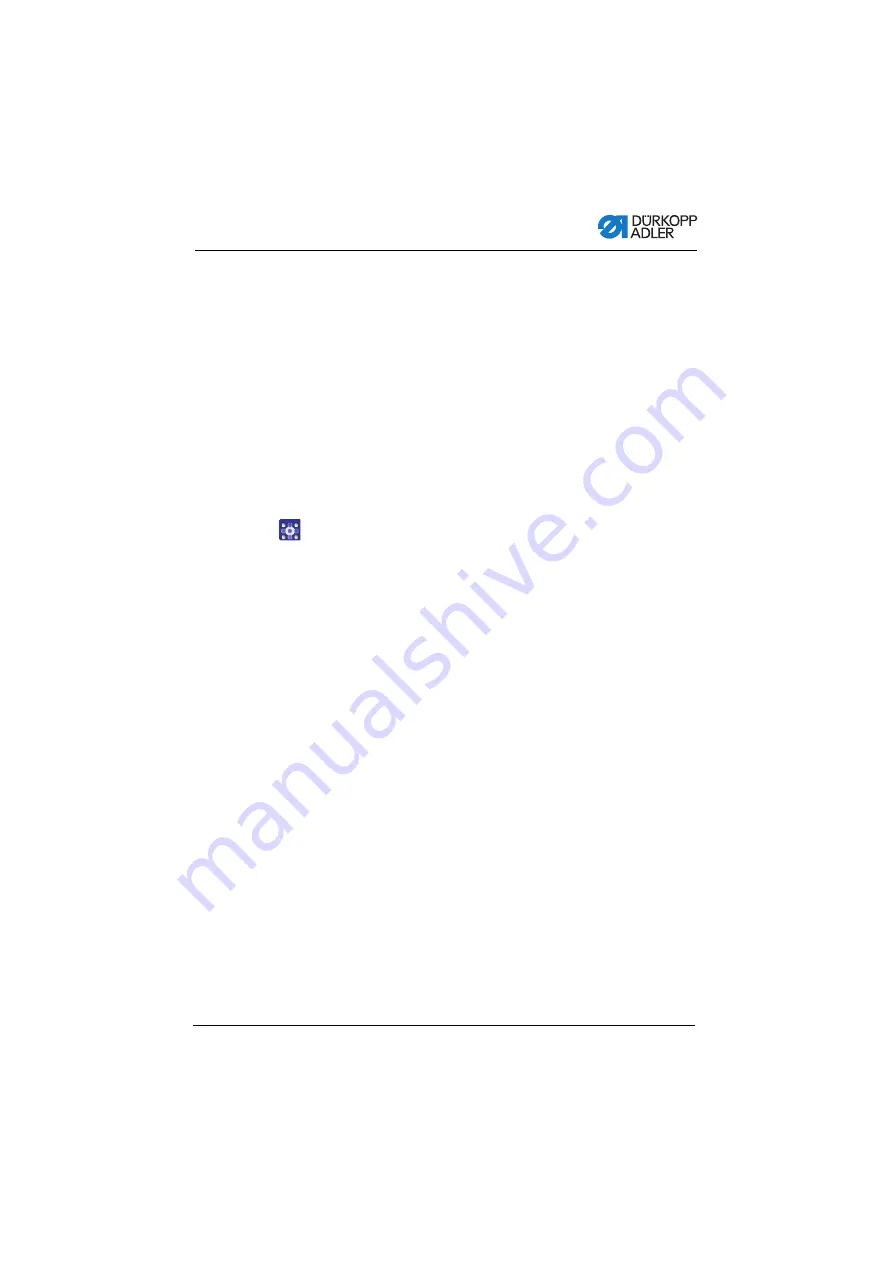
Programming
Operating Instructions 512/532 - 05.0 - 04/2018
43
5.
Press the
Reset
button to return a changed value to the ori-
ginal value.
6.
Press the
Ready
button to save a change.
The button LED goes out.
7.
Press the
Memory
button.
The button LED goes out.
4.19.2 Editing parameters at the M2 level
Prerequisite:
• Machine is in programming mode,
Ready
button LED is off.
To edit parameters at the M2 level:
1.
Press and hold the
Memory
button for 6 s.
The controller beeps twice, the button LED lights up.
The
Program
display shows the parameter number, the
Function
display shows the parameter value.
2.
Press the
+/– Program
buttons to select a different parameter.
3.
Press the
Ready
button to confirm the parameter.
The button LED illuminates.
4.
Press the
+/– Function
buttons to change values.
5.
Press the
Reset
button to return a changed value to the ori-
ginal value.
6.
Press the
Ready
button to save a change.
The button LED goes out.
7.
Press the
Memory
button.
The button LED goes out.
Содержание 512/532
Страница 1: ...Operating Instructions 512 532 ...
Страница 6: ...Table of Contents 4 Operating Instructions 512 532 05 0 04 2018 ...
Страница 16: ...Safety 14 Operating Instructions 512 532 05 0 04 2018 ...
Страница 60: ...Programming 58 Operating Instructions 512 532 05 0 04 2018 ...
Страница 70: ...Maintenance 68 Operating Instructions 512 532 05 0 04 2018 ...
Страница 86: ...Decommissioning 84 Operating Instructions 512 532 05 0 04 2018 ...
Страница 88: ...Disposal 86 Operating Instructions 512 532 05 0 04 2018 ...
Страница 97: ...Appendix Operating Instructions 512 532 05 0 04 2018 95 11 Appendix ...
Страница 98: ...Appendix 96 Operating Instructions 512 532 05 0 04 2018 ...
Страница 99: ......