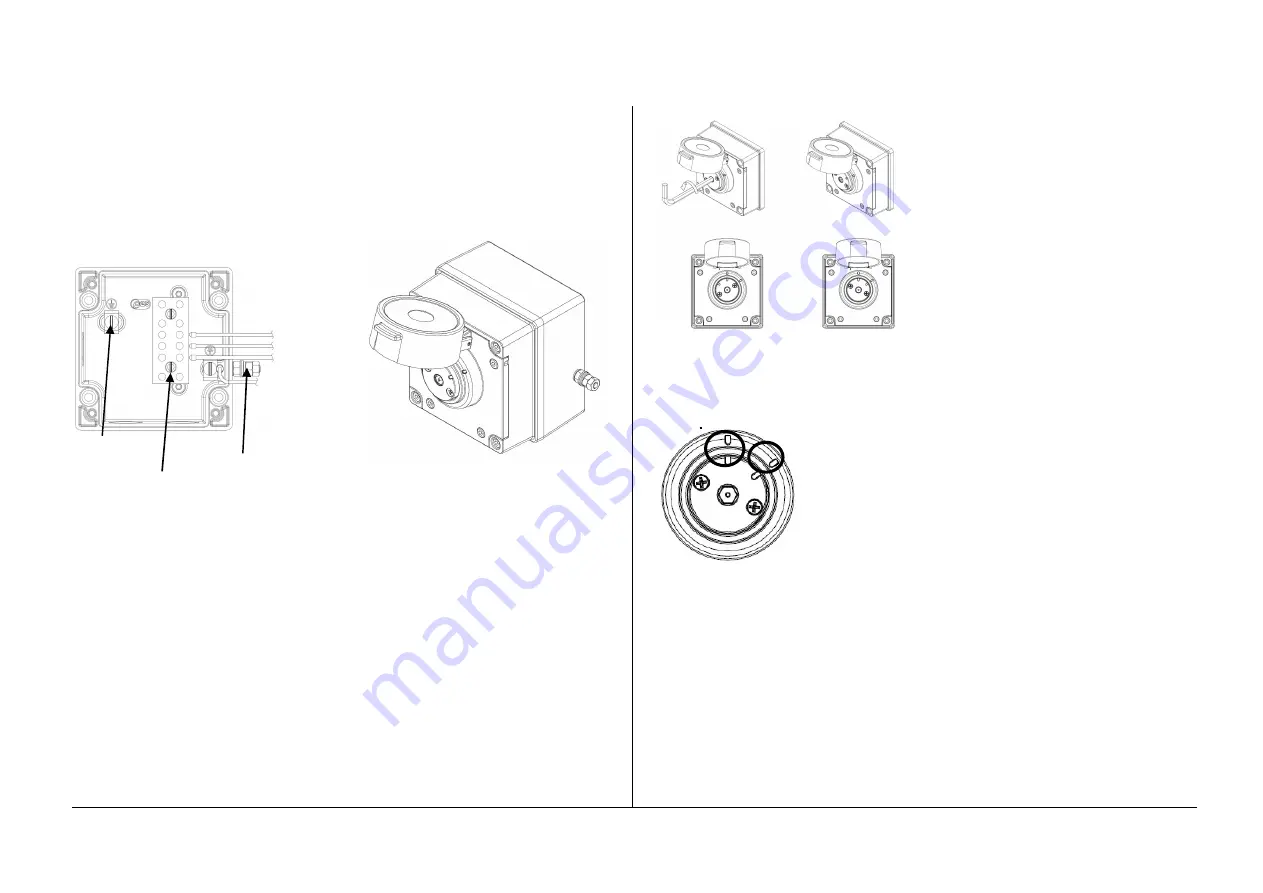
European Safety Systems Ltd.
Impress House, Mansell Road, Acton, London W3 7QH
[email protected] Tel: +44 (0)208 743 8880
Document D150-00-751-IS Issue 4 11-08-2022
Sheet 2 of 2
www.e2s.com Fax +44 (0)208 740 4200
6)
Earthing
The unit has both internal and external earth
terminals.
It is recommended that a cable crimp lug is used
on the earth wires.
The internal earth wire is placed under a earth
clamp which will stop the cable twisting. This is
secured by an M4 screw and spring washer.
The external earth lug should be located between
the two M5 washers provided and securely locked
down with the M5 spring washer and two locknuts.
Internal Earth
terminal
External
Earth Stud
Terminal block
7)
Cable connections
There are 3 off cable entries for M20x1.5 cable
glands or stopping plugs.
Cable glands or stopping plugs must be rated IP66.
The unit can be wired in a number of different ways
depending on the resistor combination selected.
Option 1 – EOL (End of line) Resistor
Option 2 – Series (In line) resistor
Option 3 – Series and EOL resistors
The equipment needs to be installed with ATEX
and/or IECEx certified Zener Barriers or Galvanic
Isolators.
For wiring schematic refer to drawing D150-06-051
8)
Testing unit operation
The tool reset unit can be tested without the need
to replace any element.
To test, lift the cover lift flap to reveal the tool reset
button. The button should be pressed into the body
to activate the unit and place it into the operated
condition.
The call point switch will now change over it’s
contacts to operate the alarm.
Once testing is complete the unit needs to be reset
from the operated condition.
Using the special reset tool provided the tool reset
button is rotated anticlockwise by an angle of 55º,
see guide alignment marks on button and cover,
shown below (1). The tool reset button should pop
back up to its original position.
Ensure that the tool reset button has also twisted
back clockwise by 55º to its original position see
guide marks on button and cover, shown below (2).
The unit is now reset.
1. On operated unit
2. Button should pop
Twist tool reset button up and twist back to
Anticlockwise 55º
original position
with special key to reset
Note: use
alignment marks
circled to indicate
the tool reset
buttons status
/position.
Unit currently
shown as ‘standby
condition’
Resetting an operated unit is the same as resetting
a tested unit.