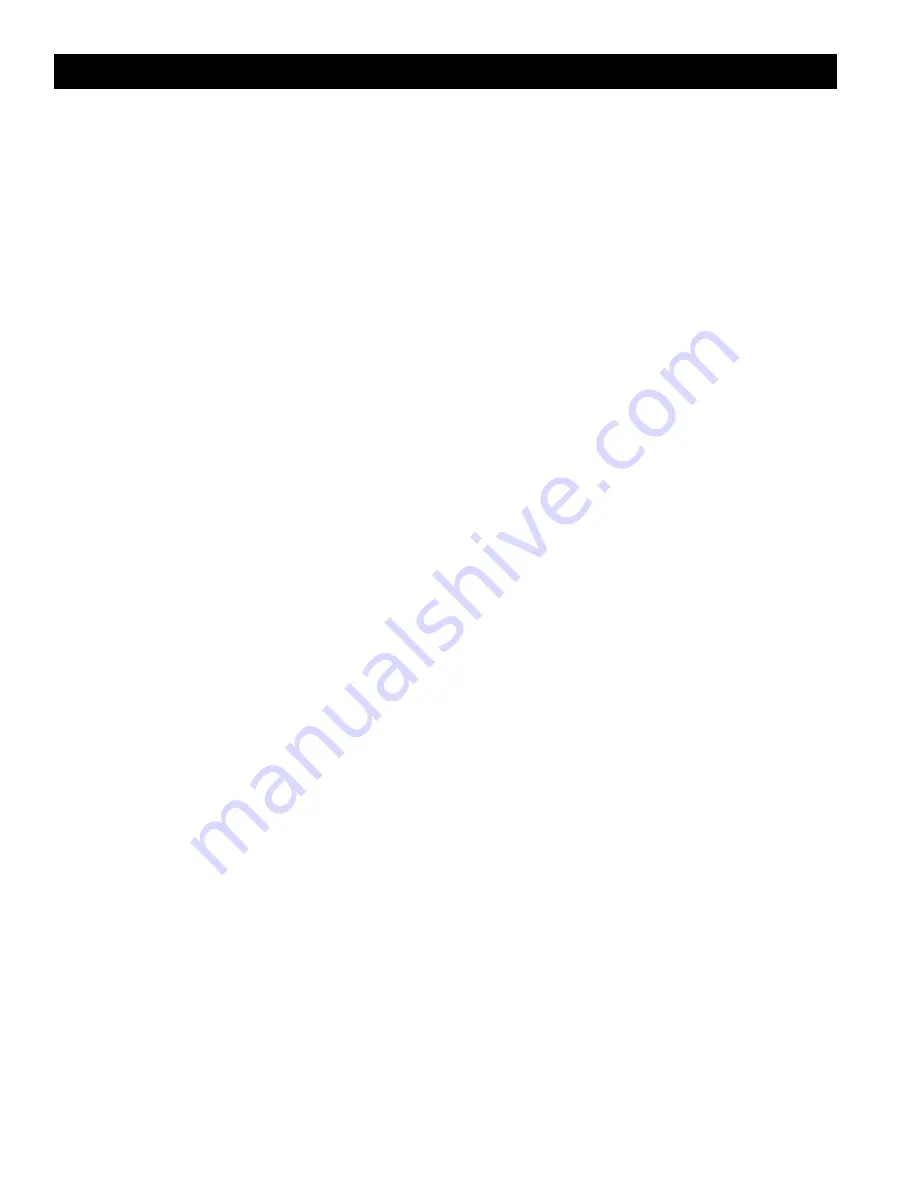
The list below represents some of the most critical installation
requirements that, when overlooked, often result in operational
problems, down time and needless parts replacement. This
is not a complete list. Before performing any troubleshooting
procedures use the list below to check for installation errors.
Costs to correct installation errors are not covered under the
limited warranty. Ensure all installation requirements and
instructions in this manual have been followed.
LOCATION
1. Ensure the HPWH is located where there is a adequate
supply of ambient heat for optimal performance or that the
HPWH is ducted to such a location.
2. Ensure required clearances are maintained and there is
access for servicing. See Clearances on page 11.
3. Ensure the HPWH is properly supported. See Ceiling
Suspension and Pad Mounting on page 16.
AIR FLOW & DUCTING
4. Ensure all supply and return ductwork connected to the
HPWH is properly sized, does not exceed maximum
equivalent length requirements and is installed according to
the instructions in this manual. See Air Flow and Ducting on
page 19.
5. Ensure all supply duct work is insulated to prevent
condensation from forming on the ductwork.
6. Ensure all return air duct is insulated if the return air
temperatures are expected to fall below the surrounding
room air temperature during normal operation.
WATER PIPING
7. Ensure the outlet (supply) and inlet (return) water piping
connected to the HPWH are not less than the connection
size on the unit. See Table 1 on page 9.
