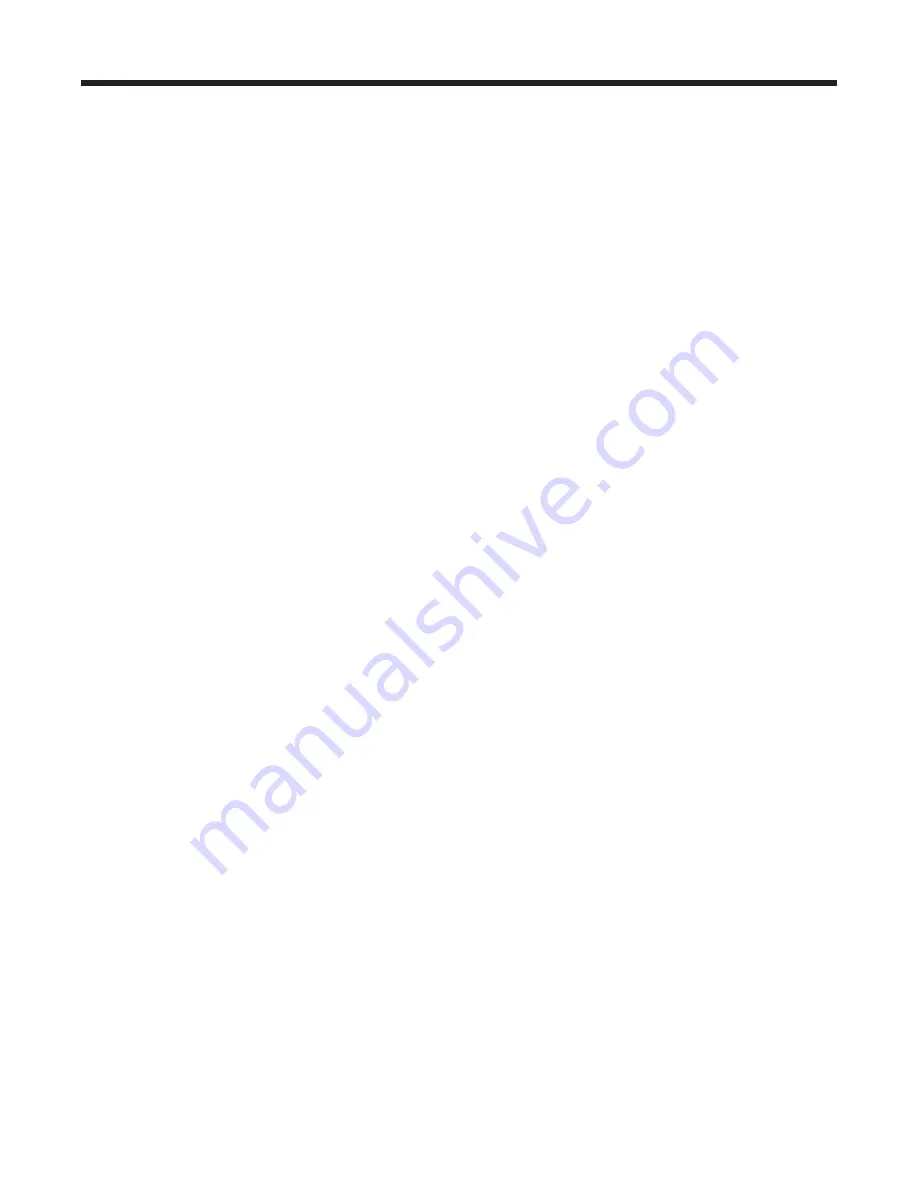
5
For your nearest Roots office contact information, please consult the last page of this document.
ROOTS blowers & exhausters are treated after factory
assembly to protect against normal atmospheric corrosion.
The maximum period of internal protection is considered to
be one year under average conditions, if shipping plugs &
seals are not removed. Protection against chemical or salt
water atmosphere is not provided. Avoid opening the unit
until ready to start installation, as corrosion protection will
be quickly lost due to evaporation.
If there is to be an extended period between installation and
start up, the following steps should be taken to ensure corro-
sion protection. See “Cleaning & Preservation” on pages 17
and 18 for DVJ and DPJ units.
J
Coat internals of cylinder, gearbox and drive end bearing
reservoir with Nox-Rust VCI-10 or equivalent. Repeat
once a year or as conditions may require. Nox-Rust VCI-
10 is petroleum soluble and does not have to be
removed before lubricating. It may be obtained from
Daubert Chemical Co., 2000 Spring Rd., Oak Brook, Ill.
