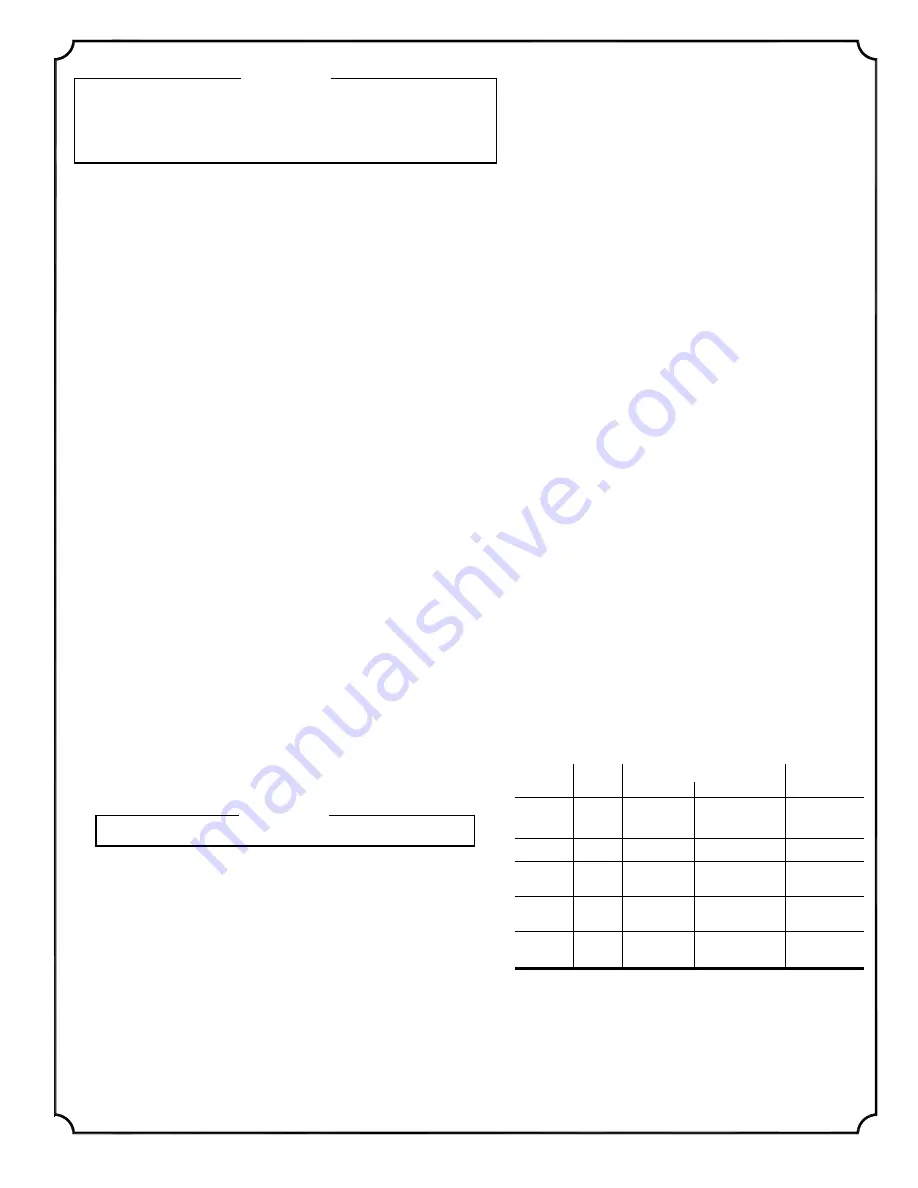
3
Form C-1206
TO REPLACE EMERY WHEELS
BBS32
1. Remove left hand cap – 2 screws (300C8-2)
– lift out emery wheel with bushing.
2. Remove screw (20C13-30).
3. Coat new emery wheel spindle with oil and
re-assemble to arm (620C1-21).
4. Repeat above steps for right hand emery wheel.
NOTE
Left and Right caps must be replaced in the same man-
ner that they were removed.
