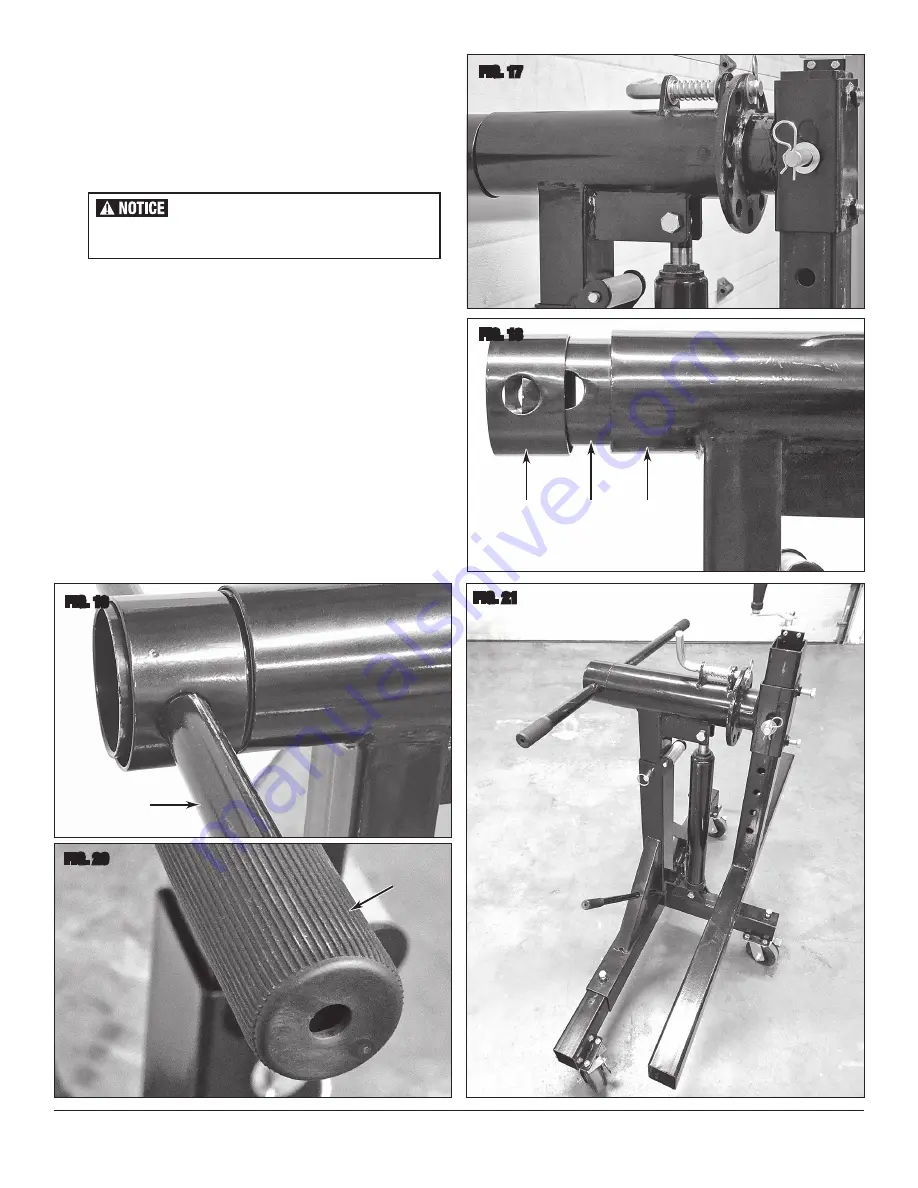
SPINDLE AND SUPPORT ARM “TEE” BEAM ASSEMBLY [H] & [D] TO
MAIN SUPPORT FRAME & SPINDLE SUPPORT ASSEMBLY [A] & [E].
1.
Remove the Retaining Clip and Washer from the Spindle Latch Pin and
set aside for reinstallation.
2.
Apply a liberal amount of high-quality synthetic, high-load wheel
bearing grease or an anti-seize compound to the bearing surfaces of
the Spindle Support and outside of the Spindle before insertion.
3.
Lift the Spindle and “Tee” Beam Assembly
[H]
and
[D]
and insert the
Spindle into the Sleeve. Push it in fully engaging the Latch Pin with the
hole nearest the 12:00 position of the 10 in the Rotation Lock Plate
(FIG 17)
.
4.
Reinstall the previously removed Retaining Clip and Washer onto the
Spindle Latch Pin
(FIG 17)
.
5.
Slide the Spindle Retaining Collar
[J]
over the protruding inboard end
of the Spindle
[H]
and align the through holes
(FIG 18)
.
6.
Insert the Spindle Rotating Bar
[K]
through the Spindle Retaining
Collar
[J]
and the Spindle
[H] (FIG 19)
.
7.
Push the rubber Spindle Rotating Bar Grips
[L]
fully onto the ends of
the Spindle Rotating Bar
[K] (FIG 20)
.
8.
The assembly should appear as in
FIG 21
. Repeat assembly procedure
for opposite end.
To order parts and supplies: 800.343.9353 >> eastwood.com
9
The assistance of a capable assistant is required for
the following step.
FIG. 17
FIG. 18
FIG. 19
FIG. 20
FIG. 21
E
✓
✓
✓
H
J
✓
K
L
✓