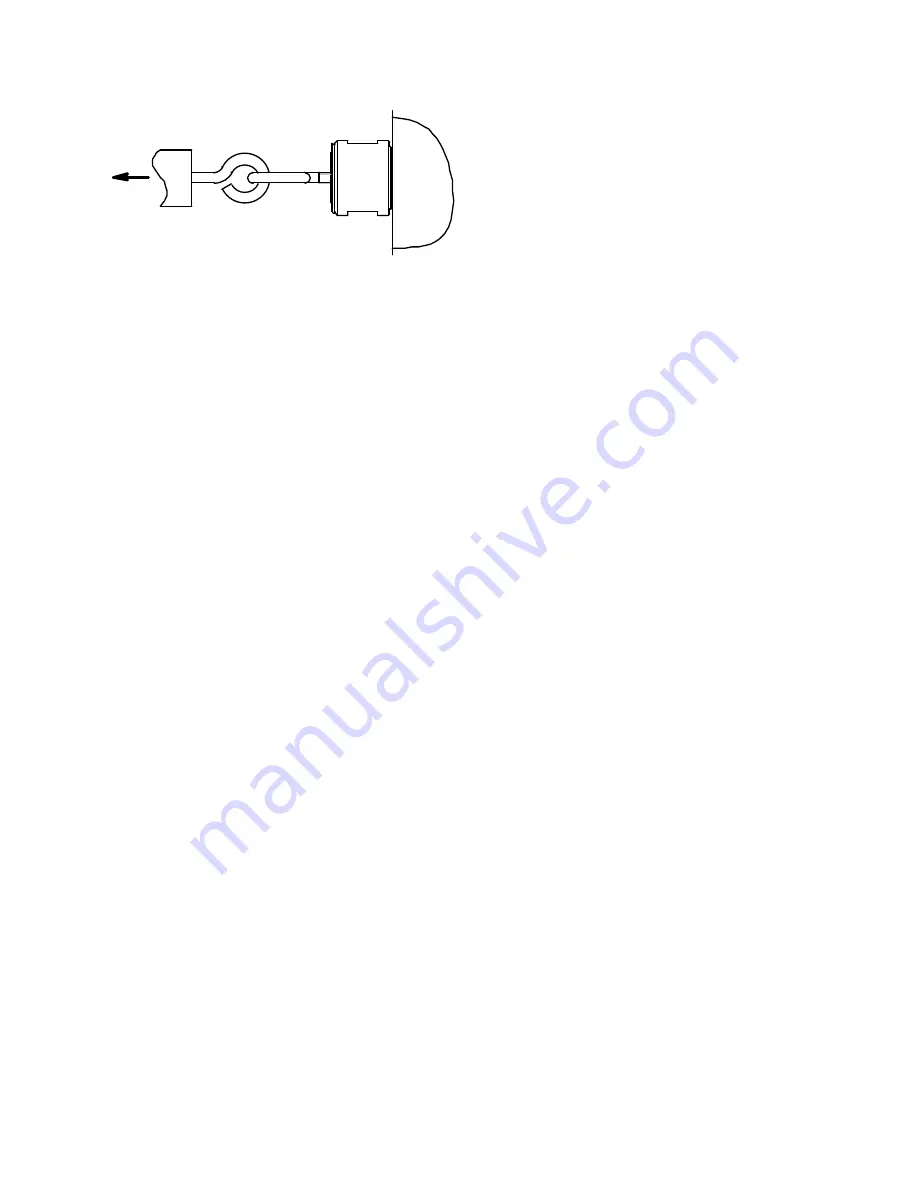
Rev B, ECN 12897, 08/18/16
5
FIGURE 4
PROPER TENSILE LOADING
The arrangement shown in Figure 4 ensures
that the load is applied centrally to the sensor
without bending moments and transverse loading.
One important point to keep in mind when
making tensile measurements is that, due to limits in
the design of the internal preload structure of these
sensors, the
maximum tensile force is limited
to
500 Lbs
. in this series.
If this level is exceeded,
the sensor may be destroyed and the load will be
suddenly released.
This could engender dangerous
situations for personnel and equipment if this
eventuality is not fully understood.
Remember that the maximum force is the
combination of both static and dynamic tensile
forces. For example, if the sensor is supporting a
static load of 250 Lbs., the maximum dynamic range
possible is 250 Lbs, (500 - 250).
QUASI-STATIC CONSIDERATIONS
Close to DC measurements are possible
with the 1051C when used with a laboratory type
charge amplifier such as the model 4165. These
force sensors are calibrated at the factory by placing
a traceable compressive force on them, (with a
proving ring) then rapidly removing it and capturing
the resultant step function on a digital storage
oscilloscope. This is a very accurate and repeatable
method for calibration of these sensors.
MAINTENANCE AND REPAIR
The sealed construction of model 1051C
precludes field maintenance. Should you experience
a problem with your sensor, contact the factory to
discuss the problem with one of our sales engineers.
If the instrument must be returned to the factory, you
will be issued a Returned Materials Authorization
(RMA) number so we may better follow the
instrument through the evaluation process. Please
do not return an instrument without first obtaining the
RMA number. There is no charge for the evaluation
and you will be notified of any charges before we
proceed with a repair.
PROPER TENSILE LOADING
USING THREADED HOOK EYES
F