BBB32
1. Remove cap (35C5-45) and lift out emery
wheel and bushing. Then remove screw
(304C10-3) from left hand emery wheel and
pull out emery wheel (541C1-10). Replace
wheels and re-assemble.
2. Adjust wheels as outlined for BBR.
BBS32
Remove sharpener (637C1-23) from machine and disas-
semble as shown in diagram page 5 – replace emery wheel
(541C1-22). Lubricate – re-assemble – re-install.
220 VOLT MACHINES
When using the 220 volt machine on three phase outlets,
use adaptor (509C1-54) by simply mounting this adaptor
on the (25C5-49) single phase attachment plug. The two
live leads of the (615C1-5) three phase attachment plug
can be utilized for the power this machine requires.
KNIFE GUARD ADJUSTMENT
Knife guards (25C4-144) and (25C4-106) should be regu-
lated in a manner that only allows the material to pass
through the material to be cut.
REPLACEMENT BLADES
CAUTION
Do not use sewing machine oil or detergent oil. It is entirely too
light for cutting machine lubrication. For best results use spe-
cially compounded Eastman Oil or at least a good grade SAE 30
motor oil. Do not oil base plate rollers.
Do not overload with grease as machine will run hot at gear assembly.
Remove knife and gear and remove excessive grease.
MAINTENANCE PROCEDURES
1. Keep rollers of the base plate free of lint. Motor should be
blown clear of lint and dust weekly using air hose at 90
P.S.I.
2. Periodically check terminal pins on the terminal block and
the terminal in the attachment plug to insure full contact.
3. When replacing the knife on your cutting unit be sure to
clean out any lint build up between knife and standard.
4. If the cutting unit seems to lag or run hot when not cut-
ting, run machine with knife removed to check for over-
greasing or any obstructions.
5. When changing knife or cleaning machine check all screws
and nuts for tightness.
6. Carefully remove spring loaded brushes – replace brushes
when worn to less than .165 inches (4.2mm) or if springs
are less than .350 inches (9.00mm).
7. When your machine performance does not appear to be
up to par, contact your Eastman Machine authorized
dealer.
MOTOR BRUSH REPLACEMENT
When replacing brushes (36C1-13) in the motor, carefully remove the
(54C4-43) brush caps, remove the (34C1-58) brush with springs and re-
place brushes accordingly.
KNIFE SHARPENING
BBB32R – BBS32 – Connect power cord and switch motor on. To
obtain a fine, keen edge on the blade, press lightly on sharpener lever
or button with a constant pressure.
KNIFE SHARPENER REPLACEMENT
BBB32 – BBS32
CAUTION
Disconnect from electric power source when servicing.
As the emery wheels wear away and become farther apart, they must
be adjusted. Proceed as follows:
1. Slightly loosen four (4) slotted screws (300C8-2) holding
adjusting bushings in place.
2. With fingers, turn adjusting bushings (20C6-23) until em-
ery wheels are as close together as possible without touch-
ing and centered over knife. Both wheels should grind at
the same time when pressed lightly against knife with a
maximum 1/32 inch clearance between wheels. The sharp-
ened edge (bevel) should be no more than 1/16 inch.
3. Tighten four (4) screws.
PLEASE SPECIFY MACHINE NAME AND SERIAL NUMBER WHEN ORDERING PARTS.
Machine
Part Number
Blade
Type
Size
Carbon
High Speed
Type
BBS32
2 1/2"
80C1-114
80C1-114HS
Round
80C1-138
*
—
Hex
BBB32
3 1/4"
80C1-84
*
80C1-84HS
Round
D2
2 1/4"
—
80C1-147HS
*
Round
D2H
80C1-149HS
Hex
BUZZ
2-1/32"
—
80C1-123HS
*
Semi Square
80C1-133HS
Octagon
*Standard Blade
Содержание BBS32
Страница 5: ...5 Form C 1206 ...
Страница 7: ...7 Form C 1206 TYPE BBB32 ...
Страница 9: ...9 Form C 1206 779 WASHINGTON STREET BUFFALO NEW YORK 14203 ...