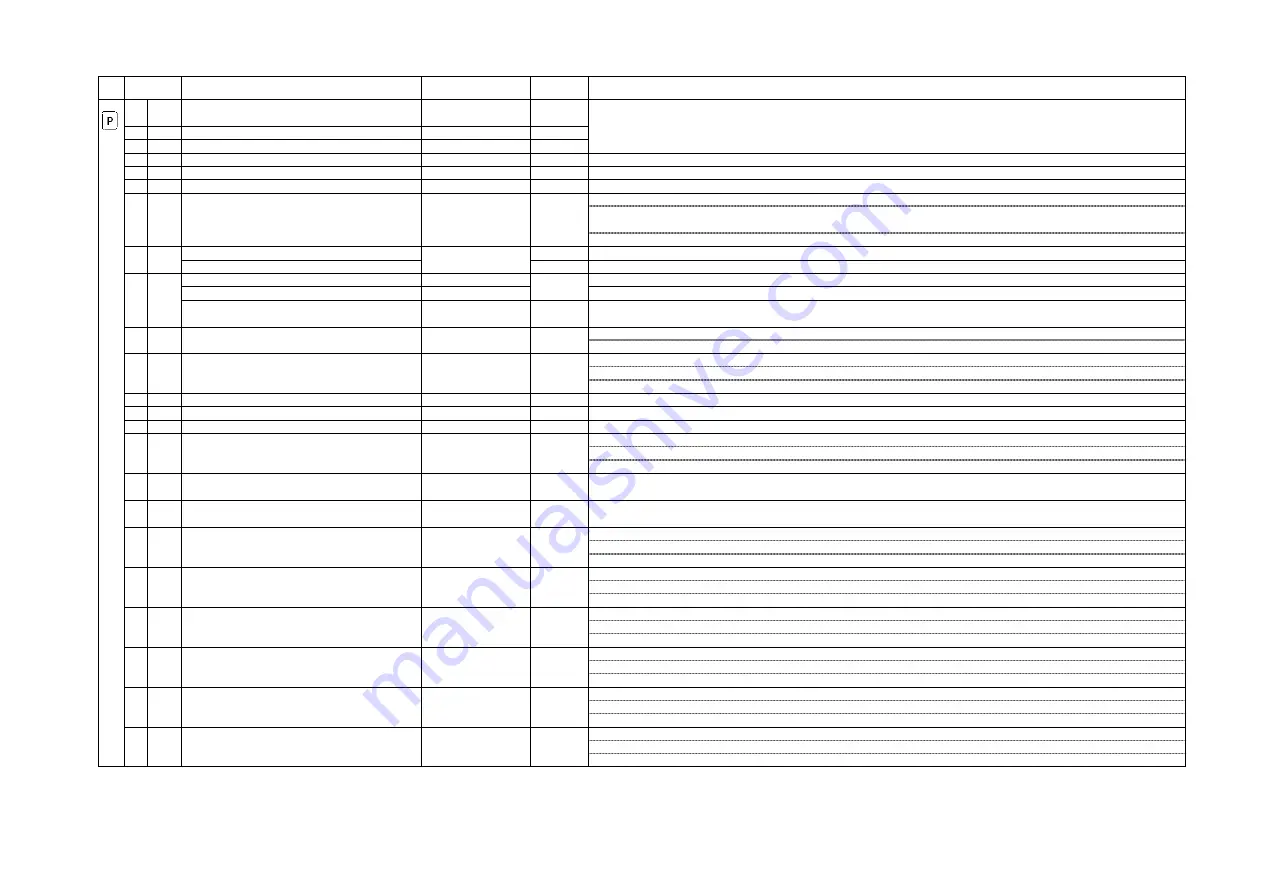
PAGE - 6
Key
Parameters Function
Range
Pre.setting
Description
HVP -20 Parameters List for DA-251 (MAC. 35)
Parameters
Code
89
D1
Delayed timing prior to upper trimmer engaged
at down-stop
0 - 990 ms
30
90
D2
Setting timing of upper trimming at down-stop
0 - 2500 ms
90
91
D3
Timing recall of upper trimming at down-stop
0 - 990 ms
120
92
W1
Delayed timing prior to wiper engaged
0 - 980 ms
0
Time setting between needle up to wiper active.
93
W2
Setting timing of wiping
0 - 9990 ms
40
Wiper ON timer setting.
