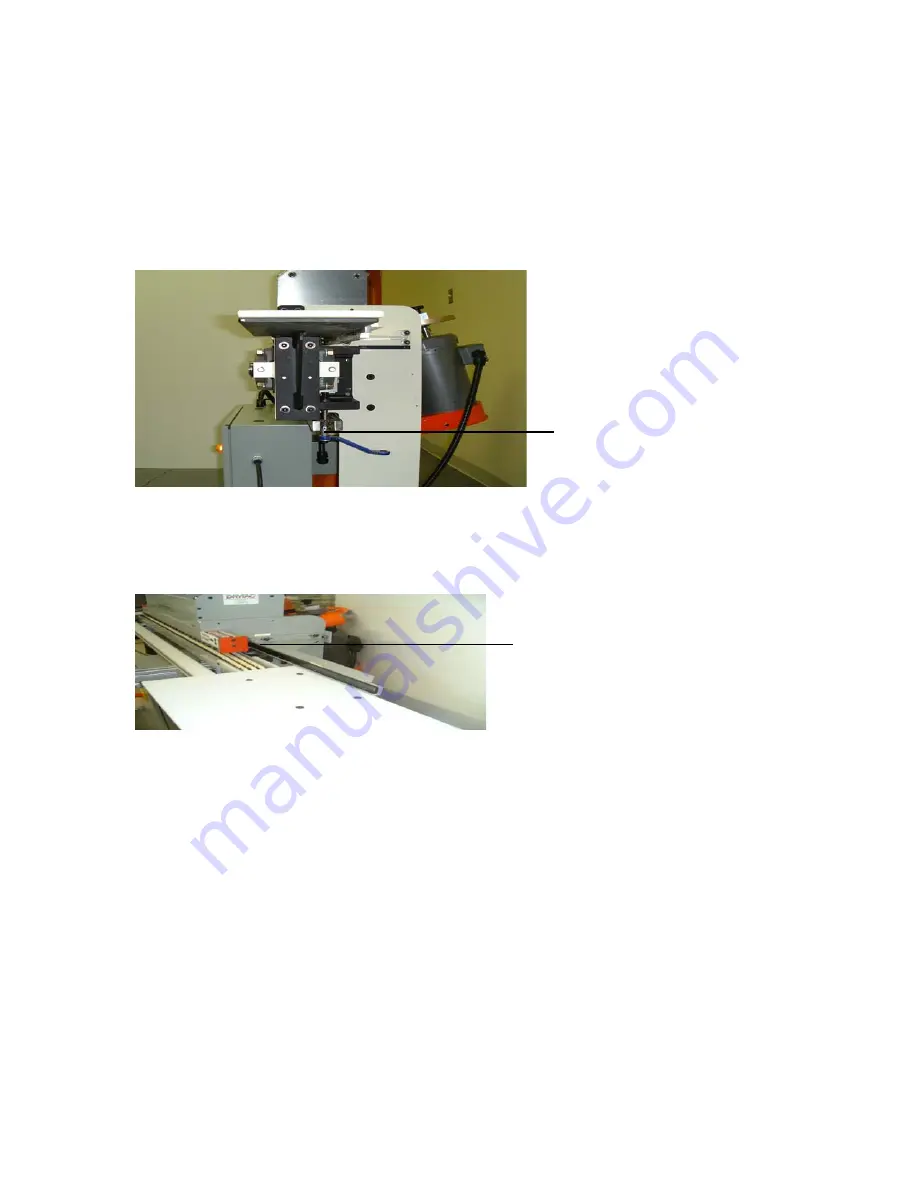
19
2. Ensure that your plaque is fully against the black in-feed guide.
3. Using the ratchet to adjust the conveyor system height, bring the conveyor up to
put pressure on the plaque.
(ratchet )
4. The top of the plaque must be flat and even with the top edge of the adjustable
plate of the in-feed guide.
(Top edge of black guide)
5. Turn your vacuum (Dust Collector) system on.
6. Turn the “Feed” knob to “JOG” mode.
7. Press the green “Shaper On” switch.
8. Press the blue “Feed” button, until plaque is pulled in.
9. Allow the plaque to travel, through shaper, for approximately 3” (8 cm.). Re-
lease the “Feed” Button.
10. Turn Shaper off.
11. Wait until shaper stops completely.
12. Lower the conveyer and remove plaque.
13. Measure how much the plaque is being shaved and make adjustments accord-
ingly.
Содержание DES-1
Страница 1: ...1 DES 1 DES 1E MANUAL www drytac com ...