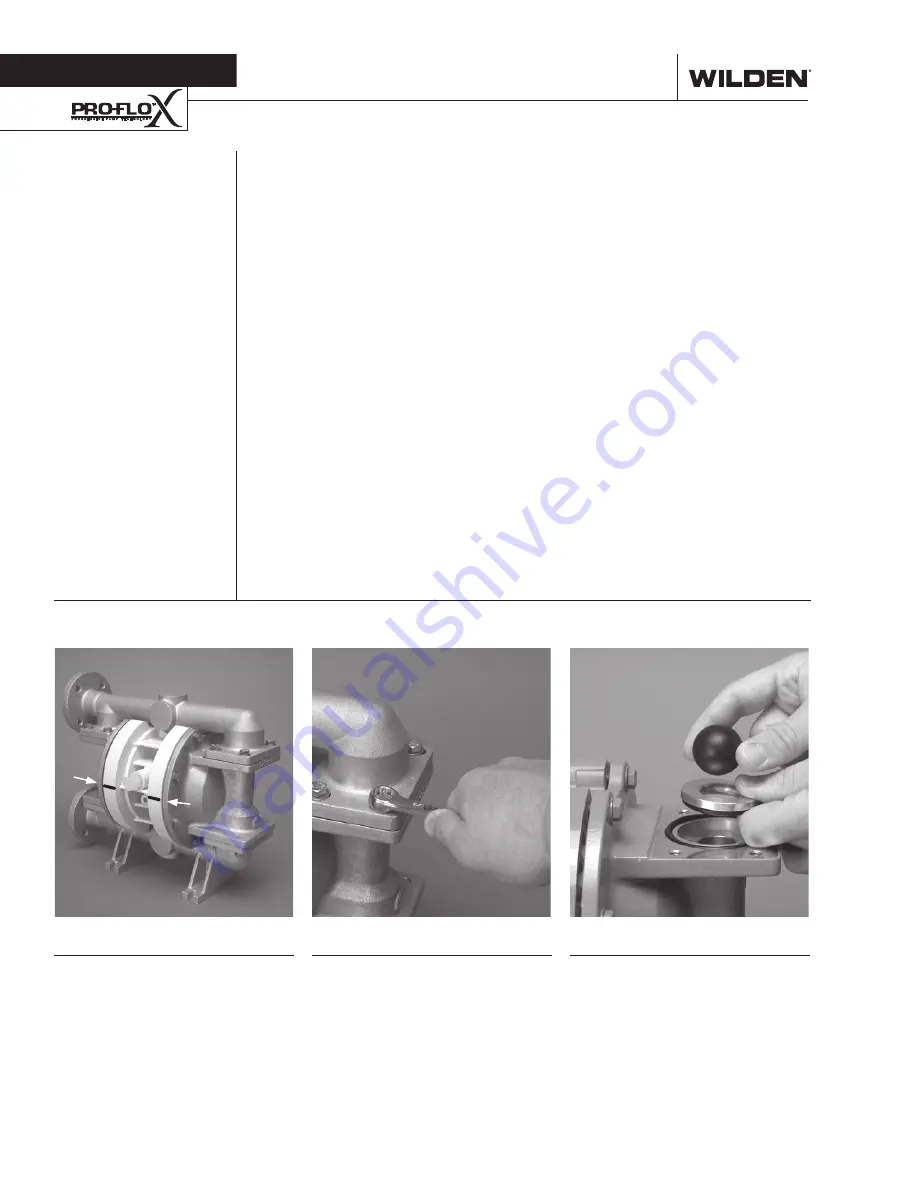
WILDEN PUMP & ENGINEERING, LLC
20
WIL-11610-E-02
To o l s R e q u i r e d :
• 13 mm (1/2") Box
Wrench
• 2 – 25 mm (1") Sockets
or Adjustable Wrench
• Adjustable Wrench
• Vise equipped with
soft jaws (such as
plywood, plastic
or other suitable
material)
CAUTION: Before any maintenance or repair is attempted, the compressed air line
to the pump should be disconnected and all air pressure allowed to bleed from the
pump. Disconnect all intake, discharge and air lines. Drain the pump by turning it
upside down and allowing any fluid to flow into a suitable container. Be aware of
any hazardous effects of contact with your process fluid.
NOTE: The model used for these instructions incorporates rubber diaphragms and
balls. Models with PTFE diaphragms and balls are the same except where noted.
Step 1
Please note alignment marks on
center section. Use to properly align
liquid chamber to center section.
Step 2
Using a 13 mm (1/2") wrench,
loosen the discharge manifold from
the liquid chambers.
Step 3
Remove the discharge manifold to
expose the valve balls, valve seats
and valve seat O-rings.
S e c t i o n 7
P U M P D I S A S S E M B L Y
Содержание PSG Wilden PX220
Страница 1: ...PX220 PX230 Metal Pump EOM Engineering Operation Maintenance wildenpump com Where Innovation Flows ...
Страница 8: ...S e c t i o n 5 B N O T E S ...
Страница 9: ...P X 2 2 0 P X 2 3 0 P E R F O R M A N C E PX220 PX230 M E T A L ...
Страница 29: ...N O T E S ...
Страница 33: ...N O T E S ...
Страница 34: ...N O T E S ...