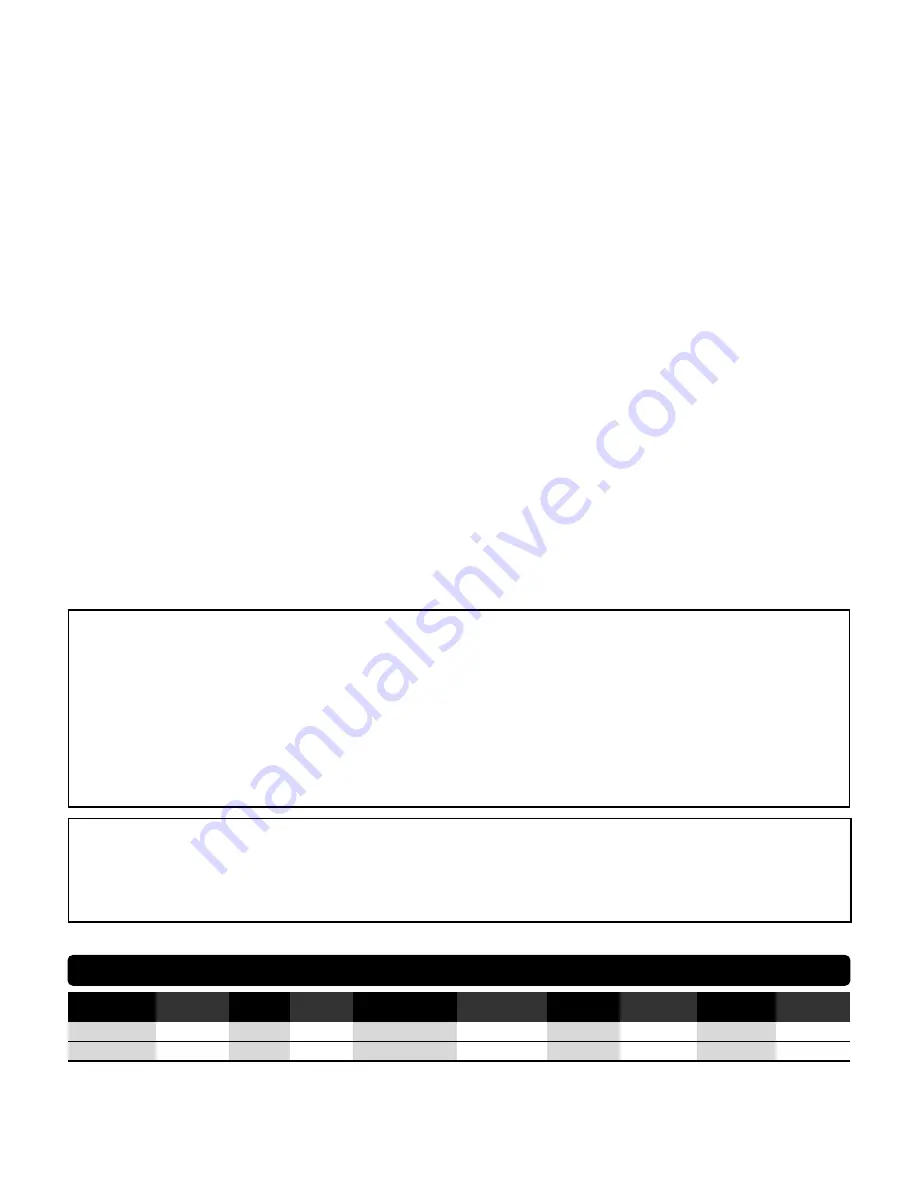
Machine Specifications
6
Model
Motor
Motor
Sound
Maximum Air Flow
Collet Insert
Air Pressure
Weight
Length
Height
Number
hp (W)
RPM
Level
SCFM (LPM)
Size
PSIG (Bars)
Pound (kg)
Inch (mm)
Inch (mm)
56723
.4 (298)
25,000
77 dB(A)
24 (680)
1/4" & 6 mm
90 (6.2)
1.6 (.7)
9.7 (247)
5.9 (150)
56727
.4 (298)
5,000
80 dB(A)
25 (708)
1/4" & 6 mm
90 (6.2)
2.3 (1.0)
10 (254)
8.3 (212)
Additional Specifications: Air Inlet Thread 1/4" NPT • Hose Size 1/4" or 6 mm
Sound Level is the pressure measurement according to the method outlined in ISO regulation ISO-15744.
Lifetime Warranty
All Dynabrade portable pneumatic power tools are rigorously inspected and performance tested in our factory before shipping to our customers. If a
Dynabrade tool develops a performance problem and an inherent defect is found during normal use and service, Dynabrade will warrant this tool
against defects in workmanship and materials for the lifetime of the tool. Upon examination and review at our factory, Dynabrade shall confirm that
the tool qualifies for warranty status, and will repair or replace the tool at no charge to the customer. Normally wearable parts and products are NOT
covered under this warranty. Uncovered items include bearings, contact wheels, rotor blades, regulators, valve stems, levers, shrouds, guards, O-
rings, seals, gaskets and other wearable parts. Dynabrade’s warranty policy is contingent upon proper use of our tools in accordance with factory
recommendations, instructions and safety practices. It shall not apply to equipment that has been subjected to misuse, negligence, accident or
tampering in any way so as to affect its normal performance. To activate lifetime warranty, customer must register each tool at www.dynabrade.com.
