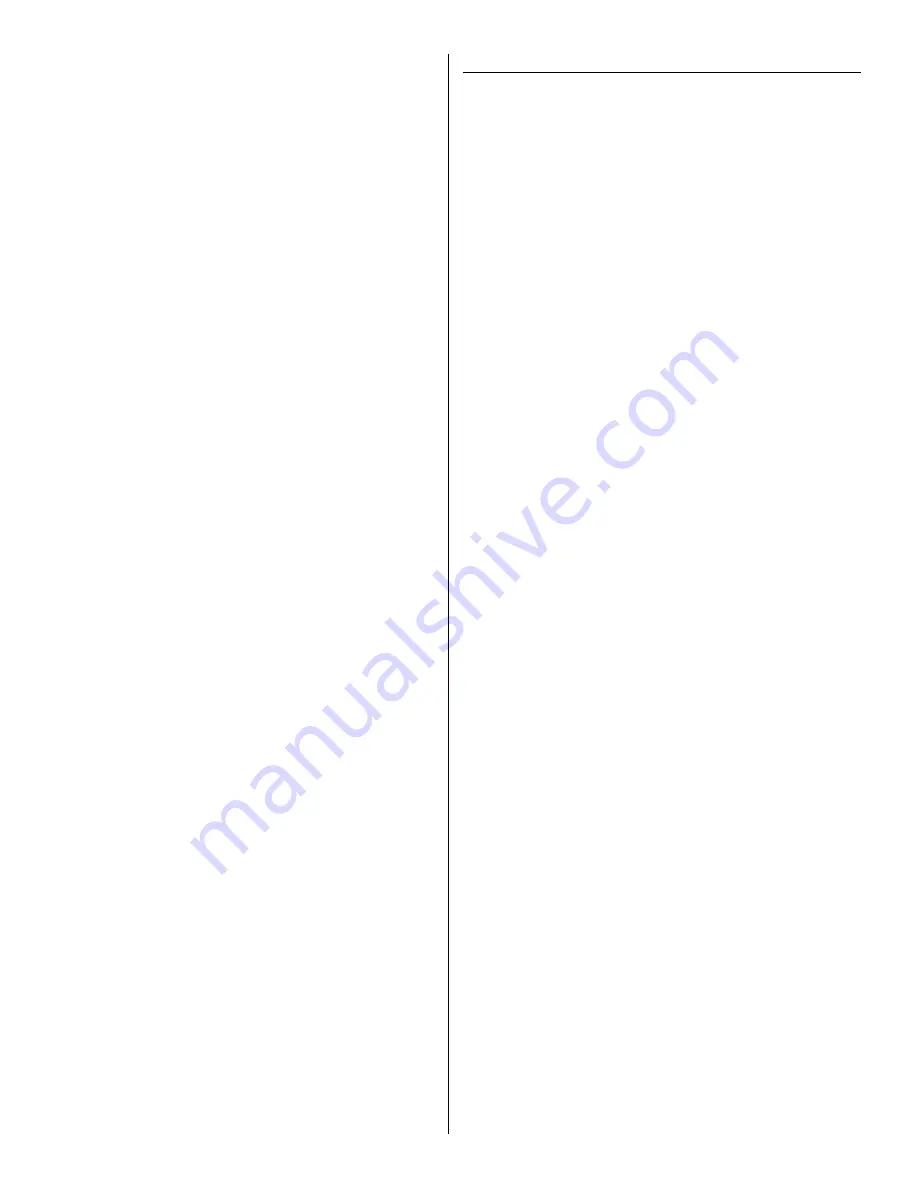
1
US DEPARTMENT OF LABOR
Form Approved Occupational Safety and Health
Administration
OMB No. 44-R1367
MATERIAL SAFETY DATA SHEET
Required under USDL Safety and Health Regulations for Ship Repairing, Shipbuilding and Shipbreaking
(29 CFR 1915, 1916, 1917)
SECTION I
MANUFACTURES NAME:Professional Tool Manufacturing LLC
EMERGENCY PHONE NO: (541) 552-1301
ADDRESS: 210 East Hersey Street, Ashland, Oregon 97520
CHEMICAL NAME & SYNONYMS: Diazon-Electroplated Diamond/CBN Products, Diamond (uncoated),
Man-Made * Diamond, RVG, MBG, MBS Product Families, Standard Series and 300 Series Diamond
Micron Powder
TRADE NAME & SYNONYMS: Electroplated CBN Wheels, Electroplated Diamond Wheels
CHEMICAL FAMILY: Abrasive/Any Grade
FORMULA: N/A
SECTION II - COMPOSITION
CHEMICAL NAME:
Nickel
Industrial Diamond
REGULATED:*
Yes
No
CAS#:
7440-02-0
7882-40-3
AGIH / TLV:
1.0 mg/m3
10.0 mg/m3 (PNOC)
CARCINOGEN:
Yes
No
*Materials are regulated by OSHA 29 CFR 1910,1200, Hazard Communication Standard.
