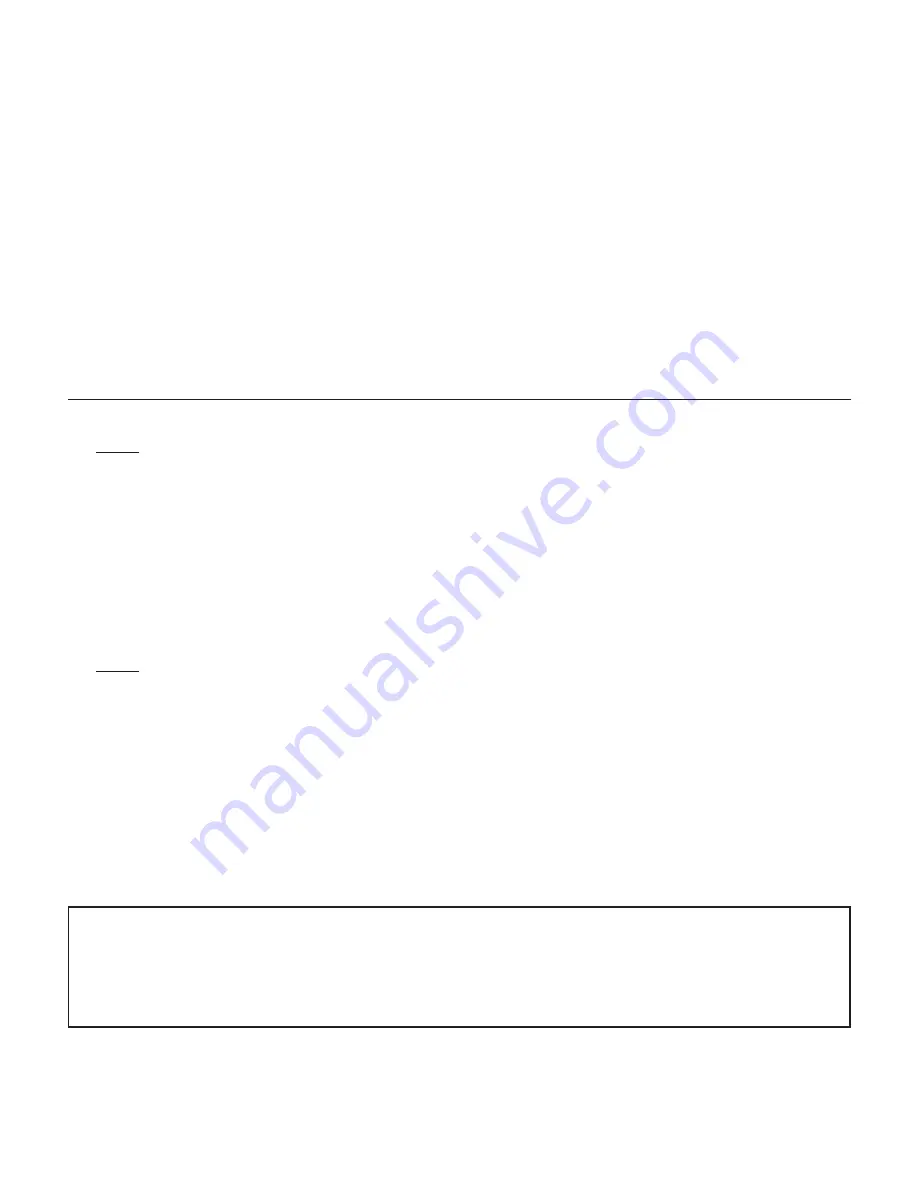
Maintenance Instructions
Important:
To keep tools safe a Preventative Maintenance Program is required whenever portable power tools are used. The program shall include
inspection of air supply lines, air line pressure, proper lubrication and repair of tools. Refer to ANSI B186.1 and EN 792 for additional maintenance information.
•
Use only genuine Dynabrade replacement parts to insure quality. To order replacement parts, specify
Model#
,
Serial#
and
RPM
of your air tool.
•
It is strongly recommended that all Dynabrade rotary vane air tools be used with a Filter-Regulator-Lubricator to minimize the possibility of misuse due
to unclean air, wet air or insufficient lubrication. Dynabrade recommends the following:
11411
Air Line Filter-Regulator-Lubricator — Provides accurate air
pressure regulation, two-stage filtration of water contaminants and micro-mist lubrication of pneumatic components. Operates up to 55 SCFM @ 100
PSIG has 1/2" NPT female ports.
