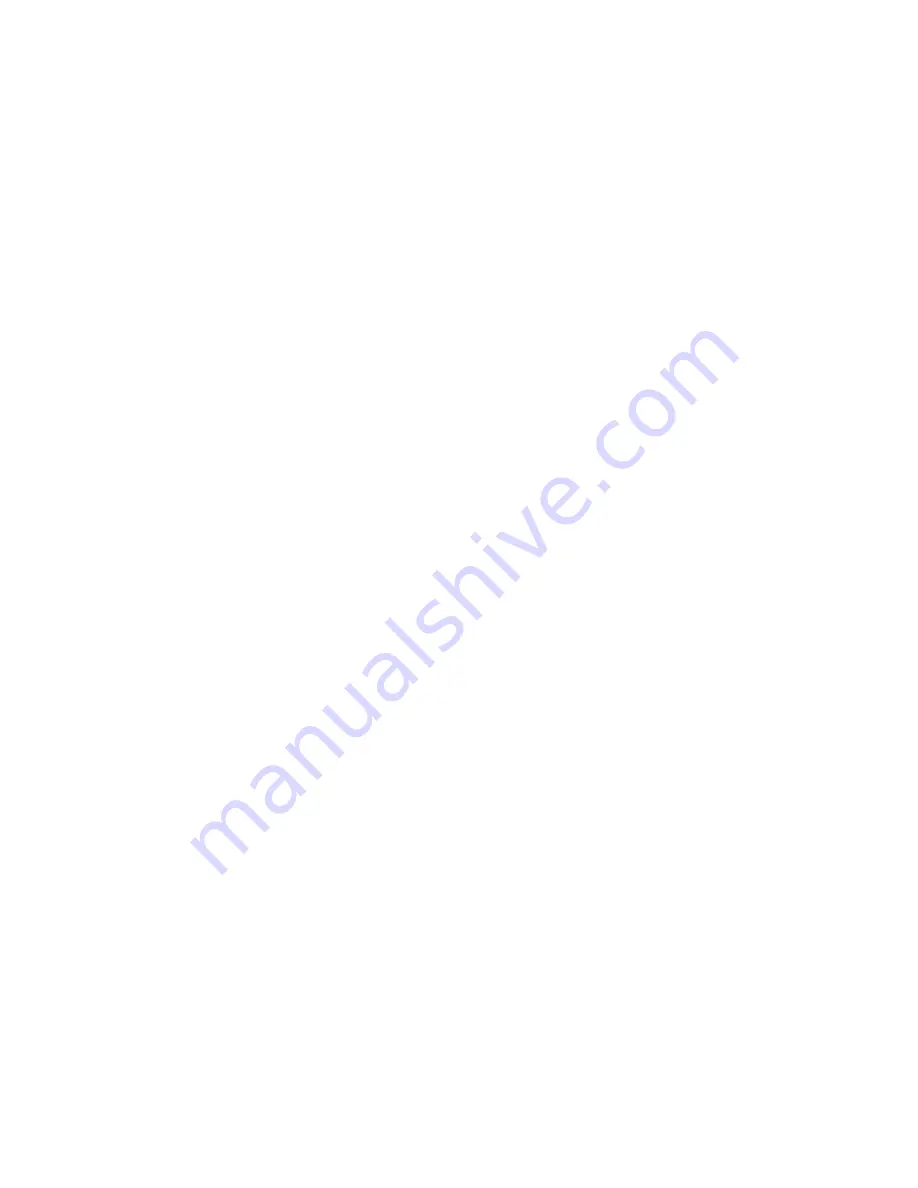
Motor Assembly/Disassembly Instructions – .33 hp Rear Exhaust Tools
Important: Manufacturer’s warranty is void if tool is disassembled before warranty expires.
A Motor Tune-Up Kit (96505) is available which contains high and medium wear parts. Please refer to parts breakdown for part identification.
To Disassemble:
Motor Disassembly:
1.
Invert machine and secure in vice, using
57092
Collar or padded jaws.
2.
Remove the accessory.
3.
Insert
56058
Lock Ring Wrench into corresponding tabs of lock ring and unscrew. Motor may now be lifted out for service.
4.
Using a #2 arbor press remove the
58359
Rear Plate by securing the
54806
Cylinder in a standard 2 inch bearing separator. Push the rotor shaft
through the bearing. Remove the cylinder, rotor, vanes and key.
5.