8. Ensure swing-type check valves (not spring-loaded types)
are installed on outlet lines of all heat pumps plumbed in
parallel to prevent hot water short-circuiting.
9. When the HPWH is connected to a storage tank ensure the
storage tank is equipped with a properly rated and sized
Temperature and Pressure (T&P) relief valve. Refer to the
storage tank manufacturer’s instructions for T&P valve sizing
and installation requirements.
NOTE:
This is a critical installation requirement that must
not be overlooked. Call the toll free technical support
phone number on the back cover of this manual for further
assistance.
10.
DO NOT
install a T&P valve in the outlet (supply) water line
of the HPWH unless required by local code.
11. Ensure the maximum lengths of 25 equivalent feet of
supply piping and 25 equivalent feet of return piping are not
exceeded on HPWH units equipped with a factory installed
circulation pump. Exceeding these lengths will cause the unit
to malfunction and/or the control system to lock out.
12. Ensure isolation valves are installed on the HPWH supply
and return water line at the storage tank for servicing and
purging the air from the HPWH during start-up.
13. Ensure the cold water supply is not connected directly to or
Tee fitted to the inlet water line on the HPWH. See the Service
and Installation Notes for Inlet & Outlet Water Temperature
on page 10. See Figure 7 and Figure 8 on page 18.
14. On two tank preheat piping configurations ensure the cold
INSTALLATION CHECKLIST
22
water supply is not connected to the back up water heater.
15. Connect building recirculation loop piping to the backup
water heater inlet on two tank preheat piping configurations.
16. Ensure the building recirculation loop pump is controlled by a
field supplied line thermostat and that it stops the pump when
the recirculation line is hot. See Building Recirculation Pump
Wiring Diagram on page 4
0
.
17. When the HPWH unit is installed above the storage tank
install a Tee fitting at a high point in the outlet water line with
a purge valve to bleed air during start up.
18. Though not required, the manufacturer recommends
installing a strainer at the inlet water line on the HPWH to help
prevent scale build up in the heat exchanger. Service costs to
clear blockages from the HPWH unit’s heat exchanger due to
debris are not covered under the limited warranty.
CONDENSATE DRAIN
19. Ensure there is a water trap installed in the condensate line
at the HPWH. Condensate will not drain without a water trap.
20. Ensure the condensate drain is properly connected to
the HPWH and draining freely to a suitable floor drain or
condensate lift pump that discharges condensate to a remote
location. See Condensate Drain Line on page 18.
ELECTRICAL
21. BEFORE ENERGIZING THE UNIT ensure the power supply
voltage and phase matches the requirements on the HPWH
rating label. Damage resulting from applying the wrong
voltage or phase is not covered under the limited warranty.
22. On HPWH units connected to 208 VAC power supplies ensure
the transformer has been properly configured. Damage
caused by failure to configure the transformer properly is
not covered under the limited warranty. See Transformer
Configuration 208 VAC Models on page 17.
23. Ensure the power supply breaker
or
the
fuses disconnect
switch are within the
requirements for the unit as shown on
the
HPWH rating label.
24. Ensure the power supply wiring meets the MCA (Minimum
Circuit Ampacity) requirements shown in this manual and on
the HPWH rating label.
25. Ensure the HPWH is properly grounded according to the
instructions in this manual and local code requirements.
26. Ensure the power supply connections to the HPWH are
connected properly and securely tightened.
27. Ensure all electrical connections in the HPWH control panel
are securely tightened.
28. When the factory supplied Digital Tank Thermostat is used:
• Insure the thermostat and sensor are installed
properly. See Digital Tank Thermostat Installation and
Temperature Sensor Installation on page 19.
• Ensure the Temperature Sensor and supplied Sensor
Well have been installed in a designated temperature
control opening in the lower part of the storage tank.
• Ensure the supplied Temperature Sensor is coated with a
suitable heat transfer compound (paste).
• Ensure the Temperature Sensor has been properly wired
to the terminal strip of the Digital Tank Thermostat. See
Figure 1
5
on page
37
.
Содержание WH-35
Страница 2: ......
Страница 32: ...UNIT WIRING DIAGRAMS FUSE SIZES 208 230 VAC SINGLE PHASE 60 HZ 32 ...
Страница 33: ...UNIT WIRING DIAGRAMS FUSE SIZES 208 230 VAC THREE PHASE 60 HZ WH 35 WH 55 and WH 75 only 33 ...
Страница 34: ...UNIT WIRING DIAGRAMS FUSE SIZES 208 230 VAC THREE PHASE 60 HZ only 34 ...
Страница 35: ...UNIT WIRING DIAGRAMS FUSE SIZES 460 VAC THREE PHASE 60 HZ 35 ...
Страница 36: ...UNIT WIRING DIAGRAMS FUSE SIZES 460 VAC THREE PHASE 60 HZ only 36 ...