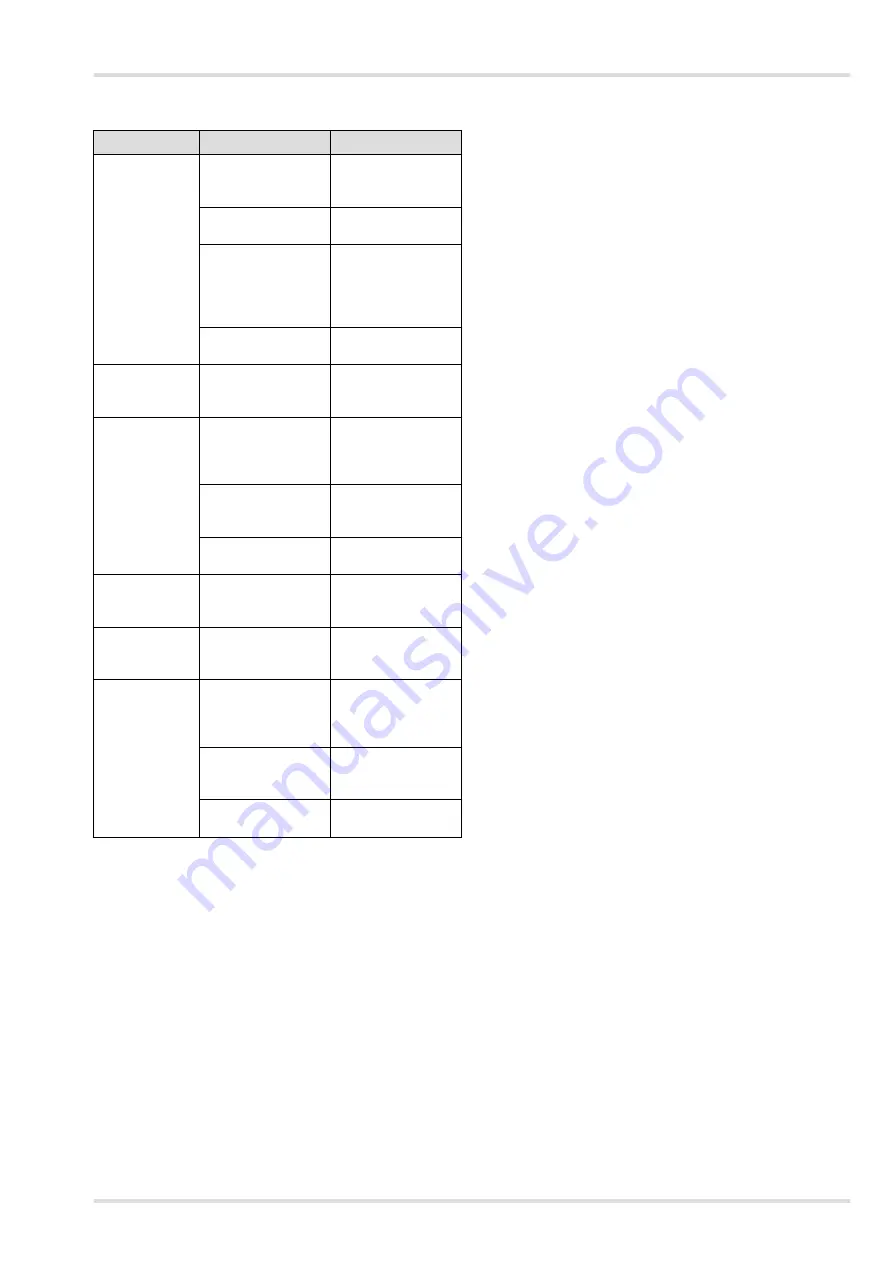
Troubleshooting
Dräger Oxygen Booster 200 ECO
23
4
Troubleshooting
5
Maintenance
5.1
Service intervals
Observe the following maintenance intervals and shorten if
necessary, if the filling times are extended by 20 % under
comparable conditions (gas supply pressure, volume of the
compressed gas container to be filled, ambient temperature).
