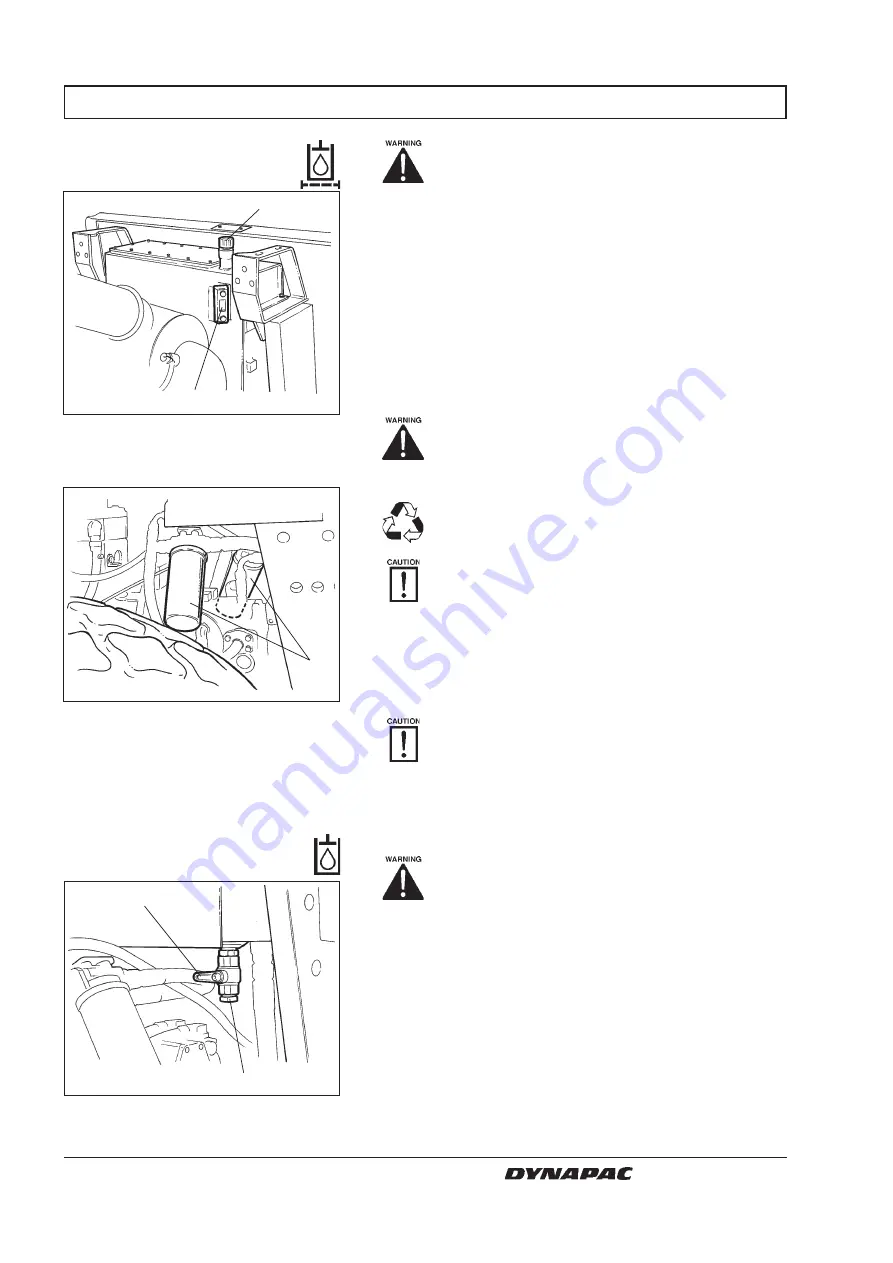
22
CA152 M152EN3
Place the roller on a level surface. Switch
the engine off and push in the reserve/
parking brake knob for all checking and
adjustments on the roller, unless otherwise
specified.
Undo the cover/bleeder filter (2) on top of the reservoir
so that over-pressure inside the reservoir can be elimi-
nated.
Check that the bleeder filter (2) is not blocked – air
should flow freely through the cover in both directions.
If there is a blockage in either direction, clean the filter
with a little diesel oil and blow through with compressed
air until the blockage disappears, or replace the cover
with a new one.
Always use protective goggles when work-
ing with compressed air.
Clean thoroughly around the oil filters.
Remove the oil filters (1) and dispose of them
in an approved manner. They are single-use
filters and cannot be cleaned.
Check that the old sealing rings do not remain
stuck on the filter holders, otherwise this might
give rise to oil leakage between the old and
new seals.
Clean the filter holder sealing surfaces thoroughly.
Apply a thin film of hydraulic fluid on the seals of the
new filter. Screw on the filter by hand.
First tighten the filter until its seal is in contact
with the filter attachment. Then turn an addi-
tional half revolution. Do not over-tighten the
filter as this might damage the seal.
Start the engine and ensure that there is no leakage of
hydraulic fluid from the filters. Check level of fluid in the
sight glass (3) and top up as required.
Make sure there is adequate ventilation
(extraction) if the diesel engine is run in-
doors. Risk of carbon monoxide poisoning
EVERY 1000 OPERATING HOURS (Every six months)
1
2
3
2
1
Fig. 37 Hydraulic tank, underside
1. Drainage tap
2. Plug
Hydraulic tank – Drainage
Fig. 36 Engine compartment
1. Hydraulic fluid filters (x2)
Fig. 35 Hydraulic fluid tank
2. Filler cover/bleeder filter
3. Sight glass
Hydraulic fluid filter
– Change
Condensate in the hydraulic reservoir is removed via
the drainage tap (1).
Drainage should be performed when the roller has been
standing for a long period of time, for example over-
night. Drain as follows:
Remove the plug (2).
Place a container under the tap.
Open the tap (1) and let any trapped condensate run out.
Shut the drainage tap.
Refit the plug.
Содержание CA152D
Страница 2: ...19 ILF015WO1...