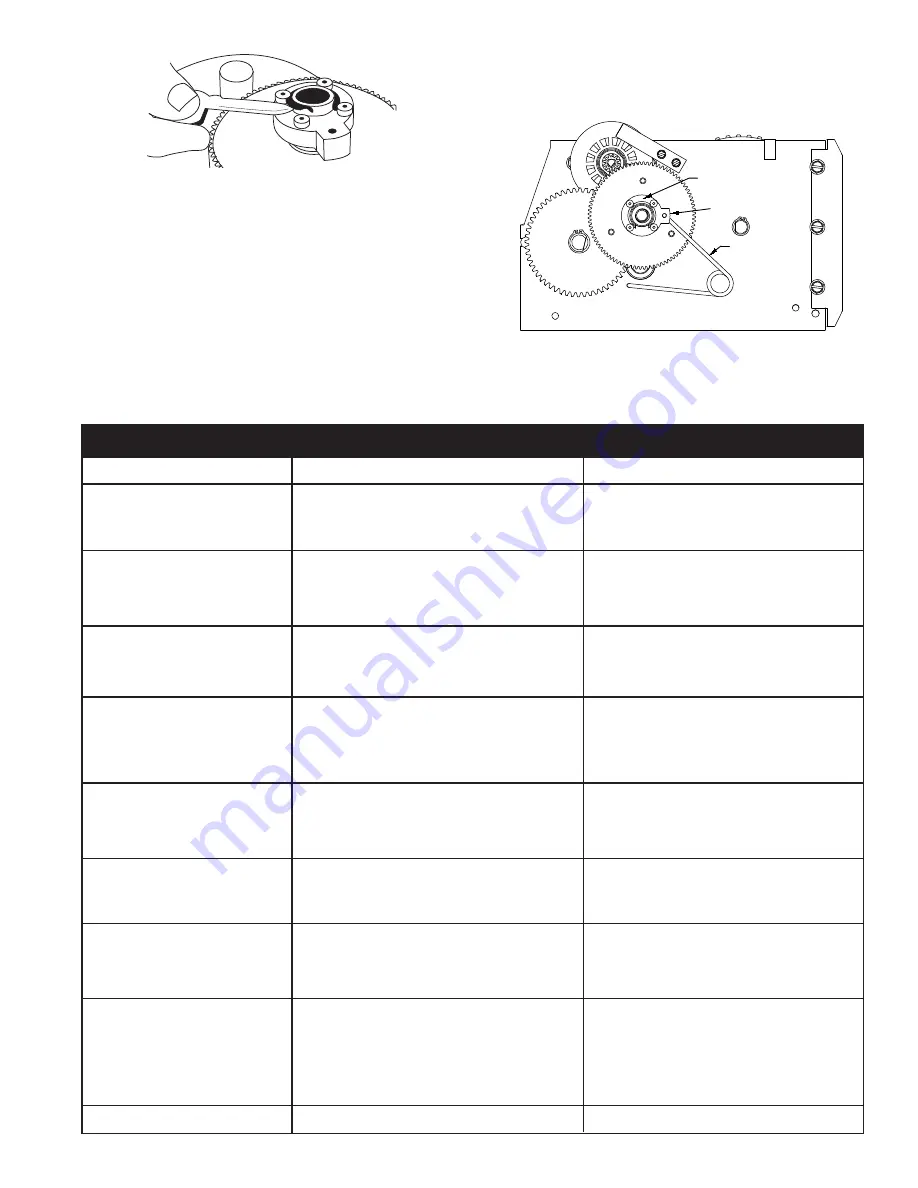
sYMptoM
possible cause(s)
corrective action
Safety hook spreads
1. Point loading of hook
1. Replace hook
2. Load exceeds rated capacity of unit
2. Lighten load, reduce %
of incline or reduce load friction
Cable breaks
1. Cable damage due to miswrap.
1. Keep tension on cable at all times
2. overloading
2. Reduce load
Cable miswrap
Loose cable being wound onto drum
Keep tension on cable at all times
and/or crushing
Load creeps when power is oFF
1. Brake/clutch out of adjustment
1. adjust (see Maintenance).
2. Roller clutch, not engaging
2. Replace.
3. overloading
3. Reduce load.
4. Brake slipping
4. Replace
Winch motor runs but fails
1. Clutch is slipping.
1. Check clutch lining for grease or oil. See
to wind cable
“Maintenance” for clutch adjustment procedure.
2. Gear train is damaged.
2. Check and Repair
Winch motor runs hot
In operation too long
Let motor cool for at least 20 minutes. (See Winch
Rating Section.)
Winch motor fails to run
Electrical
Check the following: power supply, wiring, control
switch, male/female connections and motor.
Cable will not pull out (free wheel)
1. Sticking cable
1. avoid cable miswrap.
2. Sticking clutch
2.a. “Jog” power switch with clutch in free wheel
(No load only).
b. disassemble, clean & readjust clutch, see
“Maintenance”.
Smokes
Normal on initial power down use
None
troubleshooting chart
tighten the clutch mechanism) the spring lug on
the spring keeper should come to rest at
approximately the 3:00 o’clock position.(See
FIG. 7)
5. Check the pulley block and hook assembly
(ModELS Sa7000aC aNd Sa12000aC) to be
sure that the pulley rotates freely on the bronze
pulley spacer. occasional greasing of these two
items is recommended.
FIG. 6
FIG. 7
o-ring illustration
clutch spring illustration
5
Clutch Spring
Keeper
Spring Lug
Clutch Spring