Only allow maintenance measures to be carried out by
authorized expert personnel.
Once a day before use or after every transport of the DOB
200 ECO:
Leak test of the entire DOB 200 ECO (see "Leak test" on
Every 25 operating hours:
Checking the safety valve (see "Checking the safety valve"
Every 100 operating hours or every 6 months:
Checking the screen inserts and sealing rings of all
connections (see "Checking the screen inserts and sealing
rings for the DOB 200 ECO, the filling panel and the tube
Leak test on all tube lines and connections conducted by
authorized expert personnel.
Every 200 operating hours or annually:
Check on the drive elements carried out by authorized
expert personnel.
Check of the piston seal carried out by qualified expert
personnel.
Every 1000 operating hours or every 5 years:
Major overhaul by authorized expert.
5.2
Maintenance and repair work
Leak test
The leak test requires a gas supply with at least 150 bar/
2200 psi and max. 200 bar/2900 psi (type A) or 207 bar/
3000 psi (type B) filling pressure.
The leak test of the DOB 200 ECO should be carried out as
follows:
1. Ensure that the steps from chapter "Preparations for use"
on page 20 have been carried out.
2. If a filling panel is used, make sure the steps from chapter
"Mounting the filling panel" on page 20 have been taken.
3. Ensure that any compressed gas containers connected are
closed. The compressed gas containers are closed when
their shut-off valves cannot be turned any further to the
right.
4. Slowly open the shut-off valve on the gas supply.
5. Slowly turn the filling valve (fig. 1, pos. 4) to the left and
open fully.
6. Read off the pressure displayed on the inlet pressure
gauge (fig. 1, pos. 2) and on the filling pressure gauge (fig.
1, pos. 5).
7. The pressure displayed must be at least 150 bar/2200 psi.
8. Close the shut-off valve on the gas supply.
9. Wait for 5 minutes.
10. Read off the pressure again on the input pressure gauge
and on the filling pressure gauge. The leak test is
successful when no more than 10 bar/145 psi pressure
drop is displayed on the input pressure gage and on the
filling pressure gage than at the start of the test.
11. De-pressurize the DOB 200 ECO as described in chapter
12. If the pressure drop on the inlet pressure gauge and on the
filling pressure gauge is more than 10 bar/145 psi, the
tubes and all connections on the DOB 200 ECO must be
tested for leaks. Damaged hoses and connections are not
permitted for use. All leaky connections must be replaced
by authorized expert personnel. Until that point, the DOB
200 ECO is not permitted to be used.
Error
Cause
Remedy
No filling
pressure is
generated.
Incorrect connection
to the gas supply.
Ensure a correct
connection to the
gas supply.
Pump is not working. Restore the power
supply.
Safety valve open or
leaking.
Run a function on the
safety valve and
contact an
authorized expert if
necessary.
Shut-off valve on the
gas supply closed.
Ensure that the shut-
off valve is open.
The shut-off
valve is fully
open.
End pressure
shutdown not
functioning.
Contact an
authorized expert.
No input
pressure is
displayed.
Shut-off valve on the
gas supply closed.
Ensure a correct
connection to the
gas supply and open
the shut-off valve.
Gas supply is not
delivering sufficient
pressure.
Ensure a gas supply
of at least 50 bar/
750 psi pressure.
Input pressure
gauge faulty.
Contact an
authorized expert.
No filling
pressure is
displayed.
Filling pressure
gauge faulty.
Contact an
authorized expert.
Gas is leaking
out of the DOB
200 ECO.
Connections are not
gas-tight.
Contact an
authorized expert.
The filling
pressure is too
low.
Ambient temperature
too high.
Observe the
maximum
permissible ambient
temperature.
Gas supply is not
delivering sufficient
pressure.
Ensure a gas supply
of at least 50 bar/
750 psi pressure.
Leak in the piston
seals.
Contact an
authorized expert.