94
WF
Delayed timing prior to foot lifter engaged
0 - 990 ms
50
Timer setting between wiper OFF to presses foot ON.
Condense-Stitch function by
【
027. CT
】
timer for needle up & motor stop.
ON
:
Enable. Note :
【
021. EBT
】
=ON,
【
022. EBC
】
=8,
【
023.EBD
】
=3 and
【
024.EBN
】
=2 and
【
027. CT
】
=100
must be adjusted.
OFF
:
Disable.
WEDA cutter delay stitch count
10
WEDA cutter delay stitch count setting.
Setting stitches of Condense-Stitch sewing
8
Valid only when the [095. CSF] = ON.
Tape cutter on timer
0 - 2500 ms
Tape cutter on timer setting x10 = 100 ms.
Bobbin counter alarm preaction value
0 - 250 stitches
When
【
042.CUD
】
= US,DS the value is bobbin counter alarm preaction value.
Setting stitches prior to stop beyong Condense-
Stitch
0 - 250 stitches
0
Valid only when the [095. CSF] = ON.
ON
:
Normal stitch length.
OFF
:
Long stitch length.
Edge sensor function selection..
ON
:
Enable.
OFF
:
Disable.
100
SRS Edge sensor signal check 1
0 - 99 stitches
1
Only valid when
【
099. SEN
】
set at ON. To avoid photo interference.
101
CMS Edge sensor signal check 2
0 - 99 stitches
3
Only valid when
【
099. SEN
】
set at ON. To avoid photo interference.
102
SE
Setting stitches from edge sensing to stop
1 - 999 stitches
6
Setting Stitches to stop., when edge signal detected. Only valid when
【
099. SEN
】
set at ON
When edge signal detected out. Motor will do the trimming cycle automatically.
ON : After the stitches of
【
102. SE
】
finished, trimming works.
OFF : After the stitches of
【
102. SE
】
finished, trimming doesn't work.
104
PSU Stitches for emergency up-stop
1 - 99 stitches
6
When
【
PSU
】
signal detected, running the stitches then stop at UP position.
The speed of setting stitches is set by
【
009. A
】
.
105
PSD Stitches for emergency down-stop
1 - 99 stitches
6
When
【
PSD
】
signal detected, running the stitches then stop at DOWN position.
The speed of setting stitches is set by
【
009. A
】
.
When the pedal on and the edge signal detected, the motor can start running.
ON
:
Enable.
OFF
:
Disable.
When motor running, manually push the Touch Back switch , reverse solenoid engaged on at needle up.
ON
:
Valid.
OFF
:
Invalid.
When motor running, manually push the Touch Back switch , reverse solenoid engaged on at needle down.
ON
:
Valid.
OFF
:
Invalid.
During sewing, reverse output will be OFF at needle UP or DOWN position .
ON
:
At
『
needle UP
』
position.
OFF
:
At
『
needle DOWN
』
position.
The trimming and reverse solenoid activated on the same time.
ON
:
Valid.
OFF
:
Invalid.
Correction mode selection for Touch-Back Switch. Note :
【
010. ACD
】
= OFF and
【
011. RVM
】
= B
1: Doing correction with one touch the Touch-Back switch .
2: Doing correction with double touch the Touch-Back switch.
P
O
W
E
R
..
O
N
0 - 99 stitches
97
TK3
Only valid when
【
078. TRM
】
set at
『
KB
』
mode.
Signal output from the wiper MW.
See the KB timing chart.
ON/OFF
OFF
95
CSF
Condense-Stitch function selection
ON/OFF
ON/OFF
OFF
10
96
ON/OFF
OFF
103
SET
Trimming mode at sensory stop
ON/OFF
OFF
99
SEN Edge sensor function selection
ON/OFF
ON
107
S7U
Manual Back-Tacking engaged at
needle-up position
ON/OFF
OFF
106
PSN Re-start function at emergency stop
ON/OFF
ON
109
ROF Mode for de-engaging Back-Tacking
ON/OFF
OFF
108
S7D
Manual Back-Tacking engaged at
needle-down position
OFF
111
COR Correction Mode of Touch-Back Switch
1/2
2
110
TB
Mode for Back-Tacking at trimming cycle
98
SLU
WN3
Stitch length selection for backtack
+
From
the
library
of:
Diamond
Needle
Corp