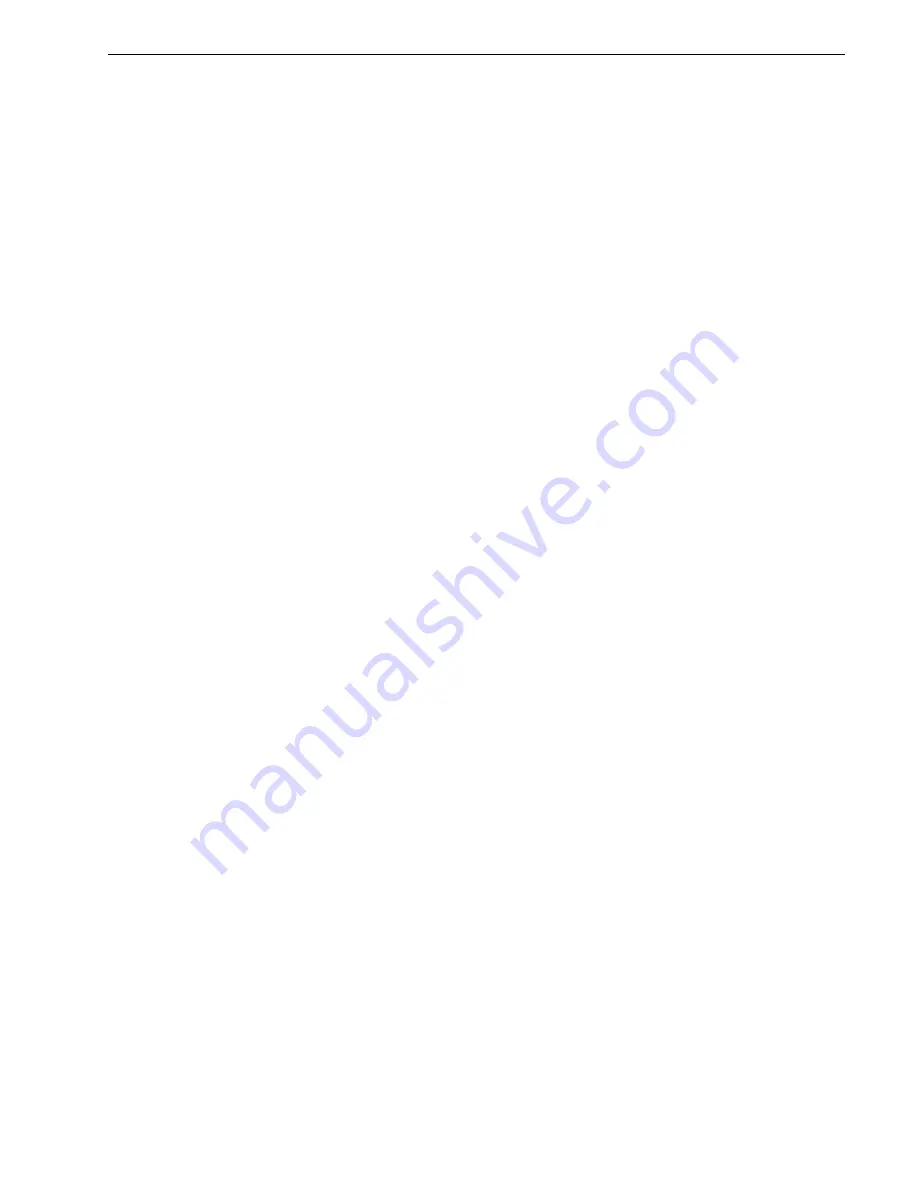
CON-2
Page 29
Specific Steps
Use the following procedure to determine the
correct limit washer length.
1.
Assemble the disc and holder (installing the
bellows gasket and bellows, if applicable).
Place the guide over the disc holder barrel;
then connect the spindle to the disc holder.
(Install the eductor tube in base, if applicable.)
Then, install the adjusting ring below the
seat.
2.
Install the guide gasket and insert the
assembly, from Step 1, above, into the base.
3.
Install the bonnet gasket and bonnet (leaving
out the spring assembly at this time).
4.
Tighten the nuts to compress the gasket.
(Do not use an impact wrench on bellow
valves.)
5.
Place a dial lift indicator on the bonnet and
over the spindle, then zero the indicator.
6.
Measure the total lift by pushing the disc
upward.
X. (Continued)
7.
Subtract the required lift of the valve from the
measured lift, to find the required limit washer
length.
8.
Machine the limit washer to the required
length. Next, machine the inside chamfer,
then deburr and polish, as required.
9.
Disassemble the valve, install the limit washer
(with chamfer down), and prepare to
reassemble the valve. Measure the actual
lift of the valve, and compare it with the
required lift for the valve, per the note above.
10. a. If the actual lift is less than required,
machine the lift washer the additional
amount necessary to obtain the required
lift. (Machine, chamfer and deburr, before
installation into the valve.)
b. If the actual lift is greater than the required
amount, obtain a new limit washer, and
begin again with Step 7, above. (Again,
machine, chamfer and deburr, before
installation into valve.)
11. Remove the bonnet and install the spring
assembly; then, reinstall the bonnet and
tighten the stud nuts.
12. The valve is now ready for setting and testing.
NOTES:
•
The limit washer must be chamfered to fit
over the radius on the disc holder. This
chamfered end must be located down,
next to the backface of disc holder, when
assembled.
•
For bellows Type "D" and "E" valves, the
limit washer must be chamfered on the
lower end, to remove the knife edge of the
cut off. For bellow valves, the outside
diameter must also be checked, and
emery clothed down to .680” or 17.3 mm
maximum diameter, in order to avoid any
interference with the bellows threads.
•
Be sure of all dimension requirements
for each valve. Do not interchange
internal parts, or use a different base,
after a set of parts has been custom-fit.
XI. Reassembly
A.
General Information
The Type 1900 Safety Relief Valve can be easily
re-assembled after the required maintenance of
internal parts has been performed. (Again, refer
to Figures 1-6, on pages 6 and 7, for parts
nomenclature.) All parts should be clean prior to
assembly. Special attention should be given to
guiding surfaces, bearing surfaces, flange faces,
retainer recesses and grooves. See Section
XVII for Recommended Compounds and Tools.
NOTES:
•
Check all gaskets used during re-
assembly. Undamaged solid metal
gaskets (not pitted or creased) can be
reused. All soft gaskets must be replaced.
Before placing the (flat) gaskets, apply a
light uniform coating of lubricant to the
surface to be gasketed; then coat the top
of the gasket with lubricant.
•
If grinding in of bearing parts was
necessary, be sure to remove all grinding
compound; then, thoroughly clean both
surfaces and rinse with alcohol or another
suitable cleaner.
•
With regard to restricted lift valves, be
sure to measure the required lift before
final assembly. (See Paragraph X.L. for
instructions.)
•
The last step before final assembly is
lubrication. Apply lubricants sparingly,
but be sure that each bearing surface is
lightly (yet uniformly) covered.