SECTION III - PHYSICAL AND CHEMICAL DATA
BOILING POINT (F)
n/a
MELTING POINT
n/a
SPECIFIC GRAVITY
n/a
VAPOR PRESSURE
n/a
VAPOR DENSITY
n/a
EVAPORATION RATE
n/a
SOLUBILITY IN WATER
n/a
SOLUBILITY IN ALCOHOL
n/a
SOLUBILITY IN OTHER SOLVENT
n/a
PERCENT VOLATILE BY VOLUME (%)
n/a
APPEARANCE AND ODOR: Solid, Clear, White To Yellow To Dark Crystals Silver Color.
SECTION IV - FIRE AND EXPLOSION HAZARD DATA
FLASH POINT
n/a
(METHOD USED)
FLAMMABLE LIMITS
LEL
UEL
EXTINGUISHING MEDIA:
n/a
SPECIAL FIRE FIGHTING PROCEDURES:
n/a
UNUSUAL FIRE AND EXPLOSION HAZARDS:
n/a
SECTION V - HEALTH, FIRST AID AND MEDICAL DATA
PRIMARY ROUTE(S) OF ENTRY:
Inhalation, Ingestion, Skin, Eye(s)
EFFECTS OF OVEREXPOSURE:
INHALATION: Difficulty in breathing (Dust from wheel use).
INGESTION: If dust, symptoms are variable.
SKIN: Irritation (especially if sensitive to Ni).
EYE(S): Irritation (from Ni or diamond particle).
FIRST AID AND MEDICAL INFORMATION:
INHALATION: Move to fresh air. Give oxygen if necessary.
INGESTION: Obtain medical attention.
SKIN: Wash thoroughly with water. Obtain medical help if necessary.
EYE(S): Flush thoroughly with water. Obtain medical assistance.
OTHER POTENTIAL HEALTH RISKS:
Nickel (Ni) is listed as a carcinogen. Avoid long exposure. Consult medical personnel for first aid
and medical information.
SECTION VI - CORROSIVITY AND REACTIVITY DATA
STABILITY:
Unstable ( )
Stable (x)
POLYMERIZATION:
May occur ( )
Will not occur (x)
INCOMPATIBILITY (Materials to avoid)
n/a
HAZARDOUS COMPOSITIONS PRODUCTS:
n/a
CONDITIONS TO BE AVOIDED: Contact with strong acids/caustics; enclosed areas.
SECTION VII - SPILL, LEAK AND DISPOSAL PROCEDURES
STEPS TO BE TAKEN IN CASE MATERIAL IS RELEASED OR SPILLED:
Normal clean up procedure
WASTE DISPOSAL METHOD: Waste will contain nickel. Dispose in accordance with all applicable
federal, state, and local regulations.