60521.
J
Paint shaft extension, inlet and discharge flanges, and all
other exposed surfaces with Nox-Rust X-110 or equiva-
lent.
J
Seal inlet, discharge, and vent openings. It is not recom-
mended that the unit be set in place, piped to the sys-
tem, and allowed to remain idle for extended periods. If
any part is left open to the atmosphere, the Nox-Rust
VCI-10 vapor will escape and lose its effectiveness.
J
Protect units from excessive vibration during storage.
J
Rotate shaft three or four revolutions every two weeks.
J
Prior to start up, remove flange covers on both inlet and
discharge and inspect internals to insure absence of
rust. Check all internal clearances. Also, at this time,
remove gearbox and drive end bearing cover and inspect
gear teeth and bearings for rust.
Because of the completely enclosed unit design, location of
the installation is generally not a critical matter. A clean, dry
and protected indoor location is preferred. However, an out-
door location will normally give satisfactory service.
Important requirements are that the correct grade of lubricat-
ing oil be provided for expected operating temperatures, and
that the unit be located so that routine checking and servic-
ing can be performed conveniently. Proper care in locating
driver and accessory equipment must also be considered.
Supervision of the installation by a Roots Service Engineer is
not usually required for these units. Workmen with experi-
ence in installing light to medium weight machinery should
be able to produce satisfactory results. Handling of the
equipment needs to be accomplished with care, and in com-
pliance with safe practices. Unit mounting must be solid,
without strain or twist, and air piping must be clean, accu-
rately aligned and properly connected.
Bare-shaft Units:
Two methods are used to handle a unit
without base. One is to use lifting lugs bolted into the top
Installation
of the unit headplates. Test them first for tightness and
fractures by tapping with a hammer. In lifting, keep the
direction of cable pull on these bolts as nearly vertical as
possible. If lifting lugs are not available, lifting slings may
be passed under the cylinder adjacent to the headplates.
Either method prevents strain on the extended drive shaft.
Packaged Units:
When the unit is furnished mounted on a
baseplate, with or without a driver, use of lifting slings pass-
ing under the base flanges is required. Arrange these slings
so that no strains are placed on the unit casing or mounting
feet, or on any mounted accessory equipment.
DO NOT
use
the lifting lugs in the top of the unit headplates.
Before starting the installation, remove plugs, covers or seals
from unit inlet and discharge connections and inspect the
interior completely for foreign material. If cleaning is
required, finish by washing the cylinder, headplates and
impeller thoroughly with an appropriate solvent. Turn the
drive shaft by hand to make sure that the impellers turn
freely at all points. Anti-rust compound on the connection
flanges and drive shaft extension may also be removed at
this time with the same solvent. Cover the flanges until ready
to connect piping.
Mounting
Care will pay dividends when arranging the unit mounting.
This is especially true when the unit is a “bare-shaft” unit
furnished without a baseplate. The convenient procedure
may be to mount such a unit directly on a floor or small con-
crete pad, but this generally produces the least satisfactory
results. It definitely causes the most problems in leveling and
alignment and may result in a “Soft Foot” condition. Correct
soft foot before operation to avoid unnecessary loading on
the casing and bearings. Direct use of building structural
framing members is not recommended.
For blowers without a base, a well anchored and carefully
leveled steel or cast iron mounting plate is recommended.
The plate should be at least 1 inch (25 mm) thick, with its
top surface machined flat, and large enough to provide level-
ing areas at one side and one end after the unit is mounted.
It should have properly sized studs or tapped holes located
to match the unit foot drilling. Proper use of a high quality
machinist’s level is necessary for adequate installation.
With the mounting plate in place and leveled, set the unit on
it without bolting and check for rocking. If it is not solid,
determine the total thickness of shims required under one
foot to stop rocking. Place half of this under each of the
diagonally-opposite short feet, and tighten the mounting
studs or screws. Rotate the drive shaft to make sure the
impellers turn freely. If the unit is to be direct coupled to a
driving motor, consider the height of the motor shaft and the
necessity for it to be aligned very accurately with the unit
shaft. Best unit arrangement is directly bolted to the mount-
ing plate while the driver is on shims of at least 1/8 inch
(3mm) thickness. This allows adjustment of motor position
in final shaft alignment by varying the shim thickness.
Aligning
When unit and driver are factory mounted on a common
baseplate, the assembly will have been properly aligned and