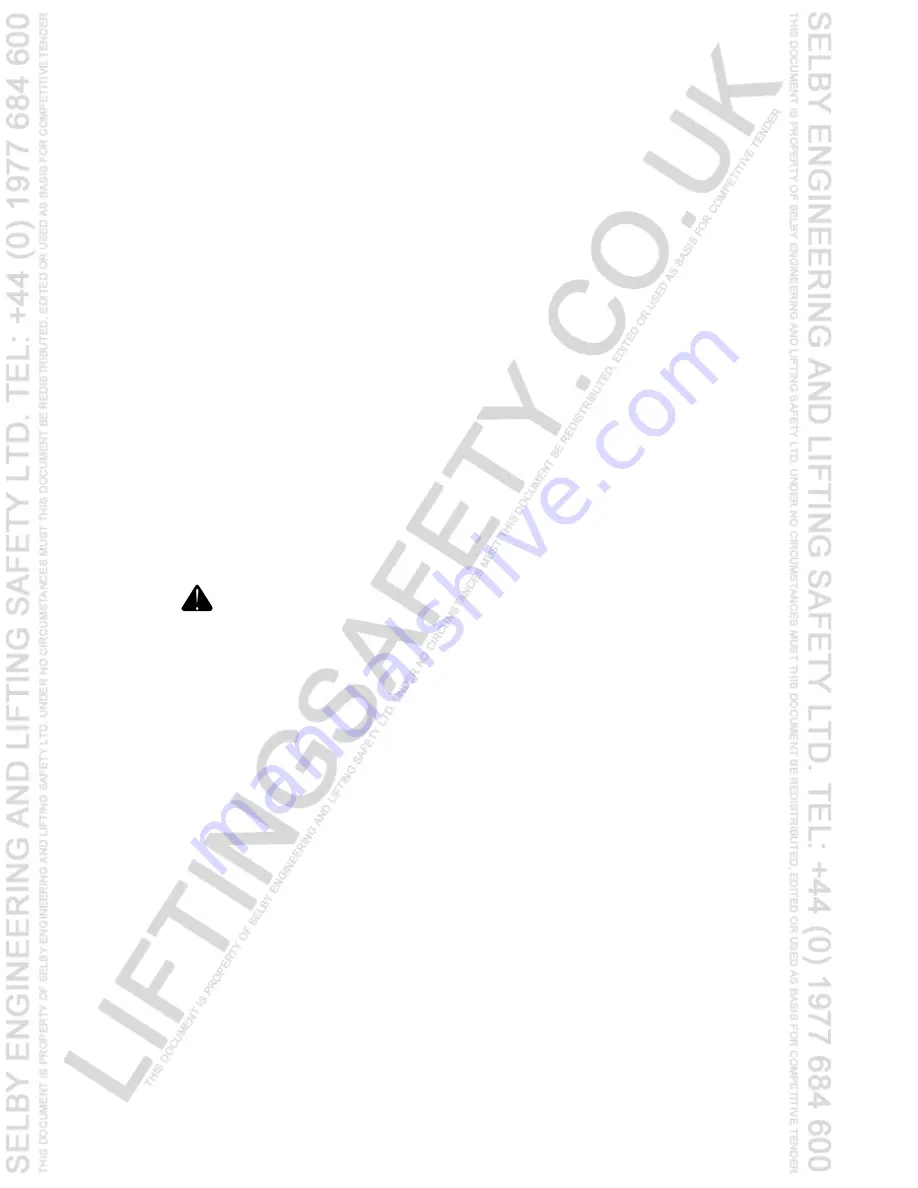
6
1-5. Important Precautions
In order to ensure that actuators provide good
service over a period of years, the following precau-
tions should be taken:
1. Select an actuator that has a rated capacity
greater than the maximum load that may be
imposed on it.
2. The structure on which the actuators are
mounted should have ample strength to carry
the maximum load, and should be rigid enough
to prevent undue deflection or distortion of the
actuator supporting members.
3. It is essential that the actuators be carefully
aligned during installation so that the lifting
screws are perfectly plumb and the connecting
shafts are exactly in line with the worm shafts.
After the actuators, shafting, gear boxes, etc.,
are coupled together, it should be possible to
turn the main drive shaft by hand. If there are no
signs of binding or misalignment, the actuator
system is then ready for normal operation.
4. The actuators should have a greater raise than
is needed in the actual installation. Should it be
necessary to operate the actuators to the ex-
treme limits of travel, it should be done cau-
tiously.
Caution
Do not allow actuator lifting nut travel to go
beyond catalog closed height (A) of actuator
or serious damage to lifting nut or the inter-
nal actuator mechanism may result. Refer to
table of specifications (par. 1-3) for closed
height (A) of respective units.
5. The worm shaft speed for these actuators
should not exceed 900 RPM for heavy loads, or
1800 RPM for light loads of one-fourth (or less)
of the actuator capacity.
6. The lifting screw should not be permitted to
accumulate dust and grit on the threads. If
possible, screws should be protected by some
means such as a boot.
7. The ball screw and lifting nut should be checked
periodically for excessive backlash and spalling
of race ways.
8. The lubrication procedures for normal and
severe service conditions, as described in
Section II, paragraph 2-1, should be closely
followed.
9. Due to high efficiency of Ball Screw actuators, a
brake must be used in conjunction with the
motor selected for actuator positioning (refer to
current catalog for brake selection data).
1-6. Warranty and Warranty Repair
Subject to the conditions stated herein, Duff-
Norton will repair or replace, without charge, any
parts proven to Duff-Norton’s satisfaction to have
been defective in material or workmanship. Claims
must be made within one year after date of ship-
ment. Duff-Norton will not repair or replace any
parts that become inoperative because of improper
maintenance, eccentric loading, overloading, chemi-
cal or abrasive action excessive heat, or other
abuse
Equipment and accessories not of Duff-Norton’s
manufacture are warranted only to the extent that
they are warranted by the manufacturer, and only if
the claimed defect arose during normal use, appli-
cations and service. Equipment which has been
altered or modified by anyone without Duff-Norton’s
authorization is not warranted by Duff-Norton.
EXCEPT AS STATED HEREIN, DUFF-NORTON
MAKES NO OTHER WARRANTIES, EXPRESS OR
IMPLIED, INCLUDING WARRANTIES OF MER-
CHANTABILITY AND FITNESS FOR A PARTICU-
LAR PURPOSE.
If you have any questions concerning warranty
repair, the Duff-Norton Company.
Authorization for return must be received from
the Duff-Norton Company before returning any
equipment for inspection or warranty repair.
Содержание ADM9821
Страница 13: ...13 A Figure 3 1 Exploded Illustration 2800 and 9800 Series Ball Screw Actuators...
Страница 14: ...14...
Страница 15: ...15...