•
Lubricate wick system through the angle gear oil fitting with 2-3 plunges for every 24 hours of use, to achieve maximum gear life.
Important:
Use only the recommended angle gear oil for the wick system. Do not contaminate the wick with any other oil or grease product.
(Order
95848
Gear Oil and
95541
Gun) Always prime pump to insure good flow before lubricating gears.
•
Dynabrade recommends one drop of air lube per minute for each 20 SCFM (example: if the tool specification states 40 SCFM, set the drip rate on the
filter-lubricator to 2 drops per minute). Dynabrade Air Lube (P/N
95842
: 1 pt 473 ml) is recommended.
Routine Preventative Maintenance:
•
Check free speed of tool using a tachometer without abrasive accessory attached with 90 PSIG at inlet while tool is running. This governor controlled tool
should be speed checked every 20 hours of use or weekly, whichever occurs more frequently. Always check tool speed after any maintenance or repair.
•
Inspect pad backing for excessive wear, nicks, cracks and cuts at the pad edges. Do not use pads that show excessive wear.
Check pad backing for concentricity.
•
Visually inspect abrasive discs for nicks, cuts, tears at the edges. Abrasive disc with a curved shape indicates improper storage. Do not use abrasives that
show these characteristics.
•
Mineral spirits are recommended when cleaning the tool and parts. Do not clean tool or parts with any solvents or oils containing acids, esters,
ketones, chlorinated hydrocarbons or nitro carbons.
•
DO NOT clean or maintain tools with chemicals that have a low flash point (example: WD-40
®
).
•
A Motor Tune-Up Kit (P/N
96100
) is available which includes high wear and medium wear motor parts.
•
Air tool labels must be kept legible at all times, if not, reorder label(s) and replace. User is responsible for maintaining specification information i.e.:
Model #, S/N, and RPM. (See Assembly Breakdown)
•
Blow air supply hose out prior to initial use.
•
Visually inspect air hoses and fittings for frays, visible damage and signs of deterioration. Replace damaged or worn components.
•
Refer to Dynabrade's Warning/Safety Operating Instructions Tag (Reorder No.
95903
) for safety information.
After maintenance is performed on tool, add a few drops of Dynabrade Air Lube (P/N
95842
) to the air line and start the tool a few times to lubricate air motor.
Check for tool vibration before mounting abrasive wheel accessory.
Handling and Storage:
•
Use of tool rests, hangers and/or balancers is recommended.
•
Protect tool inlet from debris (see Notice below).
•
DO NOT carry tool by air hose. When carrying tool keep hands away from throttle lever to avoid accidental startup.
•
Protect abrasives accessories from exposure to water, solvents, high humidity, freezing temperature and extreme temperature changes.
•
Store abrasive discs prior to use at 40-50% relative humidity and 60-80˚ F (15-27˚ C) to reduce curling.
•
Store accessories in protective racks or compartments to prevent damage.
Notice
All Dynabrade motors use the highest quality parts and metals available and are machined to exacting tolerances. The failure of quality pneumatic motors
can most often be traced to an unclean air supply or the lack of lubrication. Air pressure easily forces dirt or water contained in the air supply into motor
bearings causing early failure. It often scores the cylinder walls and the rotor blades resulting in limited efficiency and power. Our warranty obligation is
contingent upon proper use of our tools and cannot apply to equipment which has been subjected to misuse such as unclean air, wet air or a lack of
lubrication during the use of this tool.
One Year Warranty
Following the reasonable assumption that any inherent defect which might prevail in a product will become apparent to the user within one year from the date
of purchase, all equipment of our manufacture is warranted against defects in workmanship and materials under normal use and service. We shall
repair or replace at our factory, any equipment or part thereof which shall, within one year after delivery to the original purchaser, indicate upon our
examination to have been defective. Our obligation is contingent upon proper use of Dynabrade tools in accordance with factory recommendations,
instructions and safety practices. It shall not apply to equipment which has been subject to misuse, negligence, accident or tampering in any way so as to
affect its normal performance. Normally wearable parts such as bearings, contact wheels, rotor blades, etc., are not covered under this warranty.
3