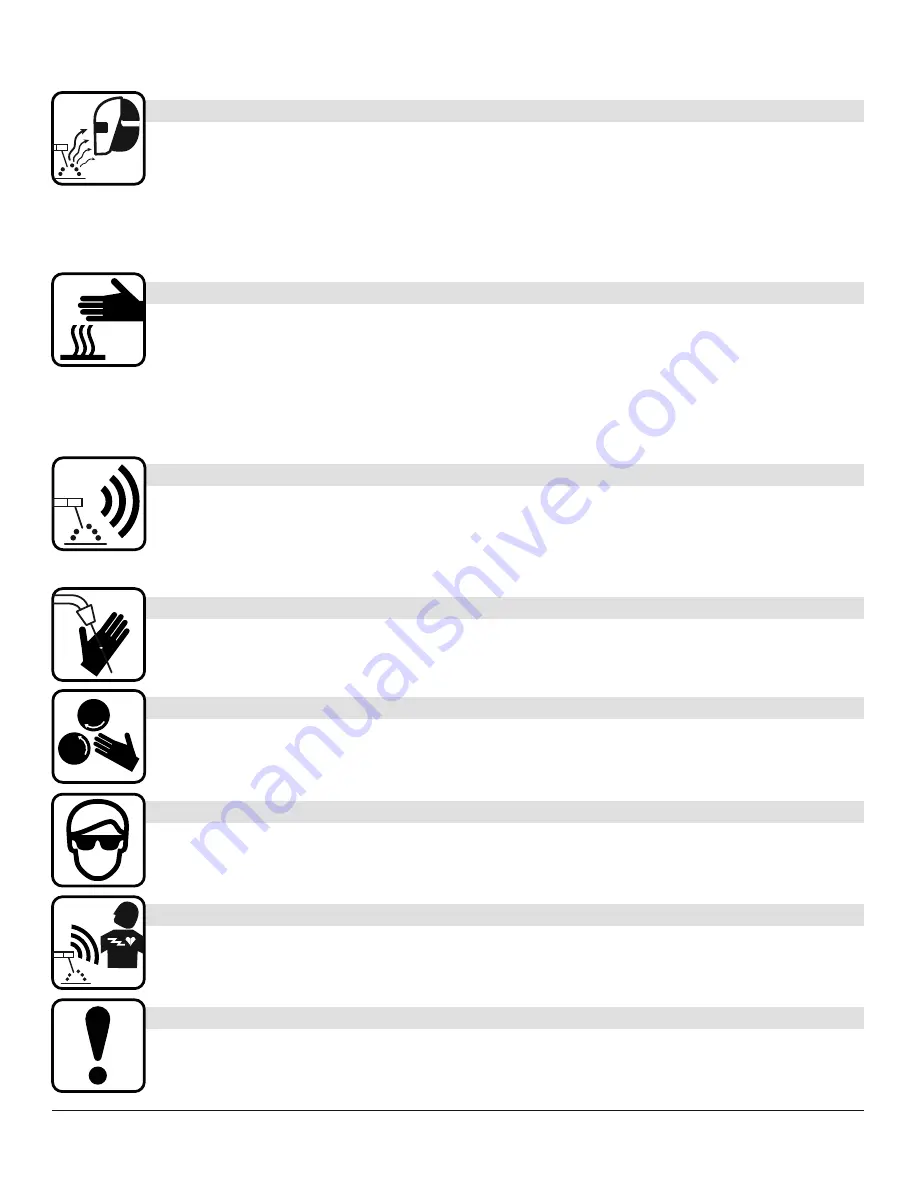
4
Eastwood Technical Assistance: 800.544.5118 >> [email protected]
ARC RAYS CAN BURN!
• Use a shield with the proper fi lter (a minimum of #11) to protect your eyes from sparks and the rays of the arc
when welding or when observing open arc welding (see ANSI Z49.1 and Z87.1 for safety standards).
• Use suitable clothing made from durable fl ame-resistant material to protect your skin. Protect nearby
individuals with a non-fl ammable barrier.
• Wear safety glasses under your welding helmet with side shields.
• If other persons are in the area of welding use welding screens to protect bystanders from sparks and arc rays.
HOT METAL WILL BURN!
• Electric welding operations cause sparks and heat metal to temperatures that will cause severe burns!
• Use protective gloves and clothing when performing any welding operations. Always wear long pants,
long-sleeved shirts and leather welding gloves.
• Make sure that all persons in the welding area are protected from heat, sparks and ultraviolet rays.
Use additional face shields and fl ame resistant barriers as needed.
• Never touch work piece until it has completely cooled.
ELECTROMAGNETIC FIELDS MAY BE DANGEROUS!
• The electromagnetic fi eld that is generated during arc welding may interfere with various electrical and electronic
devices such as cardiac pacemakers. Anyone using such devices should consult with their physician prior to
performing any electric welding operations.
• Exposure to electromagnetic fi elds while welding may have other health effects which are not known.
WELDING WIRE CAN BE DANGEROUS!
• Never point the welding gun at any part of the body, other people, or metal surfaces.
• Wear safety glasses and handle welding wire safety as it can be sharp and cause injury.
MOVING PARTS CAN BE DANGEROUS!
• Use care when working near the drive motor assembly as it can pinch.
• Do not put fi ngers or other body parts between moving parts.
FLYING METAL CHIPS CAN CAUSE INJURY!
• Welding, brushing, hammering, chipping, and grinding can cause fl ying metal chips and sparks.
• To prevent injury wear approved safety glasses.
MAGNETIC FIELDS CAN AFFECT PACEMAKERS!
• Any user with a pacemaker should consult their doctor before use.
• Anyone with a pacemaker should stay away from any electric welding before consulting a doctor.
SAFETY INFORMATION
NOTICE!
• Do not touch the contact tip with the unit turned “ON”. Turn the unit “OFF” before changing tips
or cleaning the nozzle.