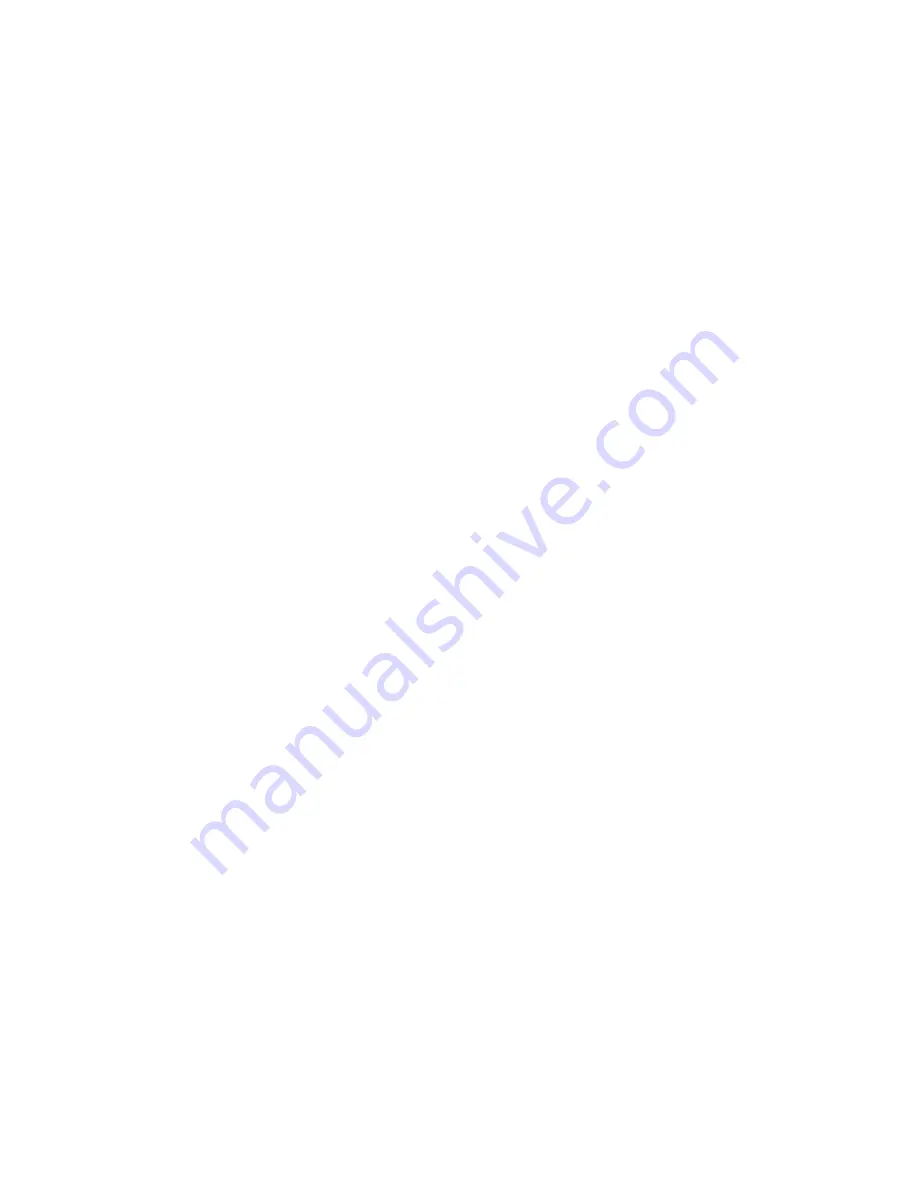
Motor Disassembly/Assembly Instructions
Important: Manufacturers warranty is void if tool is disassembled before warranty expires.
A complete Tune-Up Kit, part number 96122, is available which includes assorted parts to help maintain and repair motor. These instructions are for use
in conjunction with Part Number 57325 Repair Kit, which includes special tools for proper disassembly/assembly of tool.
To Disassemble:
1. Disconnect tool from power source. Invert machine and secure in soft jaw vise, or use 57092 Collar (supplied in 57325 Repair Kit).
2. Remove sanding pad with 3 mm hex wrench. (Supplied in 57325 Repair Kit)
3. Remove 54628 Counterbalance:
a.)
Loosen 95887 Screw with 2 mm hex wrench.
b.)
Remove 95898 Screw with 5 mm hex wrench.
Note: 54628 Counter Balance must be held stationary while removing 95898 Screw.
c.)
Remove counterbalance.
4. Pull out mounting plate sub-assembly.
5. Disassemble mounting plate sub-assembly:
a.)
Remove 01678 (3) Screws from underside of mounting plate with a 3 mm hex wrench.
b.)
Press out 56133 Bearing from mounting plate by using 57091 Bearing Press Tool (supplied in 57325 Repair Kit).