Remove
54809
Front Bearing Plate and
58368
Front Motor Bearing, using a standard 2 inch bearing separator.
Motor Disassembly Compete.
Valve Body Disassembly:
1.
Position valve body in a vise by using
52296
Repair Collar so that air inlet points up.
2.
Secure
01578
Inlet Adapter with a wrench to prevent it from turning. While holding the inlet adapter stationary remove the air fitting by turning
it counter-clockwise.
Important: 01578
Inlet Adapter must be secured before attempting to remove the air fitting so as to avoid damaging
the valve body housing.
3.
Remove
01578
Inlet Adapter.
4.
Remove
95711
Retaining Ring from inlet adapter.
5.
Remove
01486
Felt Silencer (4), and
01379
Bronze Muffler.
6.
Remove
01564
Air Control Ring from the valve body housing. Use needle nose pliers and remove
01468
Spring,
01472
Tip Valve and
01464
Seal.
7.
Use a 2.5mm drive punch to remove
12132
Pin and
01448
or
01462
Throttle Lever.
8.
Remove
95558
Retaining Ring and push
01469
Regulator from the valve body housing.
Valve Body Disassembly Compete.
To Assemble:
Motor Assembly:
Important: Be certain parts are clean and in good working order before assembling.
1.
Press
58368
Bearing onto the rotor shaft down to the shoulder using
57091
Bearing Press Tool.
2.
Place
54809
Front Bearing Plate onto
58368
Bearing and check for smooth rotation.
3.
Place
56047
Rotor Key into pocket on
54804
Rotor Shaft.
4.
Place
57090
Rotor over
54808
Rotor Shaft making sure to line up slot in
54806
Rotor with
56047
Rotor Key.
Note:
Be certain rotor “floats” easily on
the shaft, because the design of this motor uses a floating rotor. There is no need to set or adjust the gap between the rotor and the end plates.
5.
Place
56073
Vanes in slots on
57090
Rotor.
6.
Place the
54806
Cylinder over the
54808
Rotor. The short line up pin goes toward the
54809
Front Bearing Plate.
7.
Place
58359
Rear Bearing Plate and
58368
Bearing over shaft and long end of line up pin and press into place.
8.
Make certain threaded end of
54808
Rotor Shaft spins freely.
Motor Assembly Compete.
Valve Body Assembly:
1.
Install
01469
Regulator complete with o-rings and valve stem into valve body housing. Secure it in place with
95558
Retaining Ring.
2.
Place valve body housing in a vise, holding it with the aid of
52296
Repair Collar so that the air inlet opening points up.
3.
Insert
01464
Seal into the air inlet opening so that it lays flat.
4.
Line up hole in valve stem with inlet opening in housing (looking past brass bushing). Install
01472
Tip Valve so that the metal pin passes through the
hole in the valve stem. Install
01468
Spring (small end against tip valve).
5.
Position
01564
Air Control Ring around inlet opening.
6.
Place
01379
Bronze Muffler inside
01446
Air Deflector.
7.
With
95620
Retaining Ring installed on female threaded end of
01578
Inlet Adapter insert the inlet adapter through
01446
Air Deflector.
8.
Place
01486
Felt Silencer (4) inside
01446
Air Deflector.
9.
Install
95711
Retaining Ring into groove at the male threaded end of the inlet adapter. Install
96065
O-Ring into groove on the air defector.
10.
Apply Loctite #567 (or equivalent) to the male threads of the
01578
Inlet Adapter and install muffler assembly onto valve body housing
(torque to 23 N•m/200 in.-lbs.).
11.
Install
01448
or
01462
Throttle Lever onto valve body housing with
12132
Pin.
12.
Secure
01578
Inlet Adapter with a wrench to prevent it from turning.
Important: 01578
Inlet Adapter must be secured before
attempting to install the air fitting so as to avoid damaging the valve body housing.
Tool Assembly Complete. Please allow 30 minutes for adhesives to cure before operating tool.
Important:
Motor should now be tested for proper operation at 90 PSIG. If motor does not operate properly or operates at a higher RPM than marked on the
tool, the tool should be serviced to correct the cause before use. Before operating, place 2-3 drops of Dynabrade Air Lube (P/N
95842
) directly into air inlet
with throttle lever depressed. Operate tool for 30 seconds to determine if tool is operating properly and to allow lubricating oils to properly penetrate motor
Loctite
®
is a registered trademark of Loctite Corp.
3