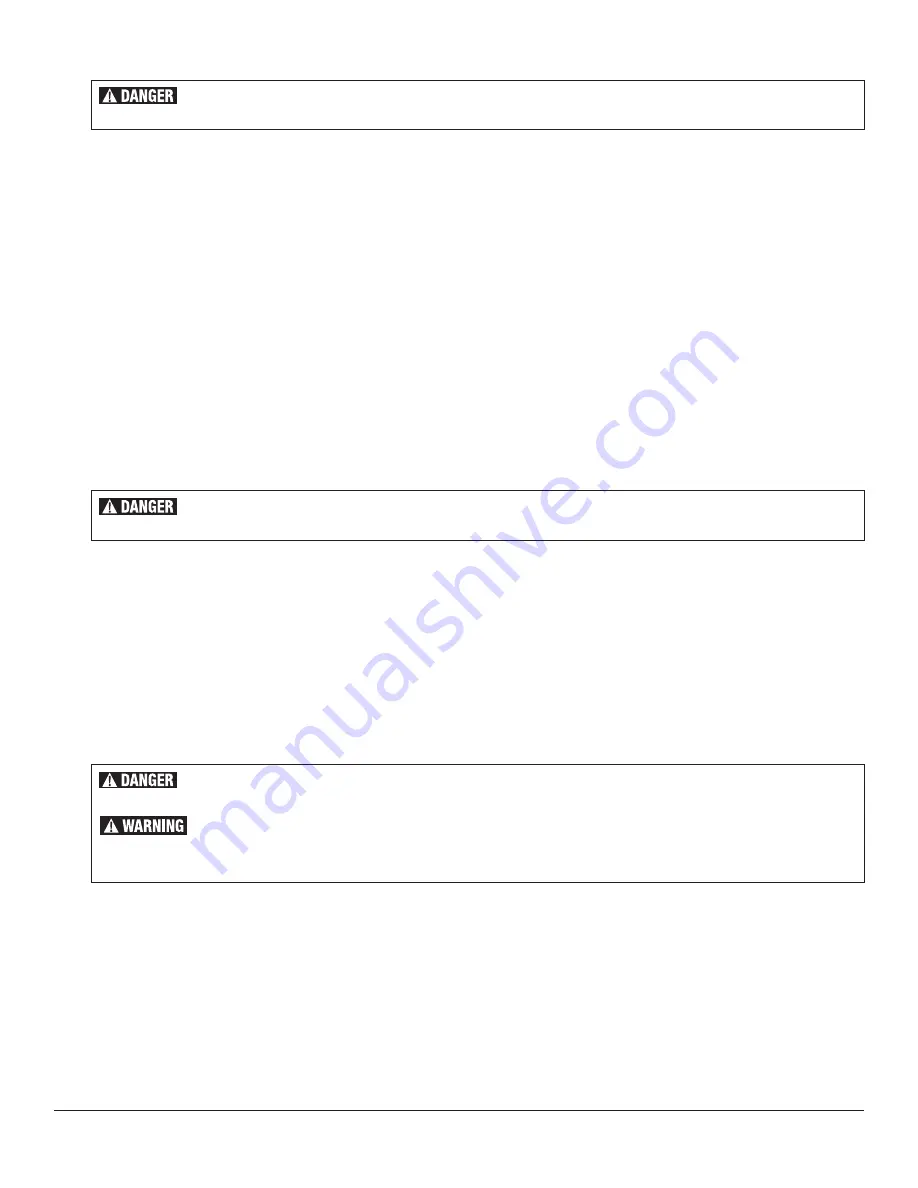
10
Eastwood Technical Assistance: 800.343.9353 >> [email protected]
FOR EASTWOOD MIG135 WELDERS WITH SET SCREW STYLE DRIVE ROLLER
1.
Unlock the Pressure Adjuster
(FIG. H1)
by pulling the top wing nut towards the rear of the welder.
2.
Lift the Rocker Arm
(FIG. H2)
and rotate the drive roller by hand until you have access to the set screw in the center of the roller.
3.
Loosen the set screw.
4.
Slide the drive roller off the shaft.
5.
Determine which size wire is going to be used and slide the Drive Roller back onto the shaft by lining up the set screw with the flat area on the shaft.
NOTE:
The stamped marking on the side of the Drive Roller indicates the size of the groove on the opposite side of the roller. The groove closest to the
drive motor is the groove that will be used. If setting up to use 0.023" (0.6mm) wire, the ‘0.6’ stamping should be facing the user when installing it.
6.
Tighten the set screw on the Drive Roller and lower the Rocker Arm
(FIG. H2)
back into place.
7.
Lift up on the Pressure Adjuster
(FIG. H1)
to put back in place and adjust as necessary.
SET UP OPERATION FOR SPOOL GUN WELDING
SET UP FOR SPOOL GUN WELDING
The Eastwood MIG135 is set up to use a spool gun which allows for easy feeding of aluminum wire to expand your welding capabilities. This is an optional acces-
sory and can be purchased separately from Eastwood.
1.
Switch the selector switch to the Spool Gun position.
2.
Open the side door of the welder and loosen the Torch Tensioner located on the side of the drive roller. If the standard welding gun is installed remove it
and its associated connector.
3.
Slide the brass body of the Spool Gun in through the front of the unit in the designated hole. Be sure to insert until it bottoms against the drive assembly or
a gas leak may occur.
4.
Connect the metal plug to the gun trigger connection on the front of the welder.
5.
Tighten the Torch Tensioner finger tight.
THREADING WELDING WIRE THROUGH THE SPOOL GUN
1.
Set the switch above the drive motor to the spool gun setting
(FIG. B1)
.
2.
Remove the thumb screw and clear plastic wire spool cover.
3.
Remove the thumb screw and spring tensioner that holds the wire spool on
(FIG. J1)
.
4.
Place wire spool on spindle and replace the thumb screw with spring tensioner and tighten till the point that the spool has some tension on it.
5.
Loosen the Brass Tensioner Thumb Screw
(FIG. J2)
until it is possible to feed the welding wire through the drive roller grooves.
6.
Feed the wire by hand from the spool into the inlet guide,
(FIG. J3)
past the drive rollers and into the wire inlet
(FIG. J4).
7.
Tighten the Brass Tensioner Thumb Screw
(FIG. J2)
until it applies light pressure onto the welding wire. If this is too tight it will deform the wire and cause
feeding issues, if it is too loose the drive roller will slip on the wire.
8.
Remove the nozzle and contact tip.
ELECTRIC SHOCK HAZARD!
Turn welder off and unplug from electrical outlet.
ELECTRIC SHOCK HAZARD!
Turn welder off and unplug from power source before installing or removing Spool Gun.
ELECTRIC SHOCK HAZARD!
Turn welder off and unplug from electrical outlet.
WELDING WIRE CAN BE DANGEROUS!
• Never point the welding gun at any part of the body, other people, or metal surfaces.
• Wear safety glasses and handle welding wire safety as it can be sharp and cause injury.
Содержание MIG 135
Страница 1: ...MIG135 WELDER INSTRUCTIONS Item 12011...