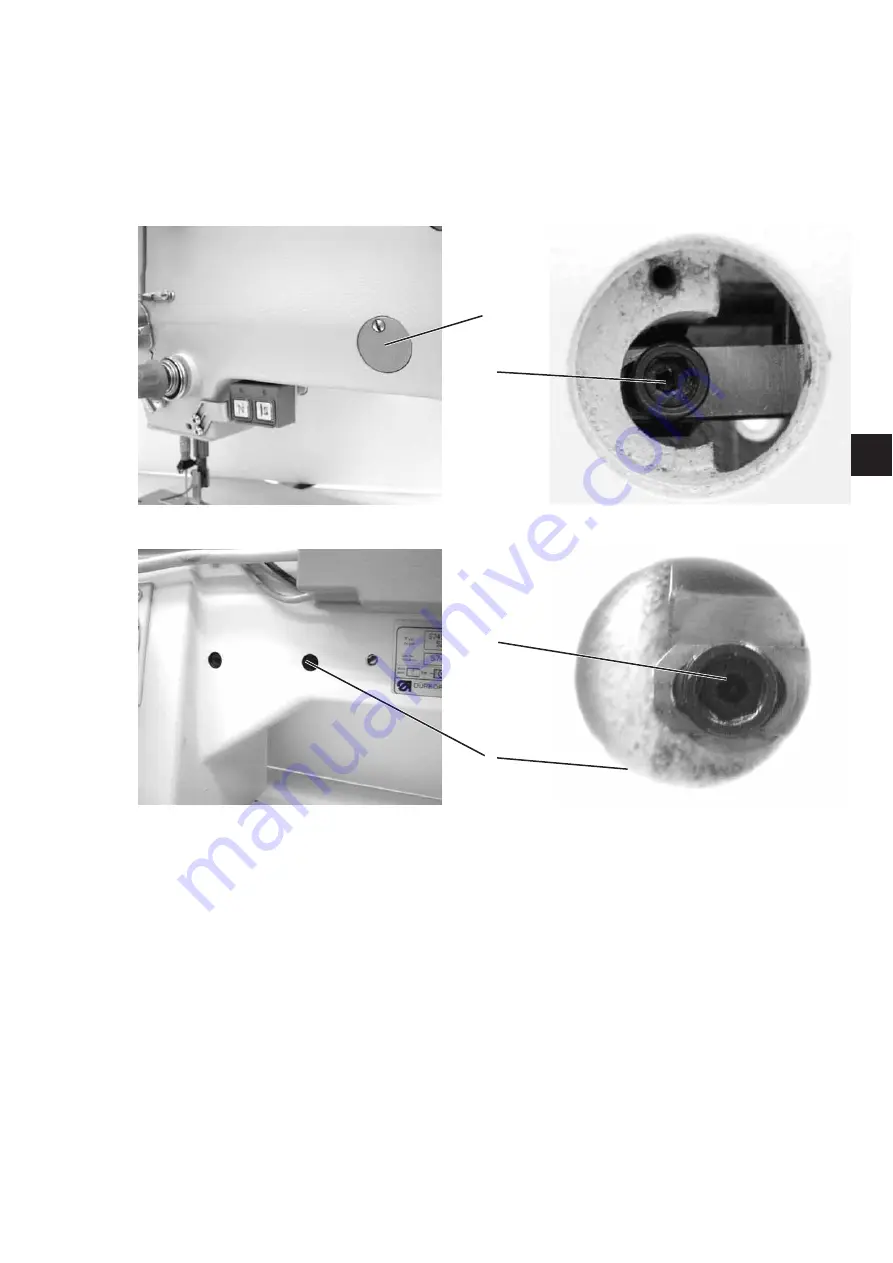
1.6
Lateral setting of needle stab position
Regulation
Both dead centers of the needle lateral motion at the zigzag stitch
sewing should be at the same distance from the throat plate needle
hole edges.
–
Dismantle the cover (1) and the hole stop (2) from the rear side.
–
Loosen both screws (3).
–
Set the maximum zigzag stitch width and adjust the positions of the
needle lateral motion dead centers as per regulation.
–
Tighten both screws properly (3).
9
G
B
1
3
3
2