6. Insert 56058 Lock Ring Wrench (supplied in 57325 Repair Kit) into corresponding tabs of lock ring and unscrew. Motor may now be lifted out for service.
7. Remove 95626 Retaining Ring. Upper motor may now be disassembled.
8. The 54629 Rear Bearing Plate contains a “press fit” bearing. Remove the rear plate assembly by securing the 54631 Cylinder in a standard 2 inch
bearing separator or use a standard bearing puller gripped on the cylinder inlet and exhaust area. Push the 54672 Motor Shaft through the bearing.
9. Remove cylinder, rotor, blades and key.
10. Remove 54630 Front Plate and 02695 Front Motor Bearing, using (#2) arbor press. Support inside edge of the bearing cavity wall on the front
plate while pressing on the small end of the 54672 Motor Shaft.
11. Remove 01206 Bearing from rear bearing plate with utility press pin.
12. Press 02695 Bearing from 54672 Motor Shaft.
To Reassemble:
Important: Be certain parts are clean and in good repair before reassembling.
1. Press 02695 Bearing onto 54672 Motor Shaft down to shoulder.
2. Assemble 54630 Front Bearing Plate onto shaft and press plate on outer race of 02695 Bearing.
3. Place rotor key, rotor, and blades onto shaft. Note: Be certain rotor “floats” easily on the shaft. Because the design of this motor uses a “floating rotor”,
there is no need to set or adjust gap between the rotor and end plates.
4. Place 54631 Cylinder over rotor. The “short” line-up pin goes toward the front plate.
5. Place rear bearing plate (with 01206 Rear Bearing pressed into place) over shaft and “long” end of line-up pin and press fit in place.
6. Install 95626 Retaining Ring, concave side toward motor. Note: Be certain retaining ring is completely pressed down into its groove on the shaft.
7
Grease the rubber seals inside the housing using a small amount if multi-purpose grease or petroleum jelly.
Note: Be certain that rubber seals in housing have not pulled out of their seat during disassembly. If this has happened re-seat the seals by pushing
them until they are flush with inside diameter.
8. Secure motor housing in vise using soft jaws or 57092 Collar (Supplied in 57325 Repair Kit). Slide motor assembly into secured housing.
Note: With handle pointing toward you be certain that the line-up pin enters slot to the right of center.
9. Apply a bead of #271 Loctite
®
(or equivalent) onto outer edge of 56046 Lock Ring and tighten with 56058 Lock Ring Wrench to (34 N•m /300 in. – lbs.).
10. Mounting plate sub-assembly:
a.)
Apply #609 Loctite to the inner bore of 54627 Mount plate.
b.)
Press 56133 Bearing into, 54685 Bearing Retainer.
c.)
Apply one drop of #271 Loctite to (3) 01678 Screws. Drop Screws thru holes in 54627 Mount Plate. Using them to line-up with threaded holes in
54658 Bearing Retainer.
d.)
Press 54627 Mount Plate down onto 56133 Bearing and 54685 Bearing Retainer.
e.)
Screw (3) 01678 Screws into 54685 Bearing Retainer. (Torque screws to 2.82 N•m/25 in. – lbs.)
11. Install mount plate sub-assembly onto 54672 Shaft.
12. Install 54628 Counter Balance onto 54672 Shaft, (matching profile of 54672 Shaft with profile on 54628 Counter Balance).
13. Apply one drop of #242 Loctite (or equivalent) to threads of 95898 Screw, and install screw by using a 5 mm hex key. (Torque screw to 9 N•m/80 in. –
lbs.) Note: 54898 Counter Balance must be held stationary while installing 95898 Screw.
14. Apply a small amount of #271 Loctite (or equivalent) to threads of 95887 Set Screw and place with a 2 mm hex key.
15. Attach sanding back-up pad to the mount plate with (5) 95886 Washers and (5) 97010 Screws. (Torque screws to 3.38 N•m/30 in. – lbs.)
Installation is Complete.
To Disassemble Valve And Speed Regulator Assemblies:
1. Invert tool and place in soft jaw vise or use 57092 Repair Collar.
2. Loosen and remove 97010 Screws (2) and 01211 Lock Washers (2) from 56672 Adapter.
3. Carefully remove 56672 adapter making sure no parts fall to the ground. On non-vacuum models, pry off 54194 Muffler Cap and remove 54195 Muffler (3).
4. Remove 57343 Speed Regulator by detaching 98597 Retaining Ring with a pair of snap ring pliers. Remove 01024 O-Rings with a small screwdriver.
5. Remove tip valve assembly from housing.
3
(Continued on page 4)
Buy parts on line at https://Dynashop.co.uk/ for all things Dynabrade
Buy parts on line at https://Dynashop.co.uk/ for all things Dynabrade