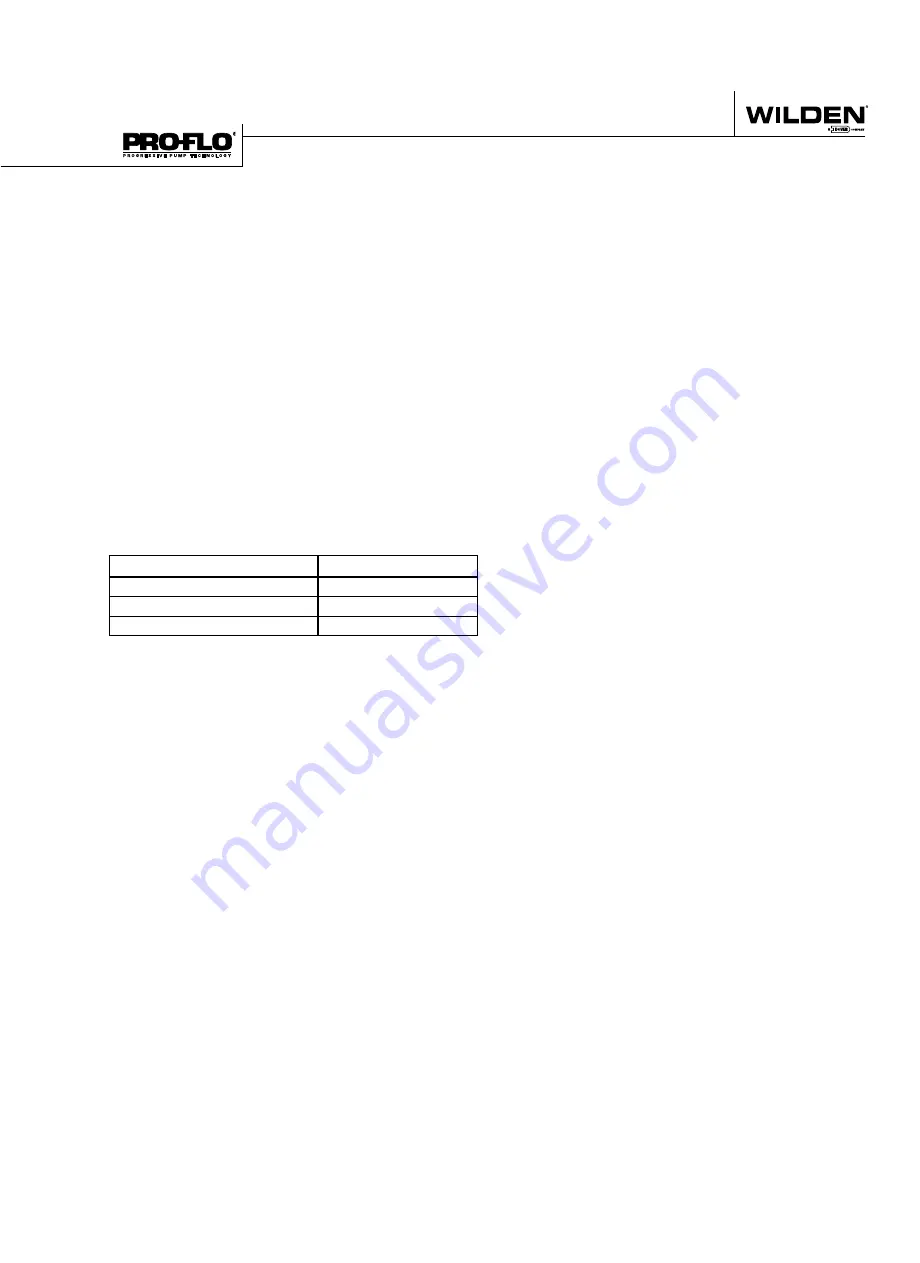
WIL-11181-E-04
13
WILDEN PUMP & ENGINEERING, LLC
ASSEMBLY:
Upon performing applicable maintenance to the air distribution
system, the pump can now be reassembled. Please refer to
the disassembly instructions for photos and parts placement.
To reassemble the pump, follow the disassembly instructions in
reverse order. The air distribution system needs to be assem-
bled first, then the wetted path. Please find the applicable
torque specifications on this page. The following tips will assist
in the assembly process.
• Clean the inside of the center section shaft bore to ensure
no damage is done to new seals.
• Stainless bolts should be lubed to reduce the possibility of
seizing during tightening.
• Apply a small amount of Loctite
®
242 to the shaft stud
threads.
• To aid in removal of the liquid chambers, place pump on
its side.
S e c t i o n 5
R E A S S E M B L Y H I N T S & T I P S
MAXIMUM TORQUE SPECIFICATIONS
Description of Part
Torque
Air Valve, Pro-Flo
®
2.8 N•m [25 in.-lbs.]
Combo Manifold Plate
13.5 N•m [10 ft.-lbs.]
Liquid Chamber
13.5 N•m [10 ft.-lbs.]
Содержание Wilden Advanced H38
Страница 18: ...N O T E S ...
Страница 19: ......