SECTION VIII - PERSONAL PROTECTION INFORMATION
RESPIRATORY PROTECTION:
Respiratory protection as needed see OSHA 29 CFR 1910.134
VENTILATION:
LOCAL EXHAUST: strongly preferred
MECHANICAL (GENERAL): Use only if adequate to maintain below TLV’s.
PROTECTIVE GLOVES: As desired by user.
EYE PROTECTION: Recommended see OSHA 29 CFR 11910.215
OTHER PROTECTIVE EQUIPMENT: Use standard precautions for grinding operations.
SECTION IX - STORAGE AND HANDLING PROCEDURES
NORMAL STORAGE AND HANDLING: Store in clean, dry area, away from chemicals.
NORMAL USE: Use adequate ventilation (see Section VIII)
PAGE (1)
FORM OSHA-20
IMPORTANT SAFETY INSTRUCTIONS
REMEMBER, FOR YOUR OWN SAFETY, READ
INSTRUCTION MANUAL BEFORE OPERATING TOOL. Wear
Eye Protection. Never touch internal parts of the sharpener when
the sharpener is on. The rotating diamond grinding wheel can cause
injury. Use caution when replacing the grinding wheel. Follow
instructions entitled “Replacing The Grinding Wheel” in this
Instruction Manual. Regularly empty accumulated grinding dust.
Follow instructions entitled “Drill Doctor Maintenance” in this
Instruction Manual.
WARNING : WHEN USING ELECTRIC TOOLS, BASIC SAFETY
PRECAUTIONS INCLUDING THE FOLLOWING SHOULD
ALWAYS BE FOLLOWED TO PREVENT THE RISK OF FIRE,
ELECTRIC SHOCK AND PERSONAL INJURY.
1. KEEP GUARDS IN PLACE
2. REMOVE WRENCHES. Form a habit of checking to see that the
wrench is removed from tool before turning on.
3. KEEP WORK AREA CLEAN. Cluttered areas and benches invite
accidents.
4. DO NOT USE IN DANGEROUS ENVIRONMENT
Don’t use
power tools in damp or wet locations, avoid exposure to rain.
5. STORE EQUIPMENT in a safe place when not in use.
6. DON’T FORCE TOOL. It will do the job better and safer at the rate
for which it was designed.
7. USE RIGHT TOOL. Don’t force tool or attachment to do a job it was
not designed for.
8. ALWAYS USE SAFETY GLASSES. Also use face or dust mask if
cutting operation is dusty. Everyday eyeglasses only have impact
resistance lenses, they are NOT safety glasses.
9. MAINTAIN TOOL WITH CARE. Keep tools sharp and clean for best
and safest performance.
10. DISCONNECT TOOLS from the power supply before
servicing,when cleaning accessories.
11. AVOID ACCIDENTAL STARTING. Make sure switch is in “OFF “
position before plugging in.
12. USE RECOMMENDED ACCESSORIES.
13. CHECK FOR DAMAGED PARTS. Before further use of the tool, a
guard or other part that is damaged should be carefully checked to
assure that it will operate properly and perform its intended function.
Check for alignment of moving parts, binding of moving parts,break-
age of parts, mounting and any other conditions that may affect its
operation. A guard or other part that is damaged should be properly
repaired or replaced.
14. NEVER LEAVE TOOL RUNNING UNATTENDED.
15. USE PROPER EXTENSION CORD. Make sure extension cord is in
good condition. When using an extension cord be sure to use one
heavy enough to carry the current the Drill Doctor® will draw. An
undersized cord will cause a drop in line voltage, resulting in a loss of
power and/or overheating. Maximum cord length (5O ft), minimum
gauge (16). The smaller the gauge the heavier the cord.
DRILL DOCTOR
®
WARRANTY
Professional Tool Manufacturing LLC warranties your Drill
Doctor® to be free of defects due to workmanship and
design for 1 year following the first day of in service use.
For warranty service see warranty card instructions or con-
tact your authorized Drill Doctor® dealer.