Dynabrade will not honor lifetime warranty on unregistered tools. A one-year warranty will be honored on all unregistered portable pneumatic power
tools. Lifetime warranty applies only to portable pneumatic tools manufactured by Dynabrade, Inc. in the USA. Lifetime warranty applies only to the
original tool owner; warranty is non-transferable.
Notice
All Dynabrade motors use the highest quality parts and metals available and are machined to exacting tolerances. The failure of quality pneumatic
motors can most often be traced to an unclean air supply or the lack of lubrication. Air pressure easily forces dirt or water contained in the air supply into
motor bearings causing early failure. It often scores the cylinder walls and the rotor blades resulting in limited efficiency and power. Our warranty obligation
is contingent upon proper use of our tools and cannot apply to equipment which has been subjected to misuse such as unclean air, wet air or a lack of
lubrication during the use of this tool.
3. Model 56723:
Install the
02649
Bearing into the front bearing plate and install these onto the rotor.
4.
Install the
01435
Collet Body onto the
01475
Rotor. (Torque to 17 N•m/150 in. lbs.)
5. Model 56727:
Position the
54553
Rotor with the
01479
Spacer in the arbor press with the pinion gear pointing up.
6.
Use the raised center of the
96240
Bearing Press Tool and arbor press to install the
02649
Bearing, shims and
01478
Front Bearing Plate.
7.
Use a .001" (0.3 mm) thick feeler gauge to check the clearance between the bearing plate and the face of the rotor.
8.
Clearance should be .001"-.0015" (0.3-0.4 mm). Note: If the clearance needs adjustment, repeat steps 2-6. Add or remove shims as required.
9.
Lubricate the
01480
Vanes with the
95842
Dynabrade Air Lube 10W/NR (or equivalent). Install vanes into the rotor.
10.
Install the
01476
Cylinder so that the air inlet opening will align with the air inlet opening in the
02673
Rear Bearing Plate.
11.
Use the RAISED OUTSIDE DIAMETER of the
96242
Bearing Press Tool and the arbor press to install the
02696
Bearing into the
02696
Rear Bearing Plate.
12.
Use the RAISED CENTER of the
96242
Bearing Press Tool and the arbor press to install the bearing/plate onto the rotor.
13.
Carefully press the bearing/plate down until it just touches the cylinder. This will establish a snug fit between the bearing plates and the cylinder.
14.
Apply a small amount of white grease to the seal of the
02696
Bearing, and stick the
02679
Shield against the bearing. Carefully slide the motor assembly
into the housing.
15. Model 56723:
Install the
01580
Felt Silencer onto the front of the air motor.
16. Model 56727:
Install the flat side of the
50778
Spacer against the
02649
Bearing. Install the planetary gear assembly into the
50776
Housing, aligning the
lubricant and set screw access holes with the notched openings in the ring gear. Apply a small amount of Loctite #567 (or equivalent) to the threads of the
50784
Set Screw and install with a 5/64" hex key.
17.
Apply a small amount of Loctite #567 (or equivalent) to the threads of the rear exhaust cover and install it onto the housing. (Torque to 28 N•m/250 in. lbs.)
18. Model 56727:
Install the
50011
Collet Body.
19.
Install the shroud and secure it with the clamp.
Motor Assembly Complete.
Throttle Positioning Procedure:
IMPORTANT: Perform this procedure carefully. Do not entirely separate the 01546 or 50776 Housing from the valve housing. Loosen the 01461 Lock Nut
only enough to make the throttle lever adjustment.
1.
Place the
52296
Repair Collar around the valve housing and secure it in a vise so that the
01546
or
50776
Housing is pointing up.
2.
Slip the
01558
Collar down onto the valve housing to expose the
01461
Lock Nut.
3.
With a firm hold on the
01546
or
50776
Housing, use a 34 mm or an adjustable wrench to turn the lock nut clockwise to loosen the
01546
or
50776
Housing
from the valve housing.
4.
Place the throttle lever in the desired position.
Note:
Allow for additional rotation of the
01546
or
50776
Housing as the
01461
Lock Nut is tightened.
5.
Grasp the
01546
or
50776
Housing firmly to limit rotation. Use a 34 mm or an adjustable wrench to tighten the
01461
Lock Nut. (Torque to 45 N•m/400 in. lbs.)
6.
Slip the
01558
Collar back over the
01461
Lock Nut.
Throttle Positioning Procedure Complete. Tool Assembly Complete.
Important:
Motor should now be tested for proper operation at 90 PSIG. If motor does not operate properly or operates at a higher RPM than marked on the
tool, the tool should be serviced to correct the cause before use. Before operating, place 2-3 drops of Dynabrade Air Lube (P/N
95842
) directly into air inlet
with throttle lever depressed. Operate tool for 30 seconds to determine if tool is operating properly and to allow lubricating oils to properly penetrate motor.
Loctite
®
is a registered trademark of Loctite Corp.